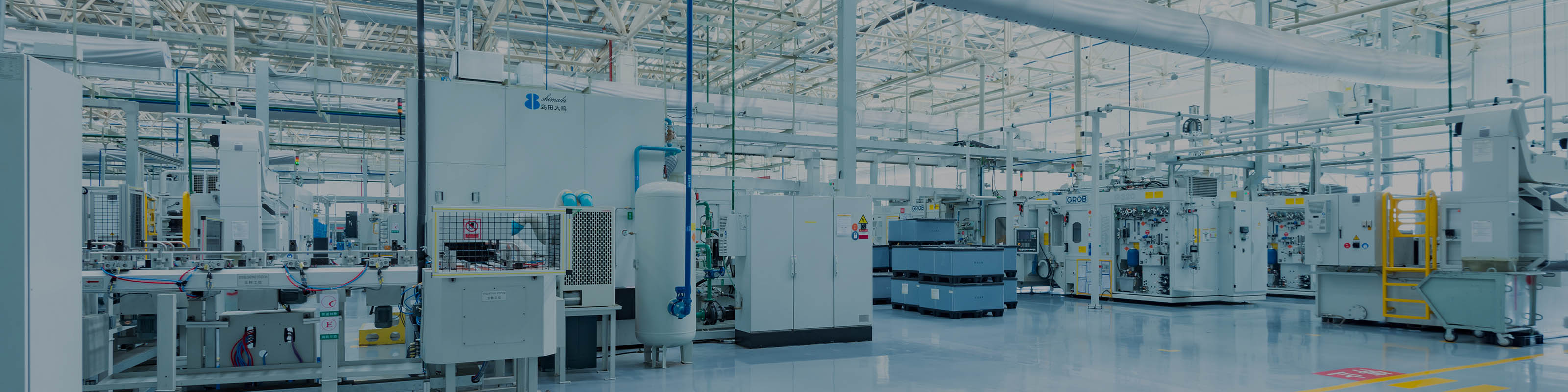
Quality Control Case Study Utilizing IoT Technology at Abel Co., Ltd.
Development of Quality Control Image System Utilizing Image Detection Technology
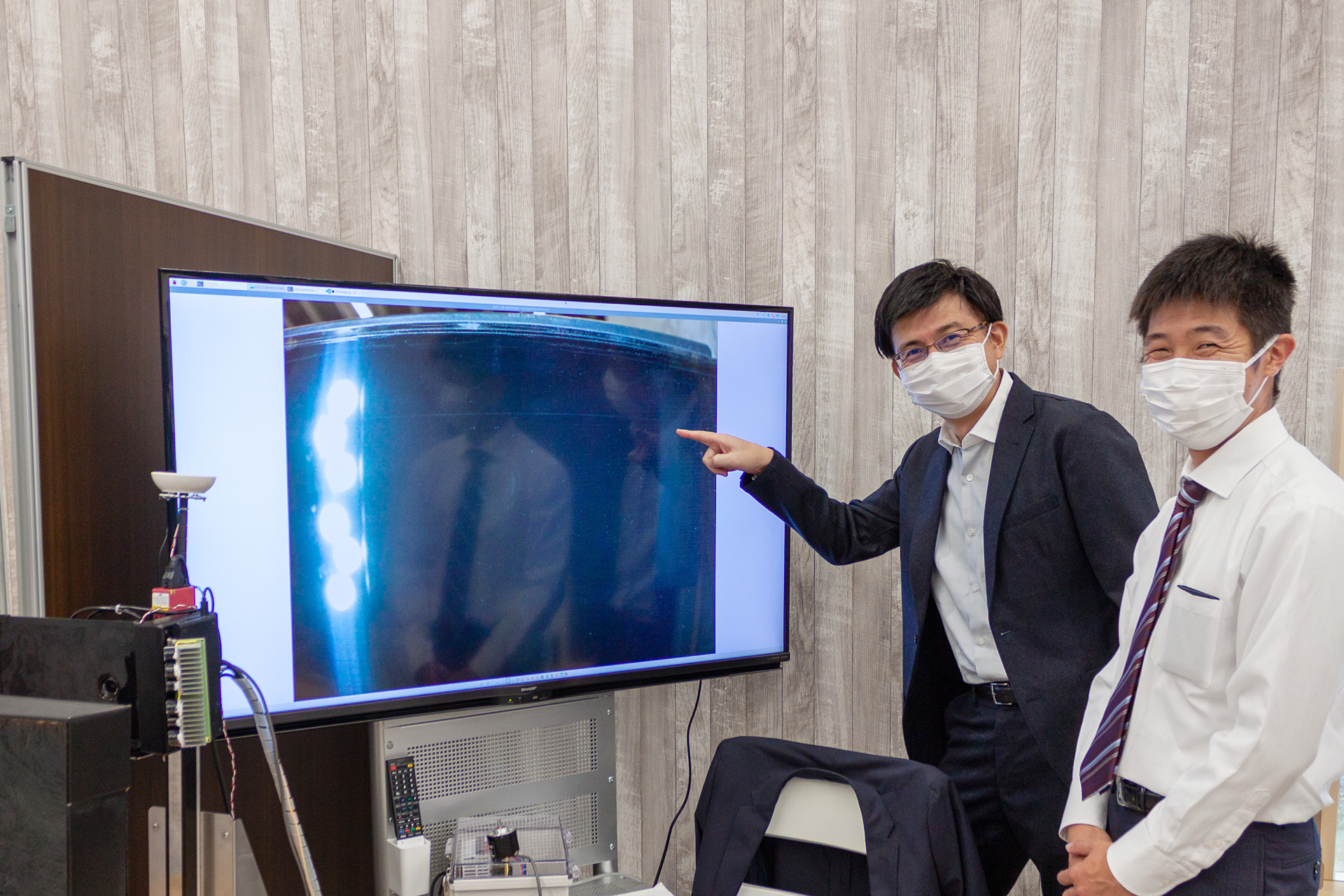
Purpose of Introducing IoT System
- Reduction of the visual inspection workload of inspectors
- Development of an appropriate quality control system
Our Areas of Responsibility
- System planning and design
- Development of IoT devices
- Technical guidance for in-house production
- Planning and support for machine learning and AI introduction
The Voice of Abel Co., Ltd.
A Solid Quality Control System.
For the Fate of the Manufacturing Companies.
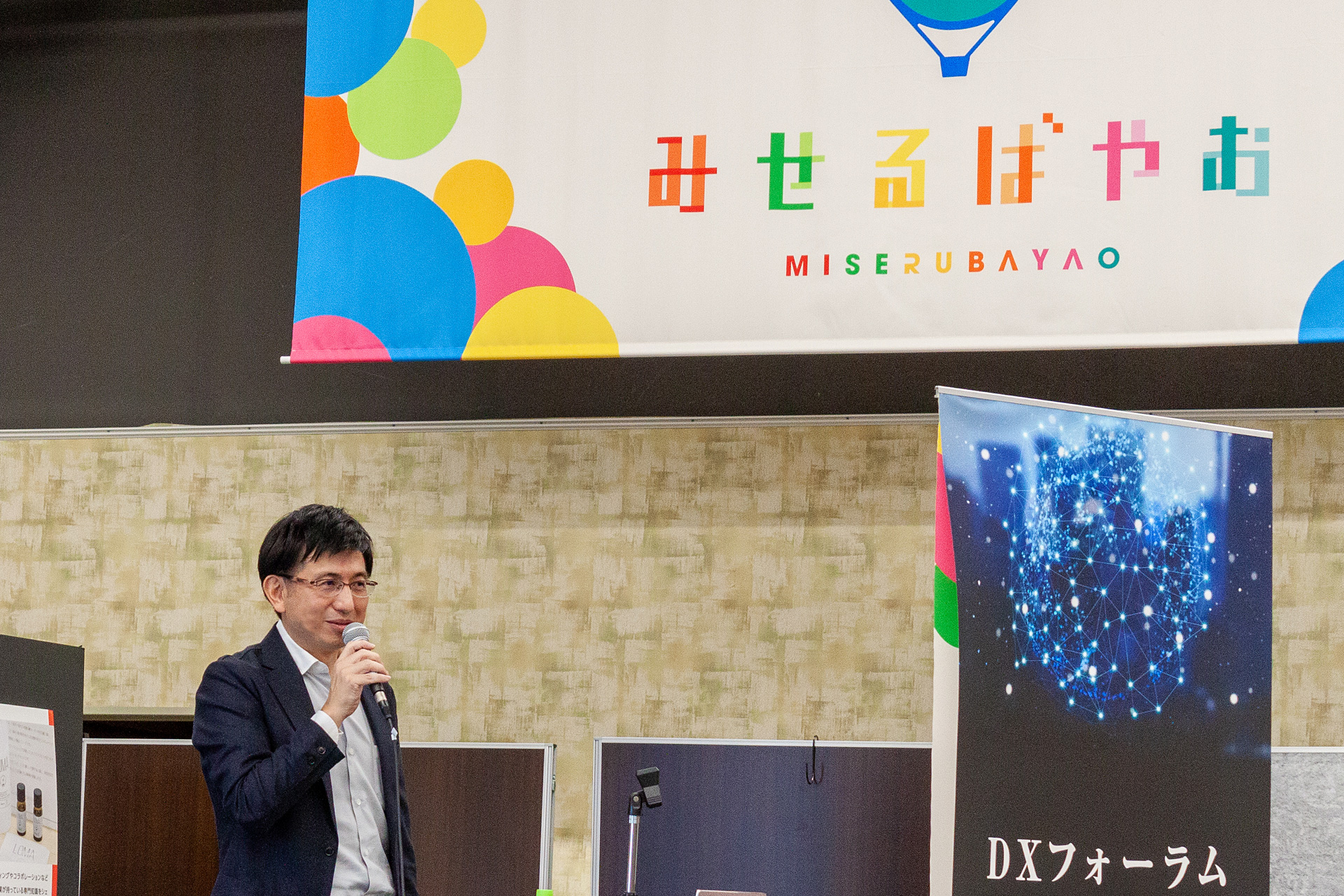
Our company, which started its business as a stainless steel surface treatment, has refined its stainless steel coloring technology for over 50 years. Our main product is the “Abel Black”. “Abel Black” is black stainless steel material with excellent functionality and design. We use our unique technology to color stainless steel materials while retaining the original texture of metal that will be lost if painted or plated. This technology, which utilizes light interference to recognize colors, has made possible a profoundly beautiful black color that has never been seen before.
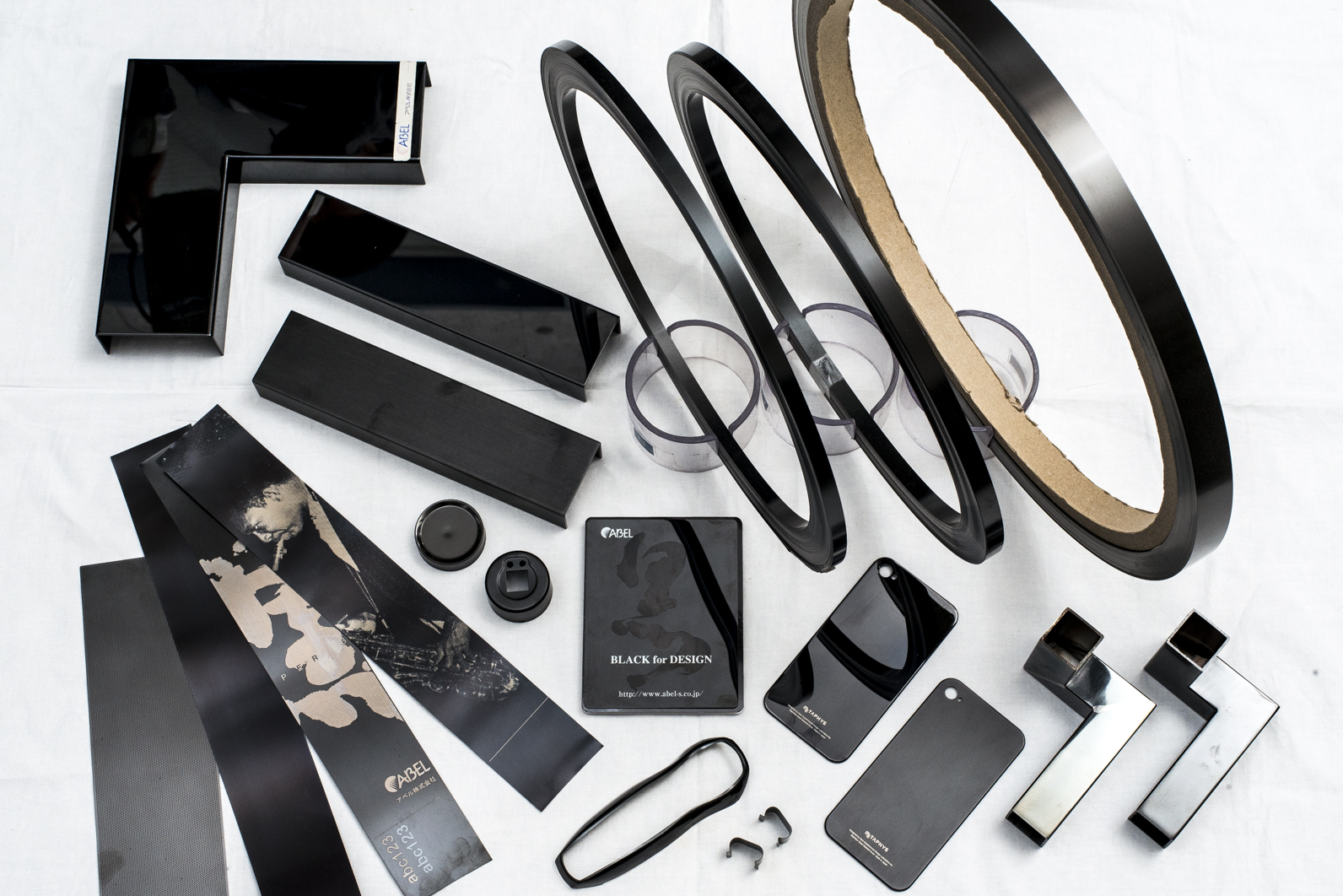
The look that appears deep is used in the interior and exterior of stores, home appliances, and automobile parts, where a sense of luxury is desired. The excellent anti-reflection effect is applied to the field frames, aperture blades, and shading plates of a camera. The excellent corrosion resistance and weather resistance which eliminate the worry of peeling off, are suitable for all-weather exteriors, semiconductor parts, and urban infrastructure components. The world’s only coloring technology, “Abel Black,” is used in various areas such as construction, optical equipment, automobiles, and medical equipment.
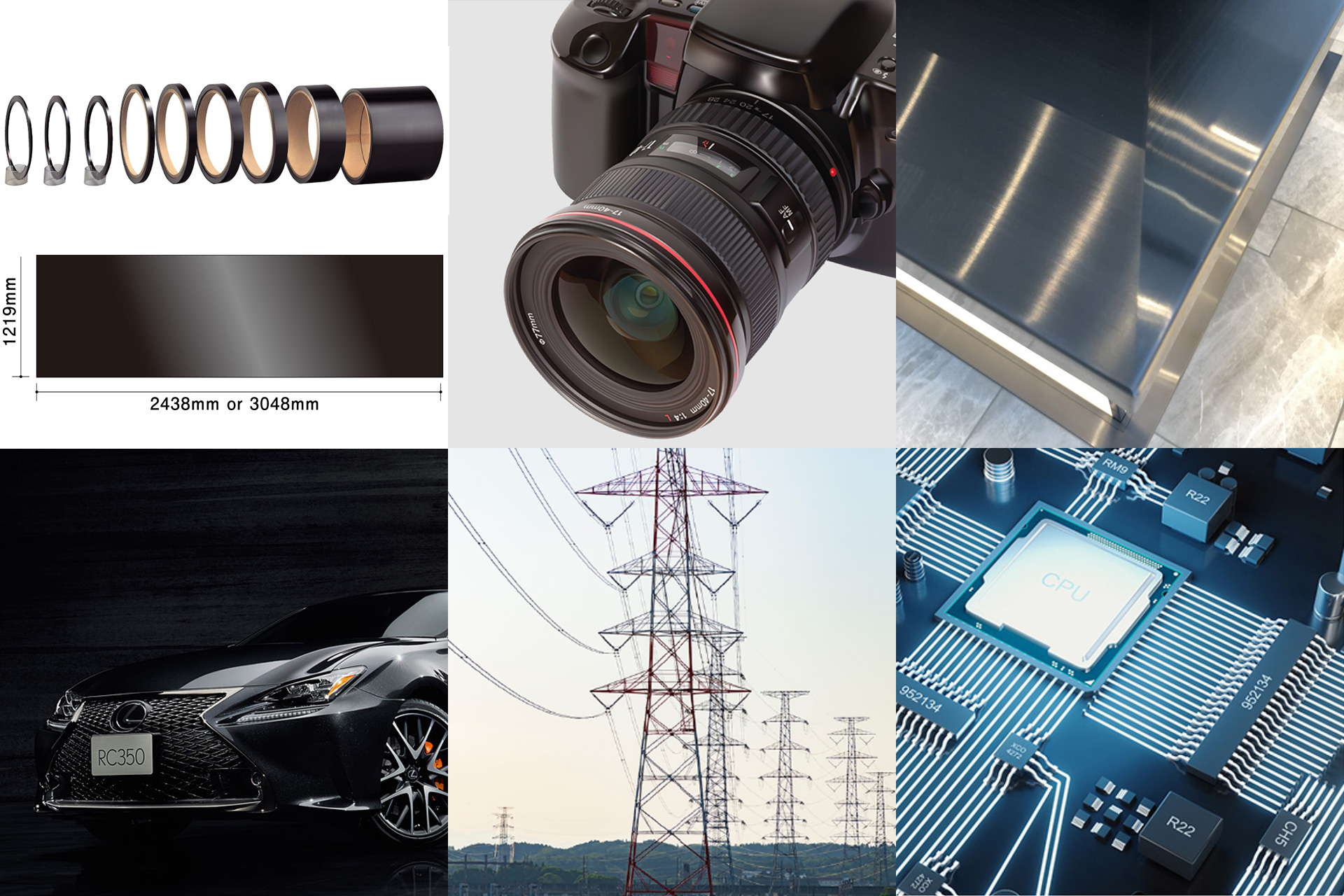
Proper quality control is an important factor in developing and manufacturing excellent products. We are constantly improving our management and inspection system for maintaining product quality and improving them. The surface inspection process of the product was one of the biggest bottlenecks in our quality control efforts. It is a rigorous work requiring two people irradiating light to visually check for scratches for over 8 hours.
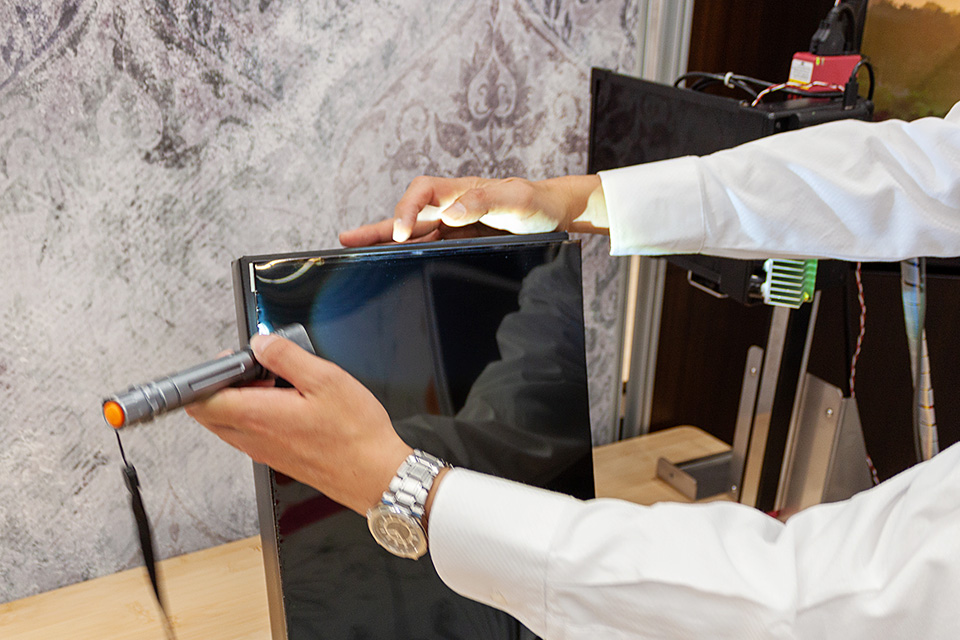
The eyes and the body get tired, and the tension to maintain concentration and quality is immeasurable. We had the desire to reduce the burden on the inspectors somehow.
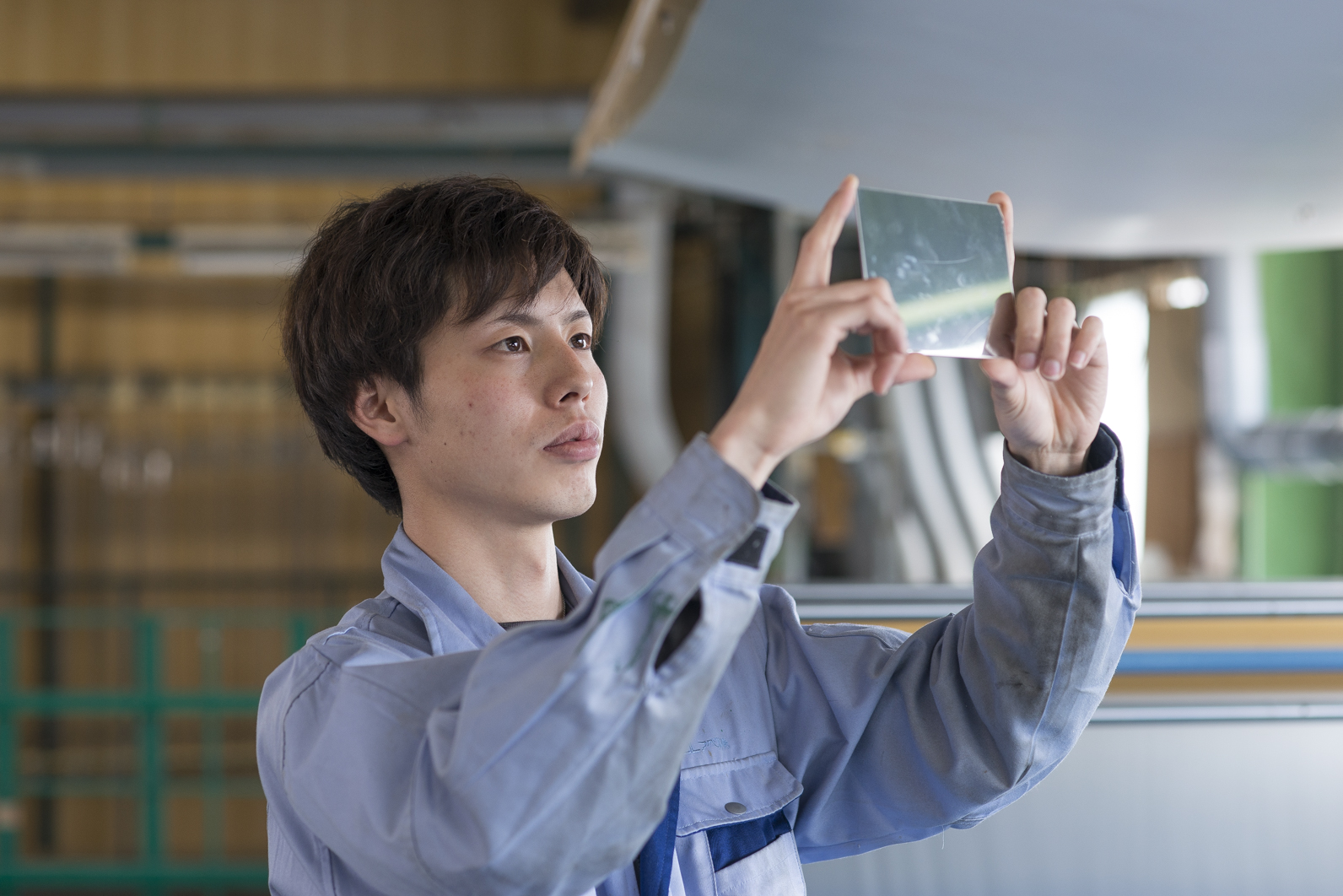
The quality control image system that we are developing in collaboration with eftax will bring revolution in such a situation. This project started with a proposal from Mr. Kobayashi of eftax. After Mr. Kobayashi trained our employees to develop and operate IoT devices and systems, we are currently conducting test operations. In the future, we plan to expand into machine learning and AI based on the accumulated image data.
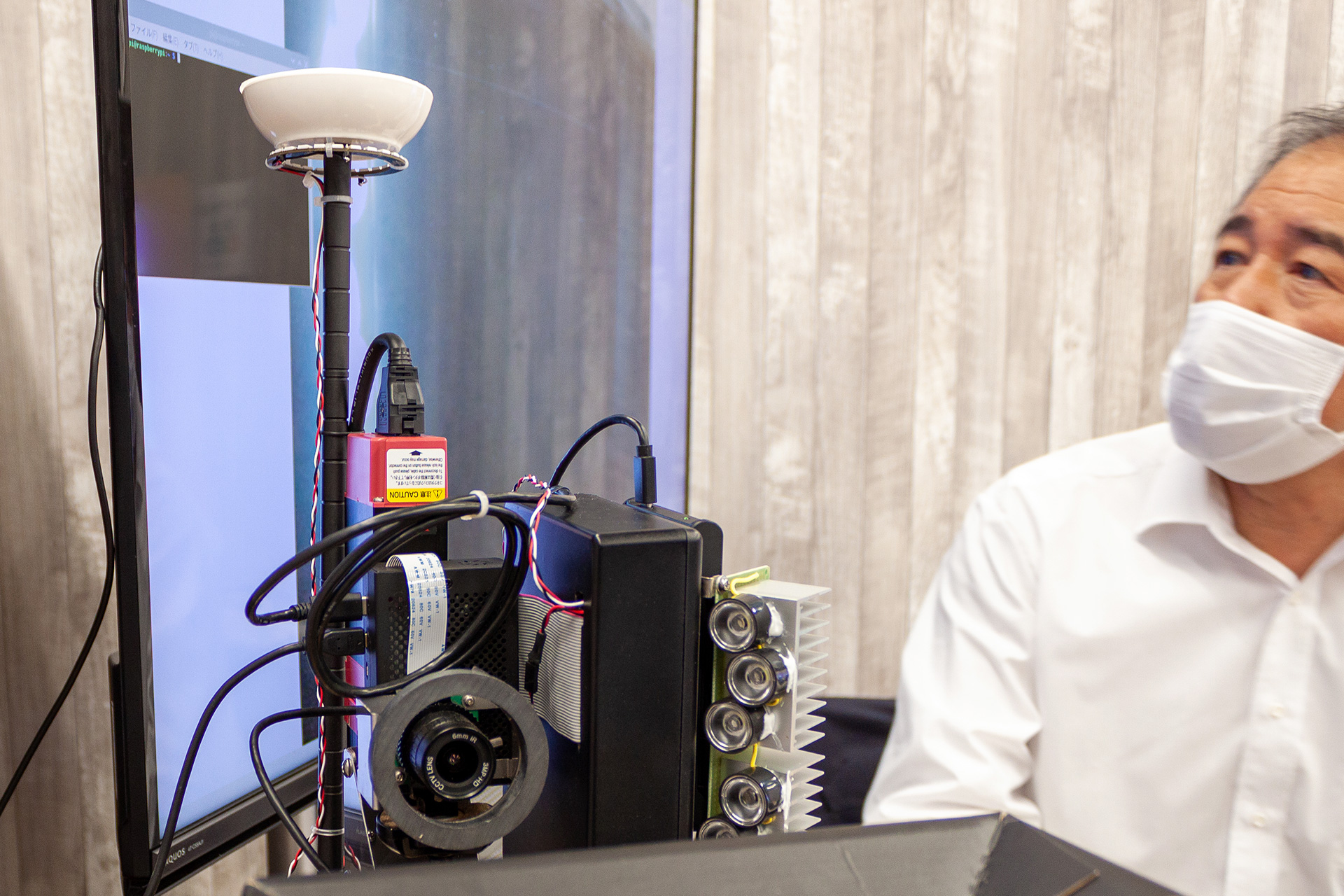
A Collaboration that was Born at an Ideathon.
Solving Bottlenecks with IT.
Before joining Abel Corporation and becoming its president and the representative director, I worked for an IT company that develops software on a contract basis. When I joined Abel Corporation in 2004, I was surprised at how various things were analog and paper-based. I said to myself, “I have to do something about it,” and embarked on reforms.
Among the efforts, such as the introduction of customer management tools and the shift to paperlessness, there were many measures that failed because they did not penetrate the company. I joined a manufacturing community, “Miserubayao” in Yao City, Osaka, from the start of its establishment. I have been participating in its IT study sessions and events, working together with the local manufacturing companies to promote DX initiatives.
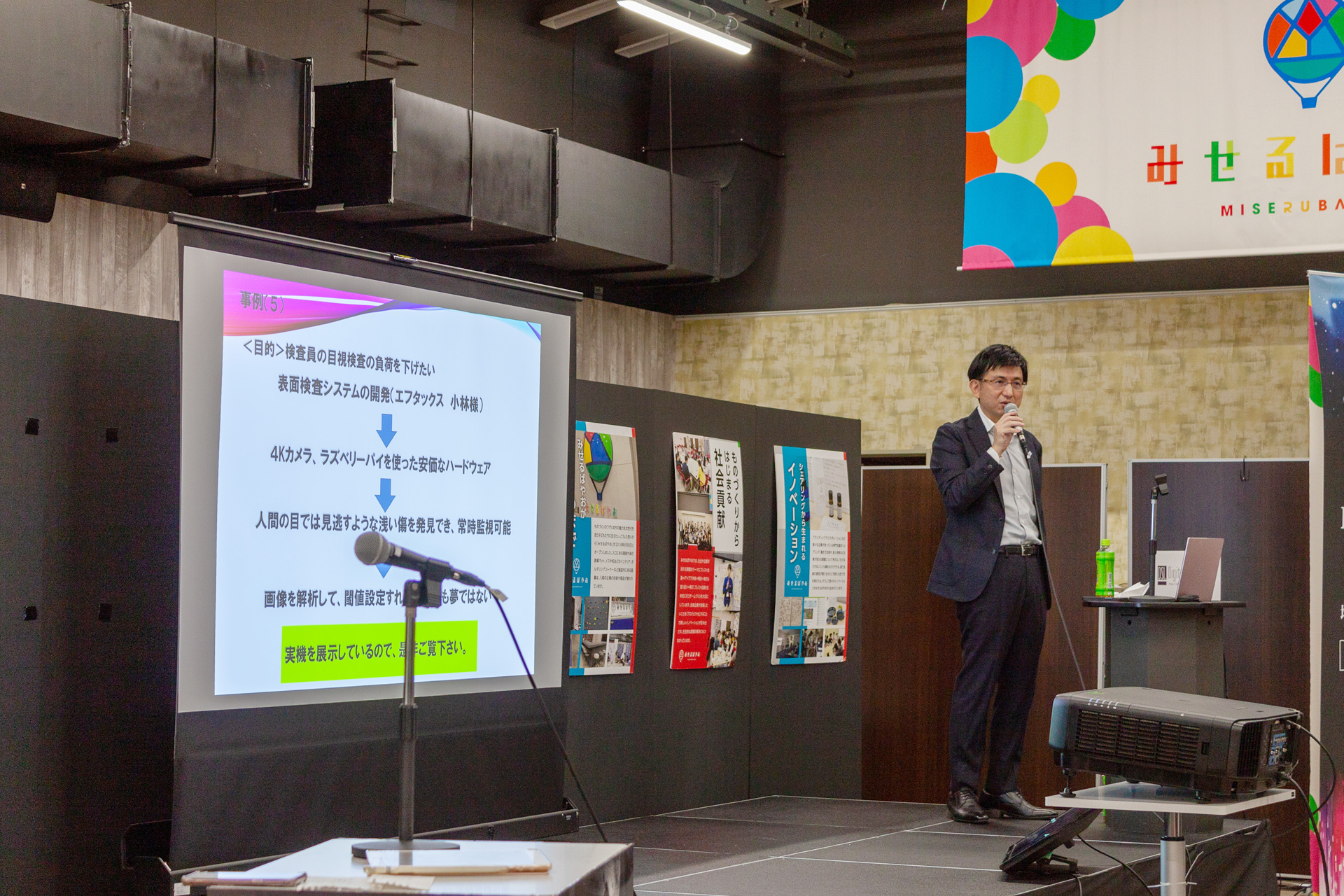
As part of the program organized by Miserubayao, I participated in the “Site Tour Ideathon,” a company visit event. This on-site tour triggered the start of the quality control image system development project.
As a matter of fact, this is the first attempt to open our manufacturing and inspection site to the public. Many employees were confused about showing the backbone of the company. However, by doing so, we discovered opportunities for improving the quality control system and promoting digital transformation, which we were not aware of.
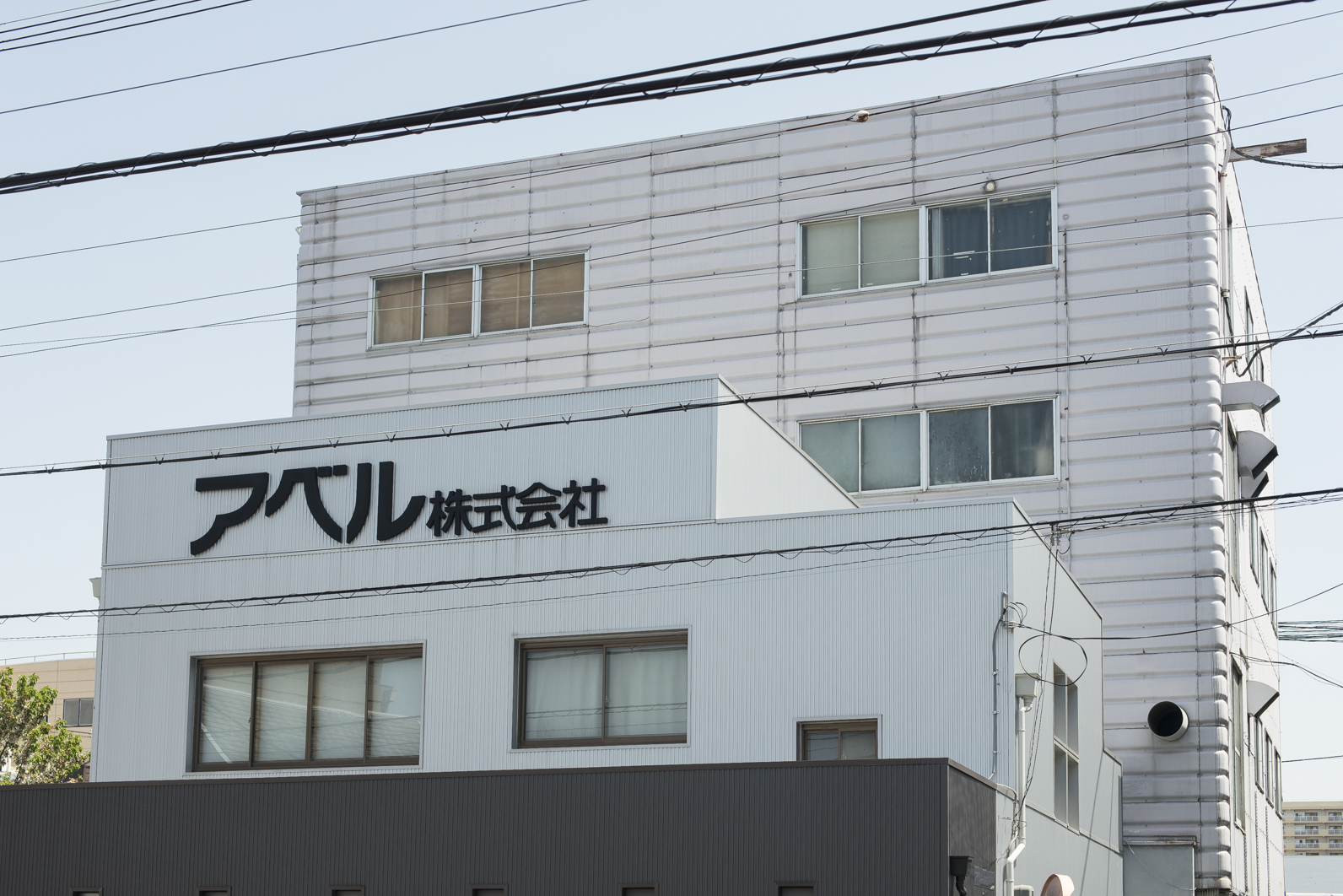
During the tour, I was asked about the process that was a bottleneck, and I mentioned the visual inspection of the product surface. We have also had a bitter past of outsourcing the production of a machine that can perform surface inspections that ended up being useless.
Then, Mr. Kobayashi, the general manager of eftax’s IoT promotion division, told us he could produce the system. I also learned about technological advancements such as high-resolution 4K cameras that I didn’t know about. I realized that the hurdles might not be as high as I had expected.
In addition, he also said, “I will teach your staff how to make changes to the programming of the system.” Outsourcing done in the past had cases where adaptability after delivery failed, so a system that we could create together was very attractive and a huge deciding factor.
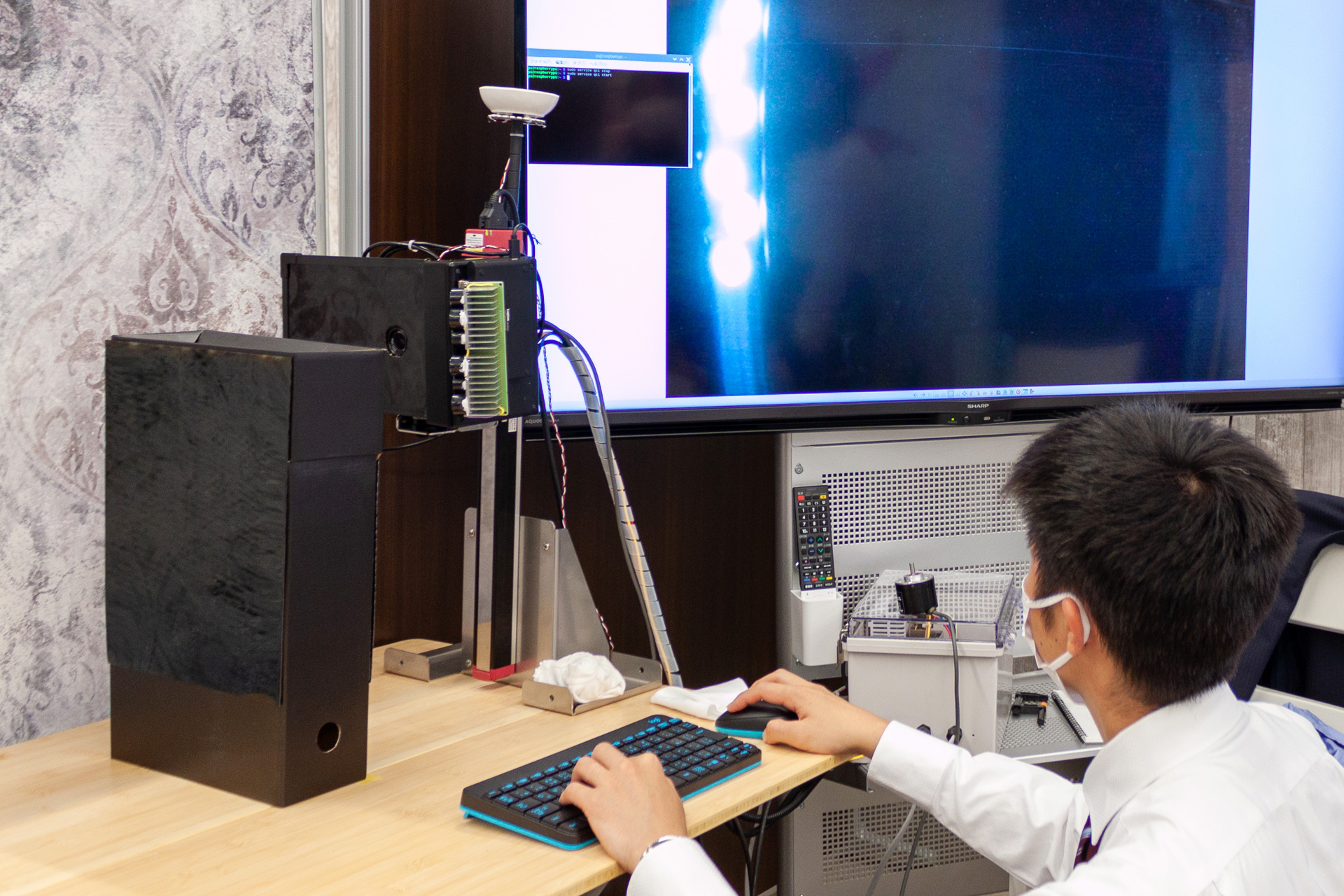
Realization of Transformation by Accompanied Support from Development to Operation and Application.
In the current process of the prototype trial operation, three images in the vertical direction are taken every 10 cm from a 300 m long stainless steel material. The number of shots per lot is as high as 9000 shots. The machine has a function to judge the presence or absence of scratches as well as taking photographs, and lights up yellow when a scratch is detected. With that as a signal, the worker goes to check. There was only one light to signal scratch detection in the first model, but I requested Mr. Kobayashi to change the specification so that the light could be seen in 360 degrees from anywhere. With expert knowledge, parts and methods that meet our request have been found for us at a low cost. It was different from our outsourcing experience because it is possible to proceed with the development while responding to our demands.
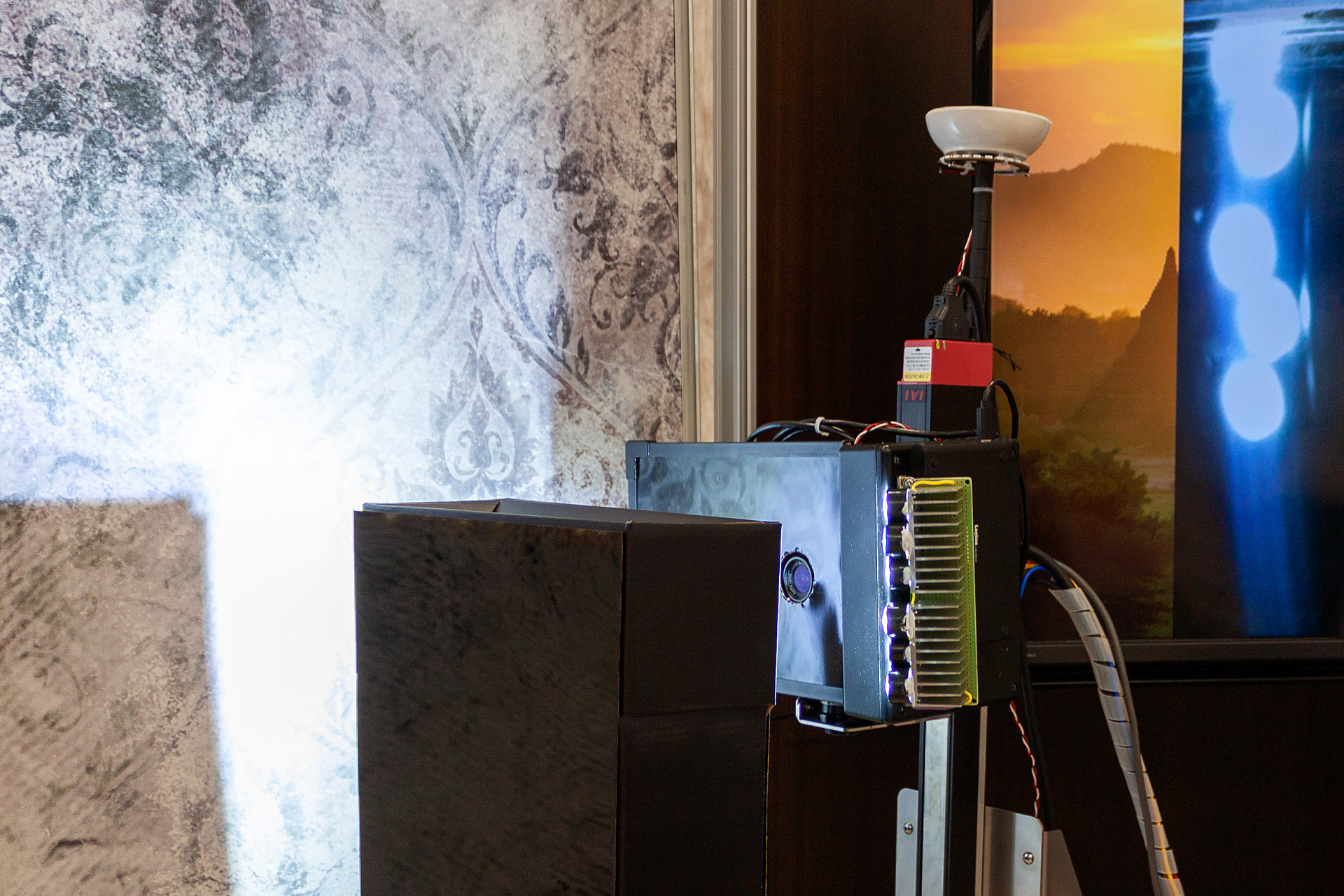
Shallow scratches that the human eye can overlook can be found with this system, and constant monitoring is possible. Because it can be left as an image, it will guarantee the product quality later, and it will also lead to the elimination of the personal work that we were concerned with. Currently, verification is performed by comparing the image with a visual. In the future, we are planning to introduce AI, making it learn the accumulated images and judge not only the presence or absence of scratches but also the type. Automated inspection is not a dream if you analyze the image and set the threshold value.
Turning Zero into One.
The Hurdle is Not High if You Walk with an Expert.
We have only just taken a step forward. There will be walls and cliffs in the future. However, we cannot know if it is good or bad unless we try it. We are proceeding with the development while realizing how much can be done with the latest technology and hardware.
If your company doesn’t have the resources, you can’t start from scratch. With the support of someone with professional insight, we were able to lower the hurdles. When I was recruiting a person that would be in charge of programming within the company, there was an employee who was happy to volunteer, and he seemed to work on it quite happily. For industrial companies, it may also be an opportunity to discover potential IT talents.
To determine if it is something you can eat with a single bite, we recommend that you try it first.
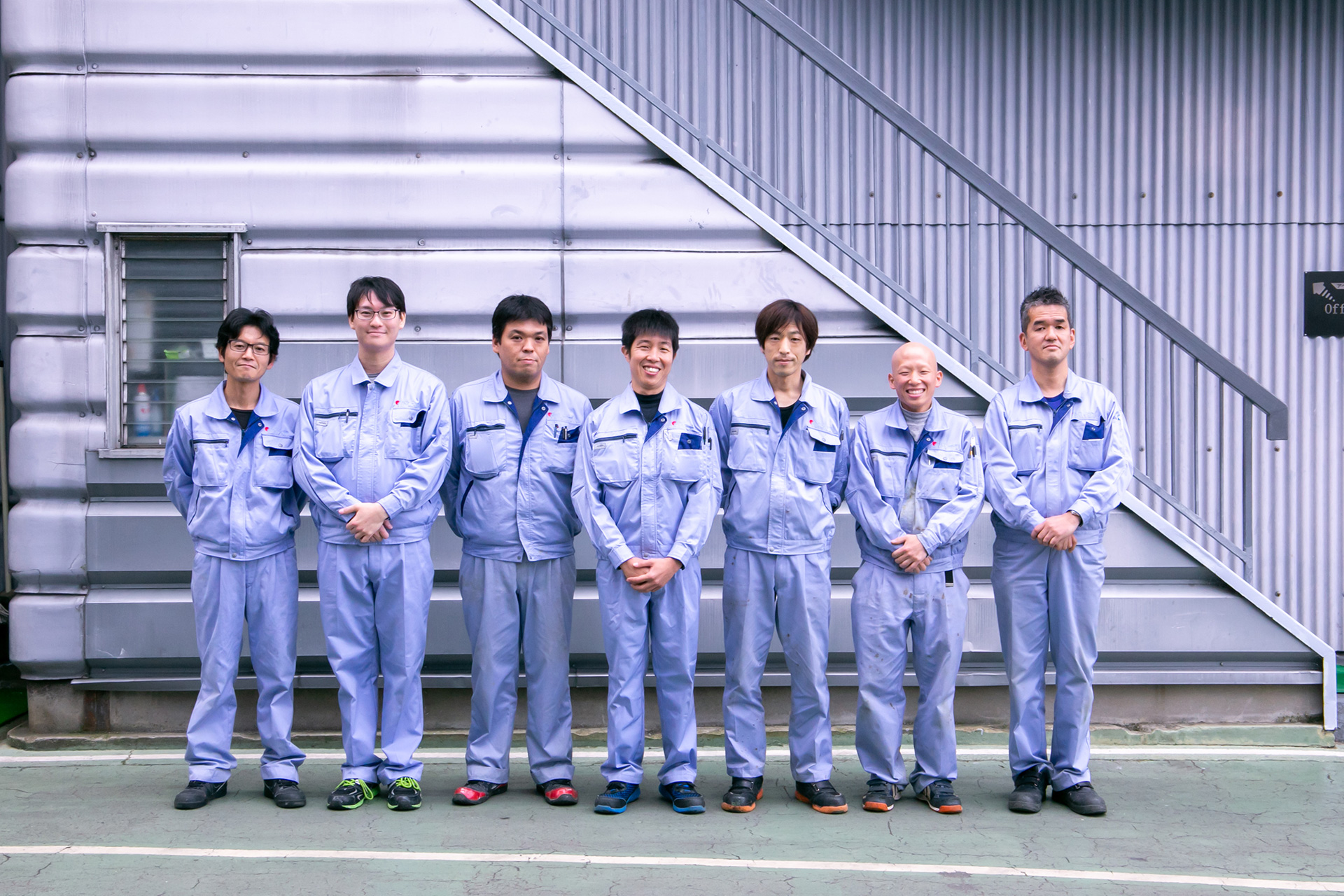
From the Person in Charge of the Project
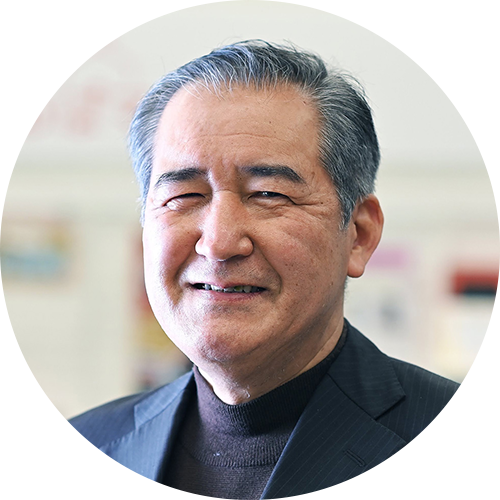
This quality control image system is a mechanism that numerically outputs the features on the surface of the material. The system quantitatively digitizes data and detects the presence or absence of scratches in about 1.5 seconds. It has been programmed, so that duplicate scratches within the photographing range are detected, and alerts are not made repeatedly.
Thresholds for determining which feature is acceptable and what level of scratches are detected can be defined by an in-house representative. The programming language used in this system is Python. It has an extensive library, and with it, the cost of development and learning, as well as the hurdles for in-house production, can be reduced. By making selections such as the use of a 4K camera as well as using Raspberry Pi as the computer, a high-quality system was realized at a reasonable price.
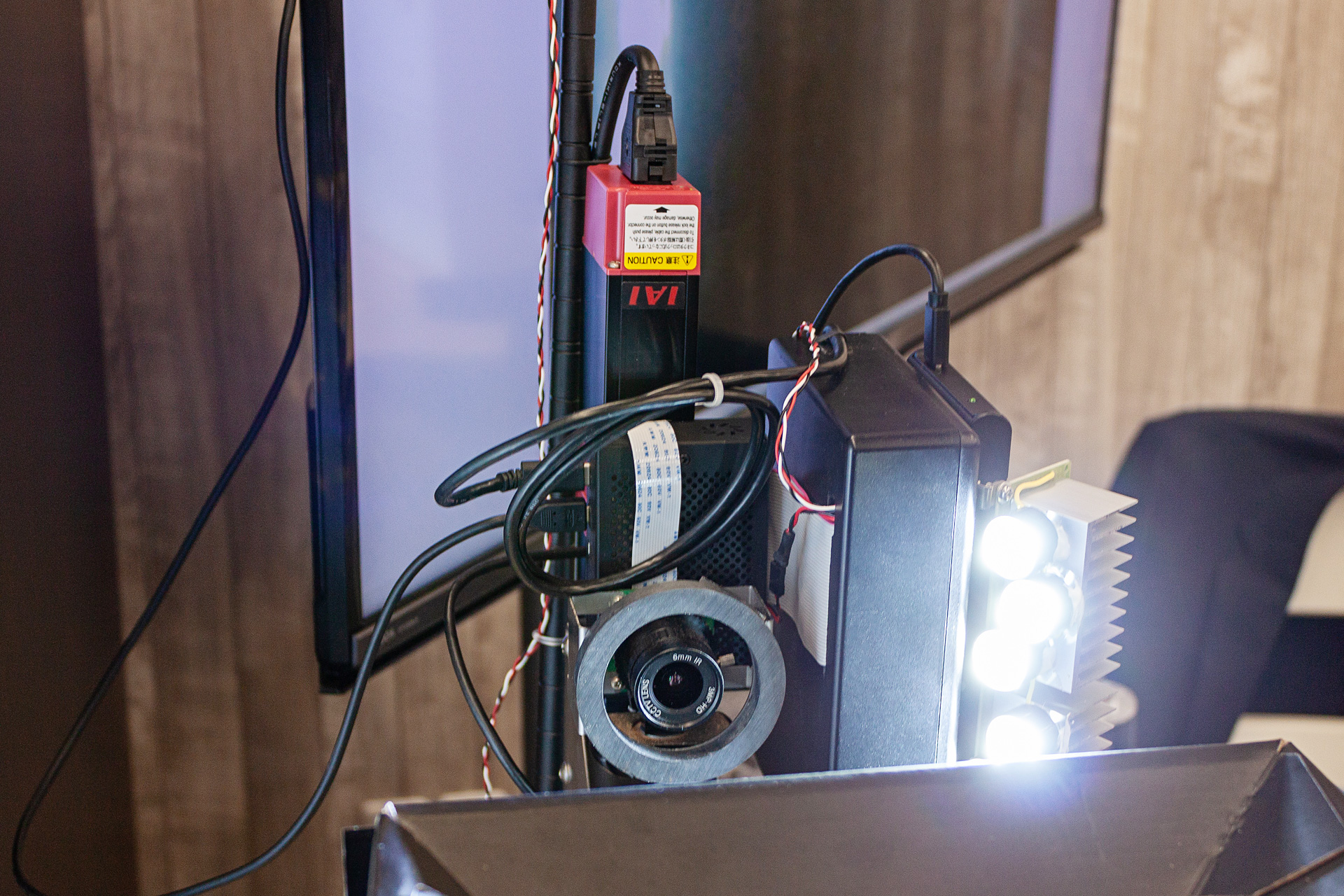
In the future, we are going to introduce machine learning to the accumulated image data and advance to a stage of AI model development to determine the type and condition of scratches. One of the reasons for using Python is that it is easy to seamlessly realize the flow from IoT device development to AI and data analysis.
Japanese manufacturing companies that provide high-quality technology, such as Abel, have the problem of being prone to over-quality. You should not dispose of parts that do not have quality problems. By quantifying, you can build a more appropriate quality control and secured system.
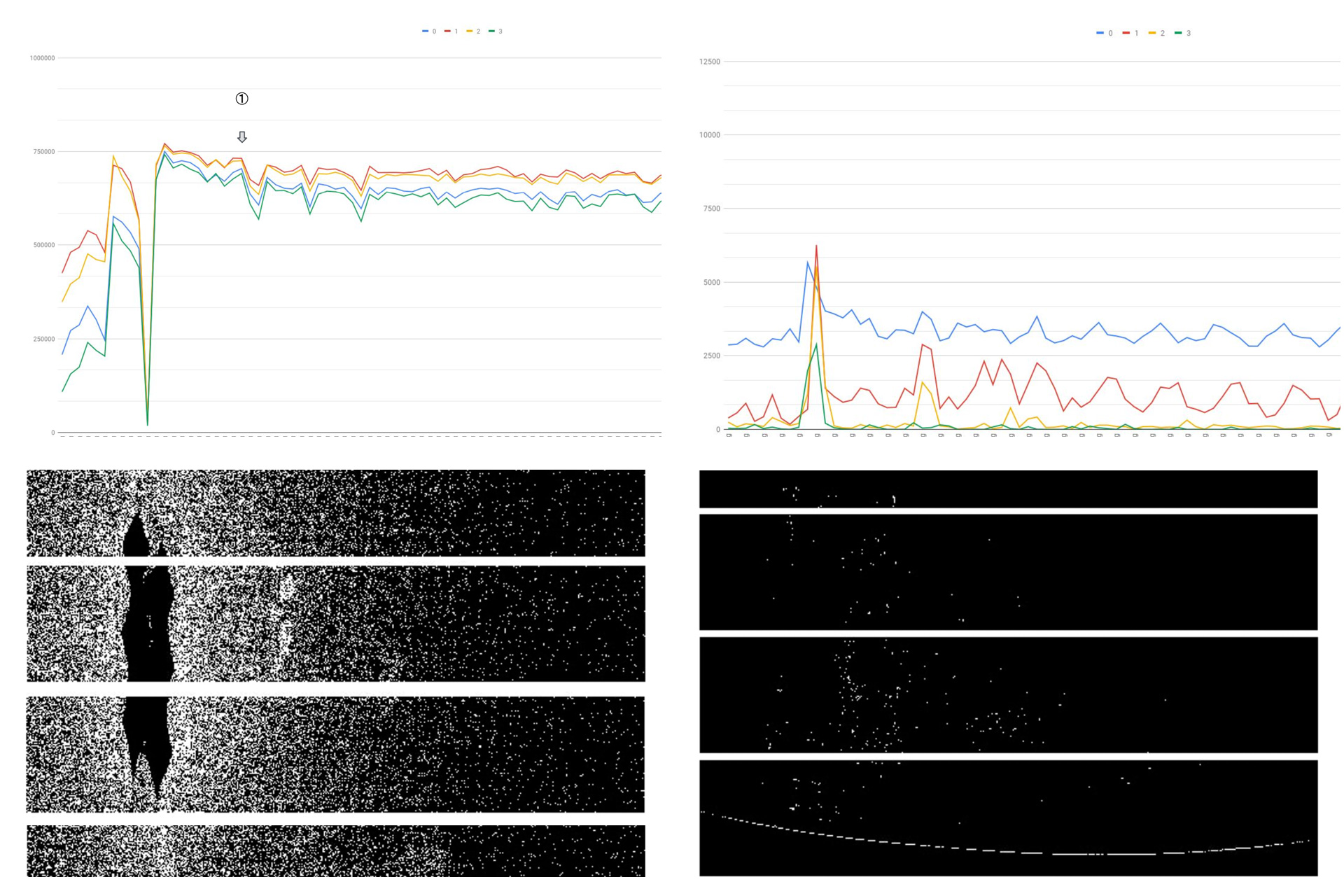
By observing the increase or decrease in the number of bright spots, the occurrence and disappearance of scratches can be quantified.
The IoT requires extensive knowledge and skills to achieve it. There is mechanical design, hardware design, software design, cloud construction, application development, and so on, with each requiring specialized knowledge and skills. I think disruptive innovation should be accepted by SMEs, but there are several barriers to SMEs’ own internal transformation. In addition, it is difficult to provide a system whose price and specifications match the actual situation of SMEs because a business model undertakes system development and operation and provides them unilaterally, and thus small turns cannot be made.
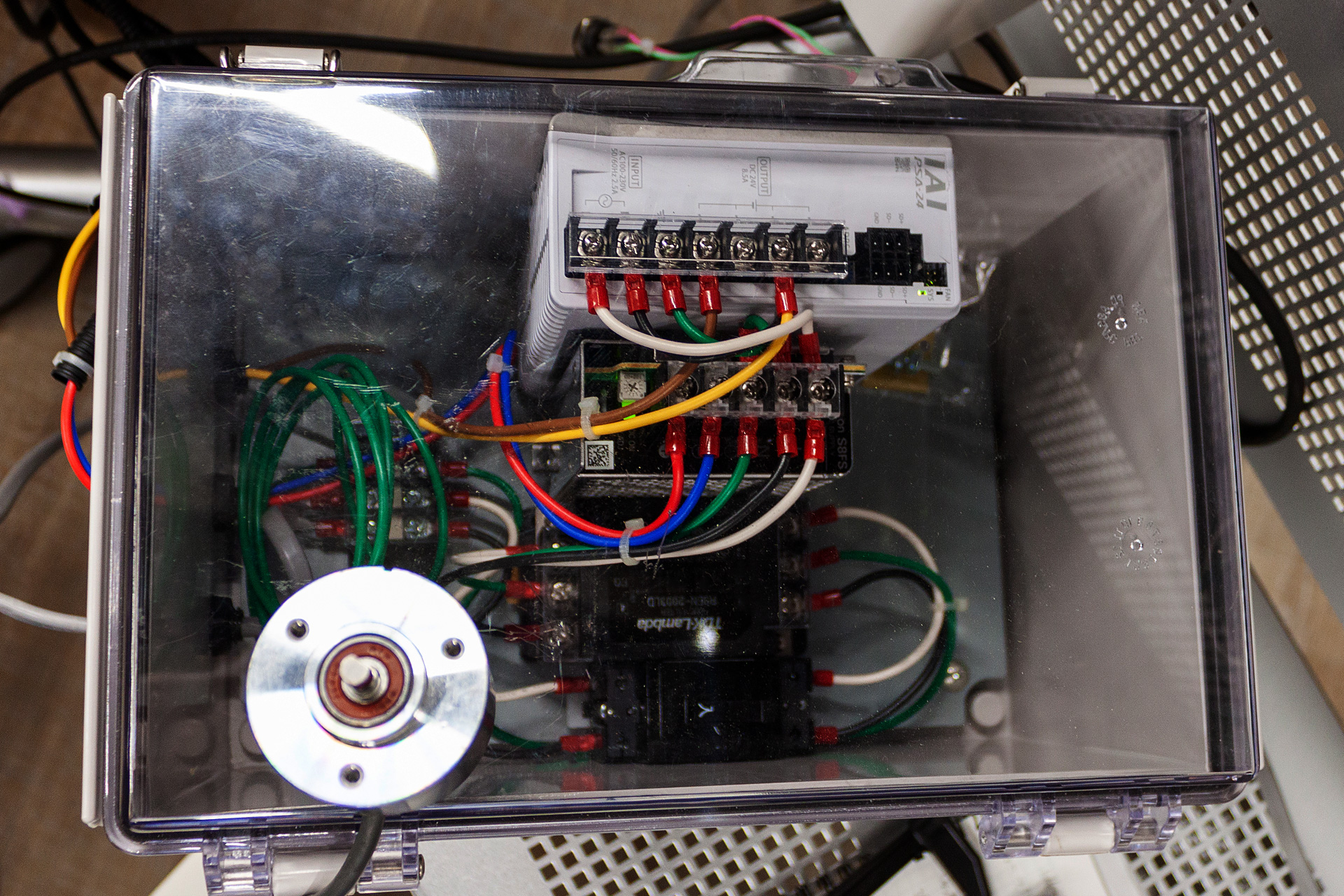
We at eftax are making all design and development open as we provide technical guidance so that SMEs can manufacture in-house. This can be realized only when there is a relationship of trust. This time, it was made possible because Abel decided to open the backbone of their company to me, and I had the opportunity to see the site with my own eyes.
In addition, there is a network of manufacturing companies called “Miserubayao” in Yao City, and that we were able to get cooperation from them is a point that we cannot omit. Regular community-based efforts and exchanges have become a good example of creating innovation.
In the future, while repeating the process of development and verification, I would like to work together with Abel towards transformation.
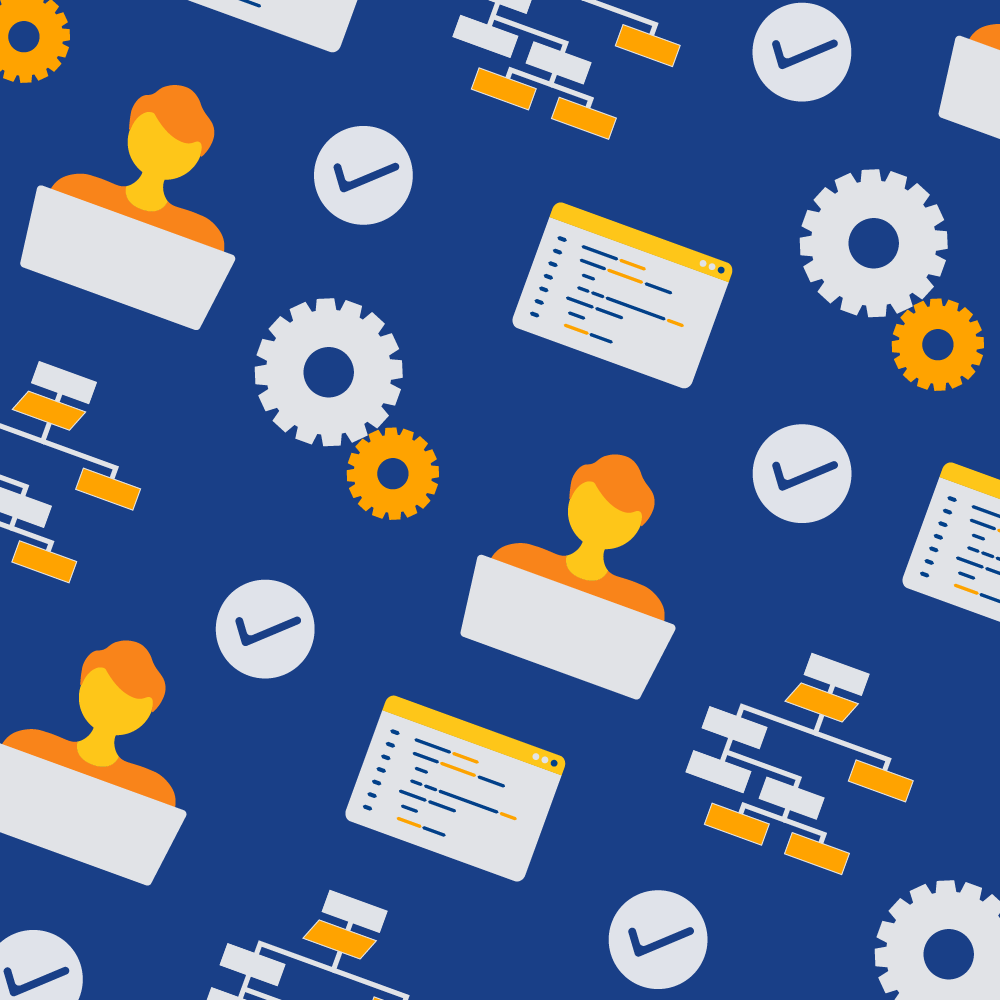
Construction and Operation Support of LMS (Learning Management System) at Kobe University
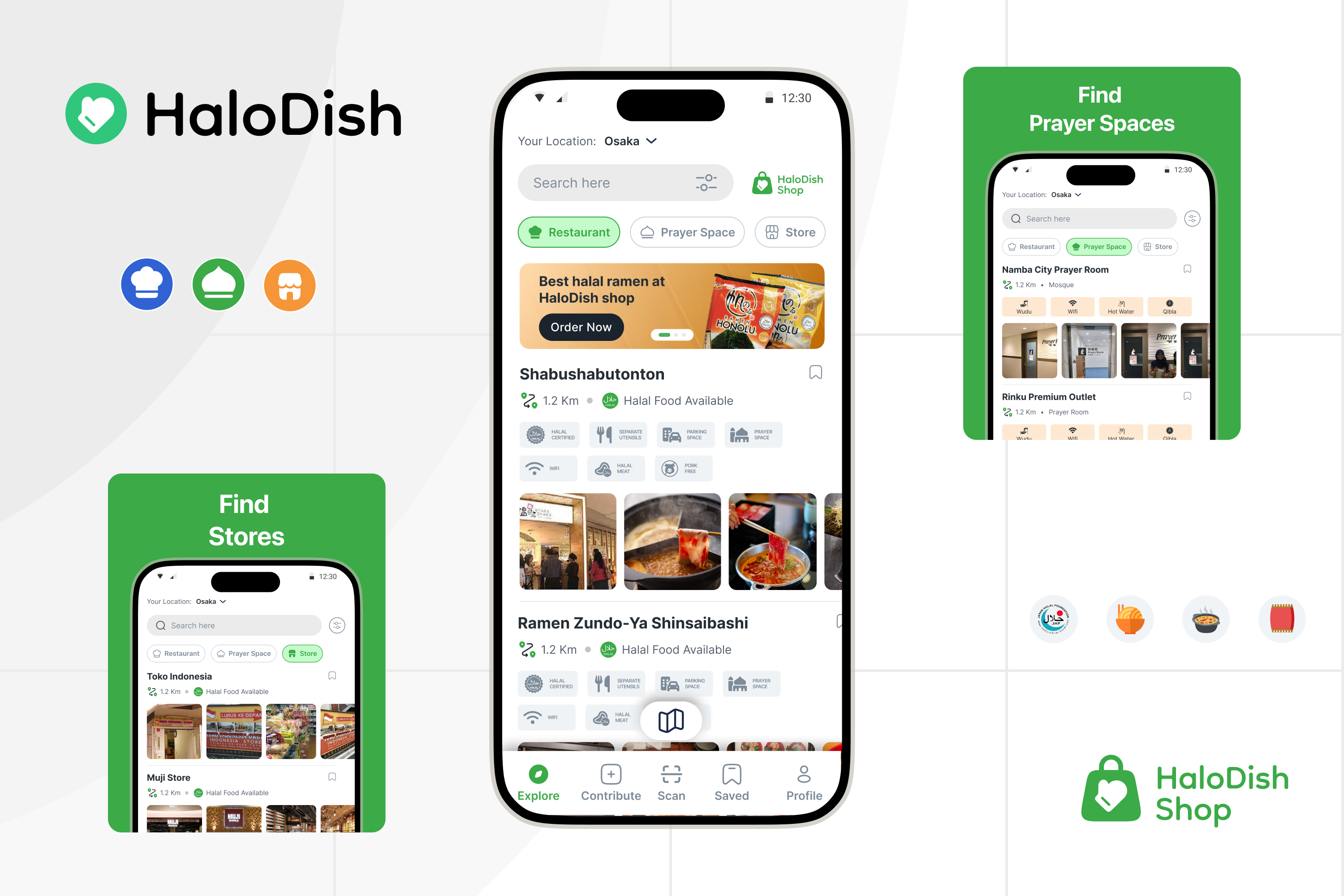
Cross-border app development: a roundtable discussion about collaboration, planning and development of halal locator app, HaloDish
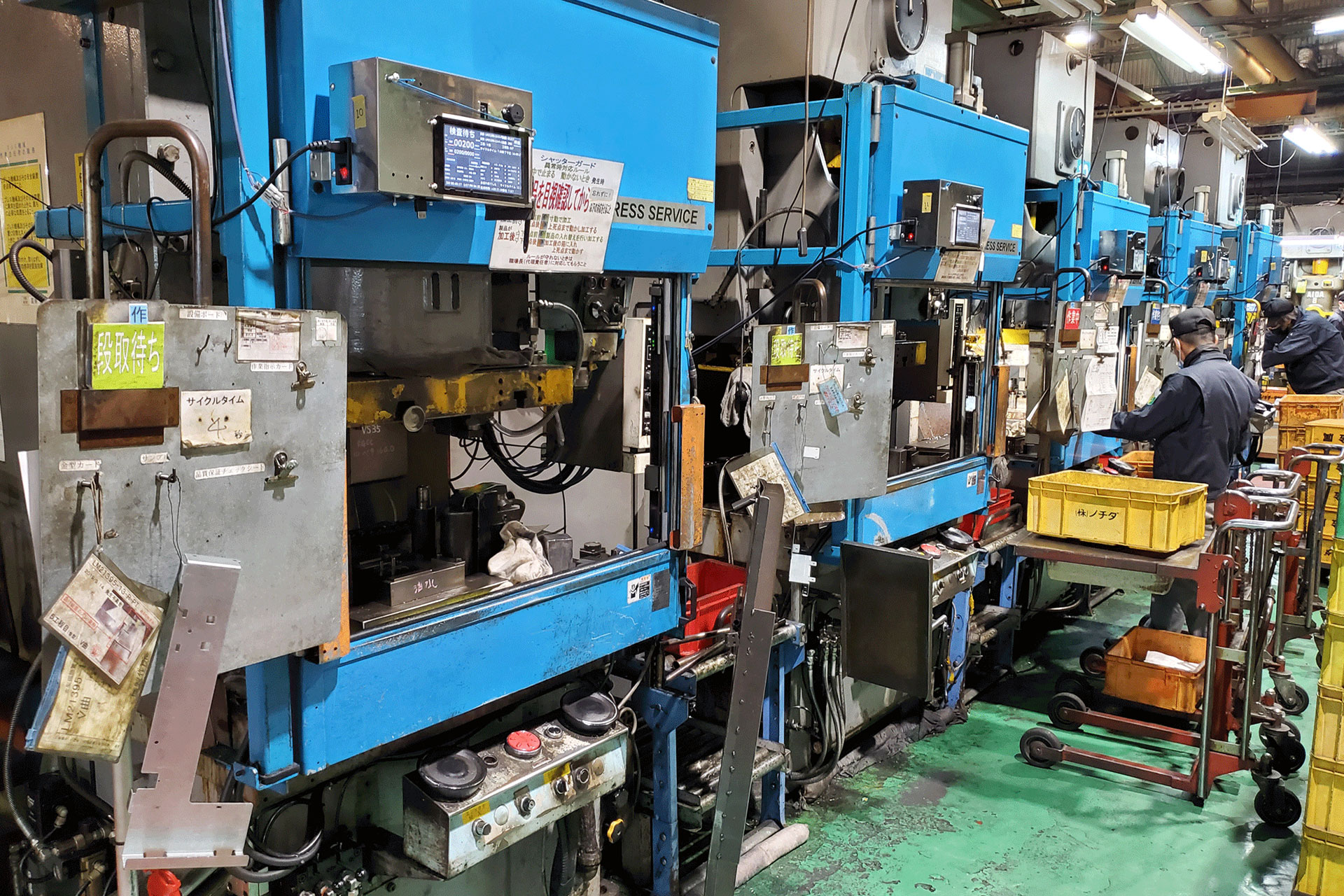