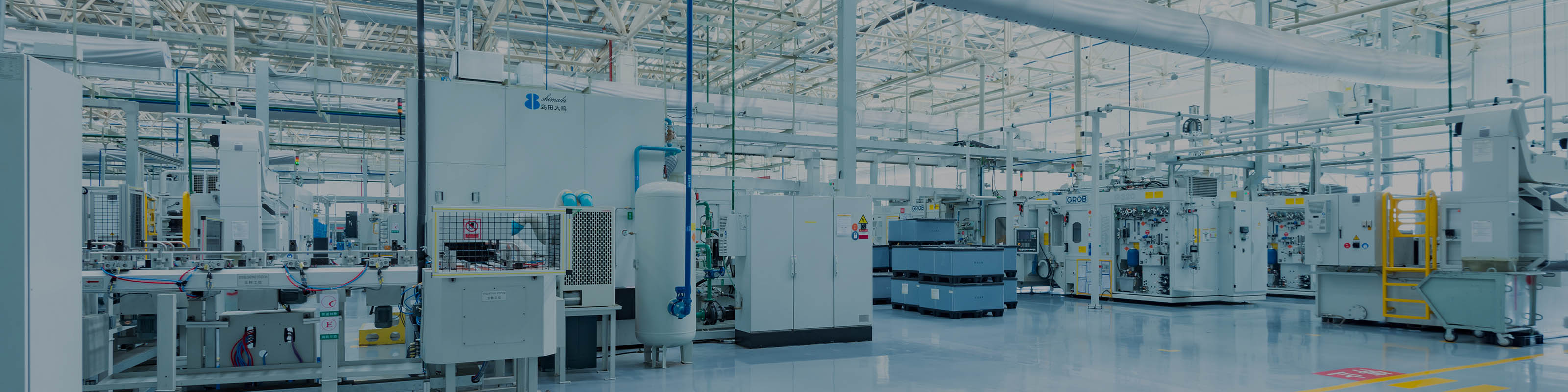
Product Management Case Study Utilizing IoT Technology at Nochida Co., Ltd.
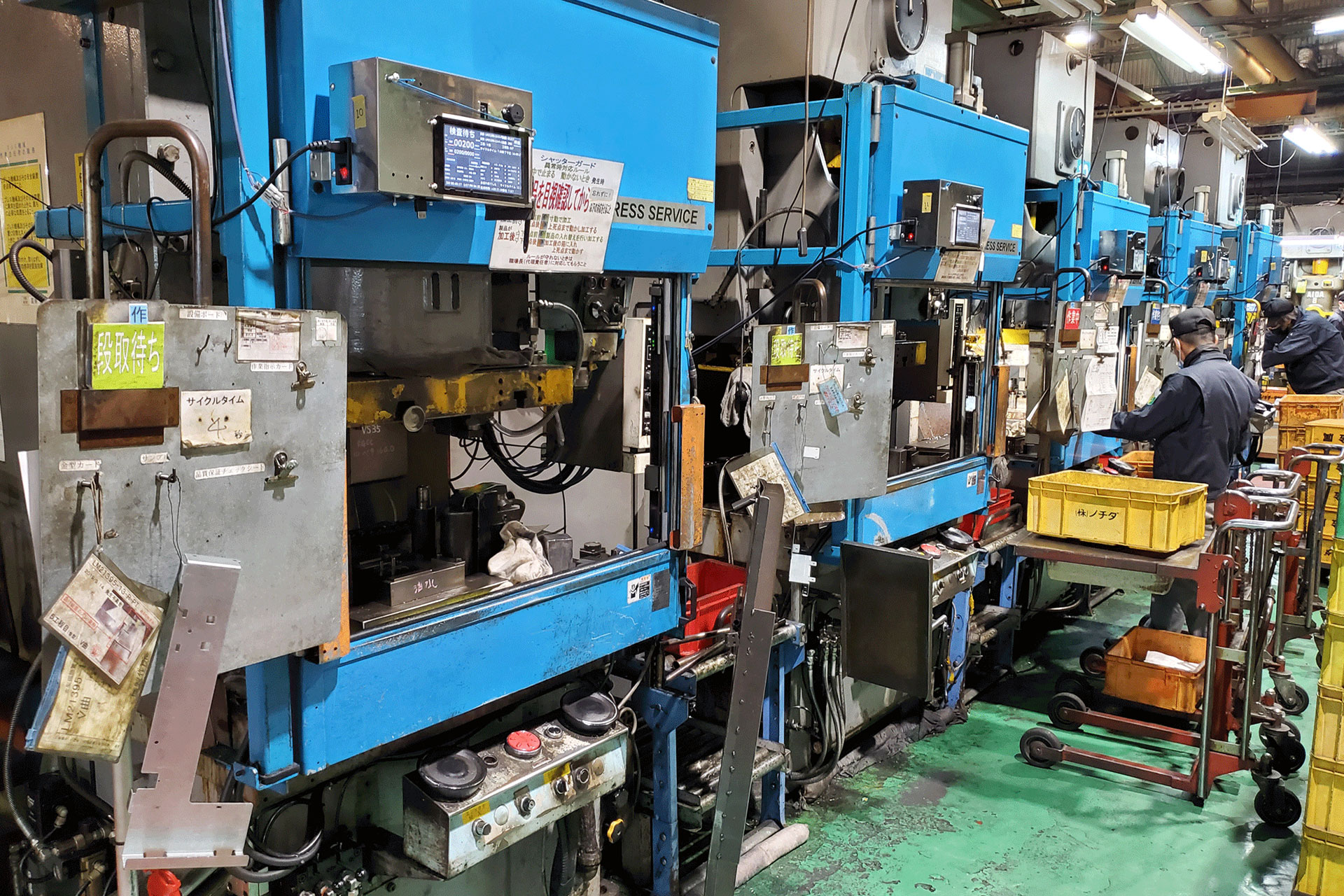
Production Management System Utilizing IoT Technology
Purpose of Introducing IoT System
Factory production control using RaspberryPi
Our Areas of Responsibility
- System planning and design
- Development of IoT devices
The Voice of Nochida Co., Ltd.
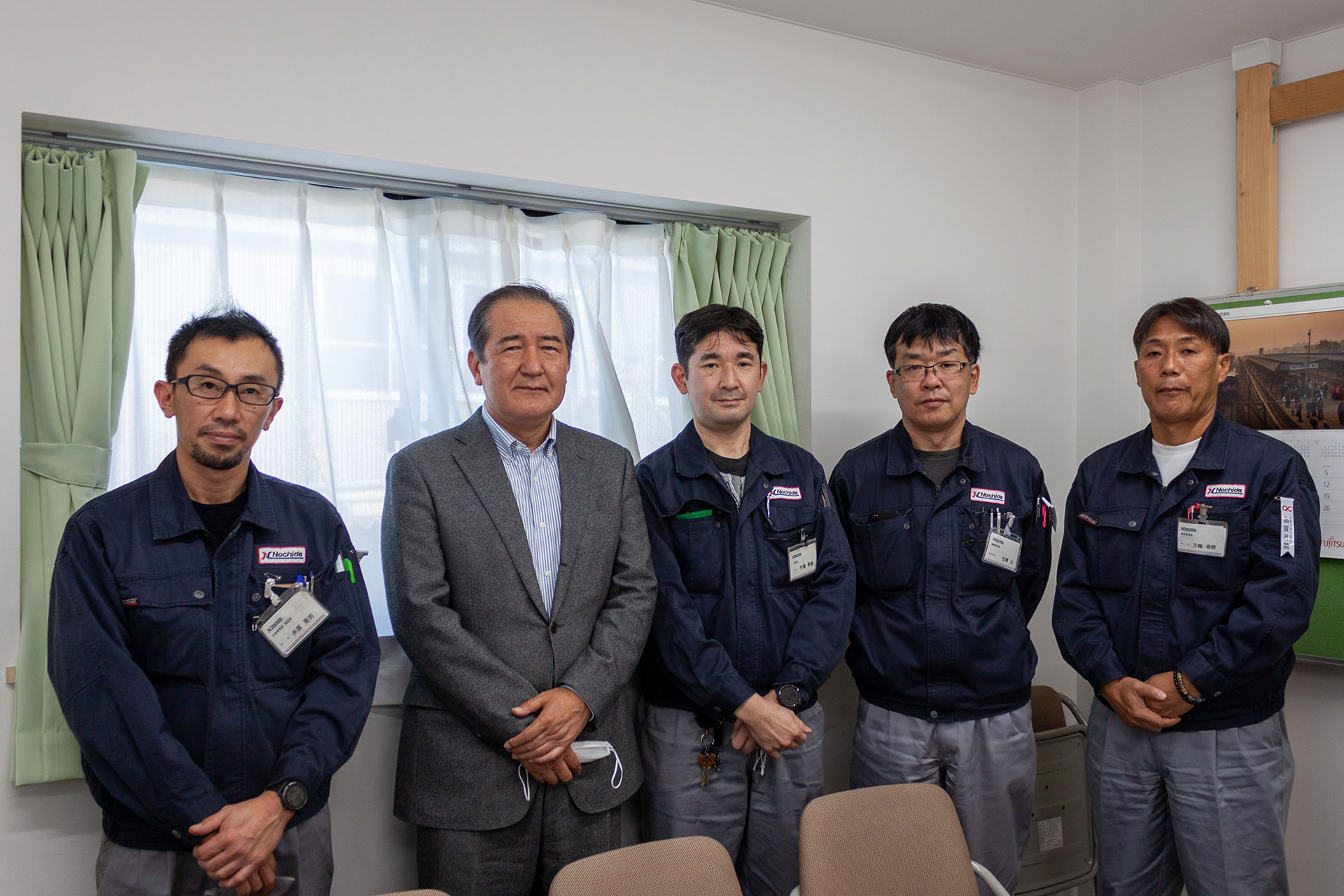
Nochida Co., Ltd. manufactures metal parts used in vehicles and medical equipment. For more than half a century since its establishment, the company has been engaged in the processing of various metals on the strength of “ultra high-mix, variable-volume production”, and is highly evaluated and trusted by many companies.
eftax recently supported the development and implementation of a production management system using IoT technology at Nochida’s Osaka Division. We interviewed Mr. Takehashi who belongs to the Development Office and is in charge of the Nochida side of this project, Director and General Manager Mr. Miwa, the Business Administration Department Mr. Furusawa, and the Manufacturing Department Mr. Ihara.
Real-time Management of the Status of Ultra-mix, Variable-volume Production, and a Common Language
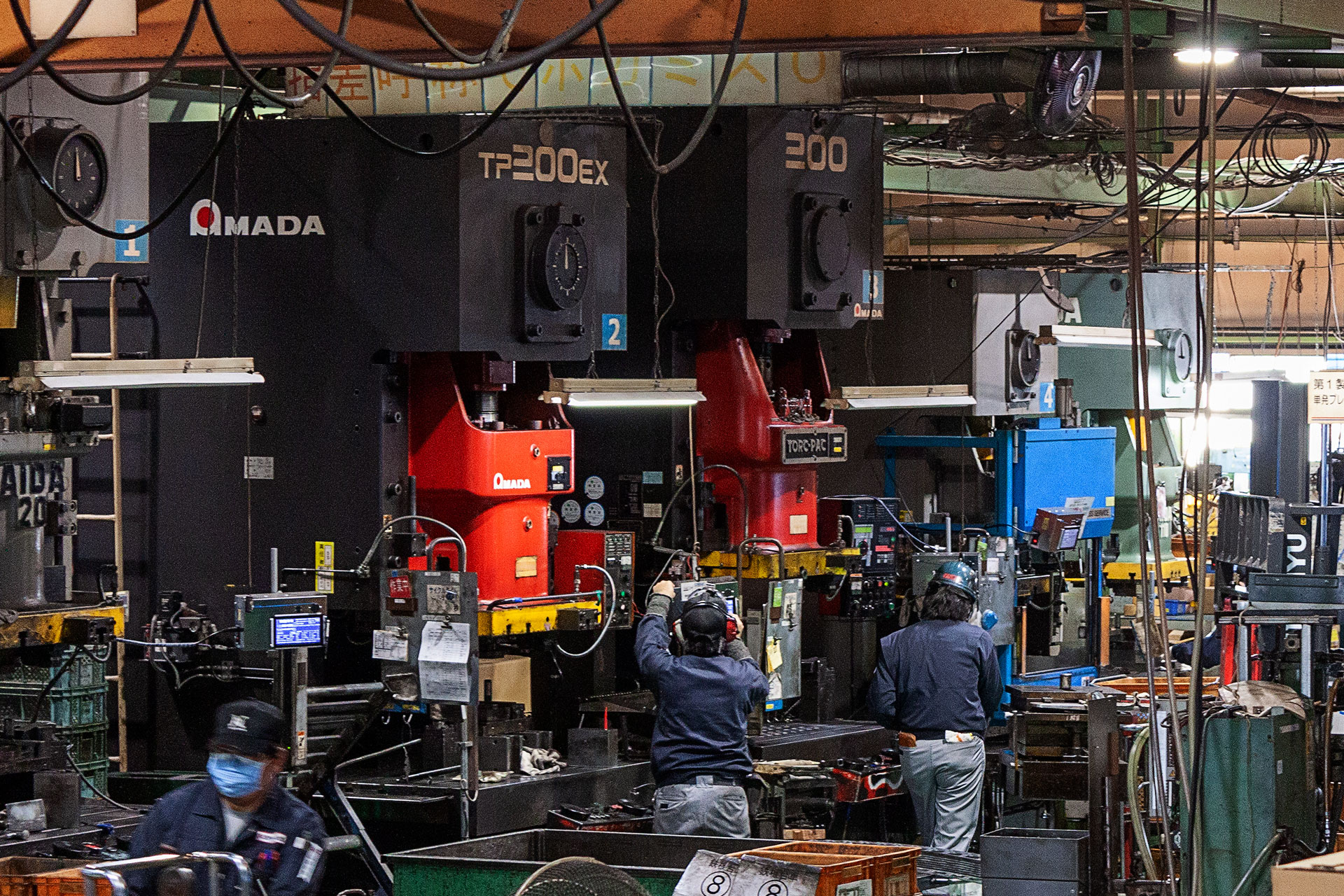
Nochida Co., Ltd. is a metalworking company that handles steel, aluminum, stainless steel, and other metals. Nochida manufactures metal parts for a wide range of industries, including transportation equipment such as motorcycles, industrial transport equipment such as construction machinery and forklifts, housing equipment such as elevators and air conditioning ducts, and medical and barber/beauty equipment.
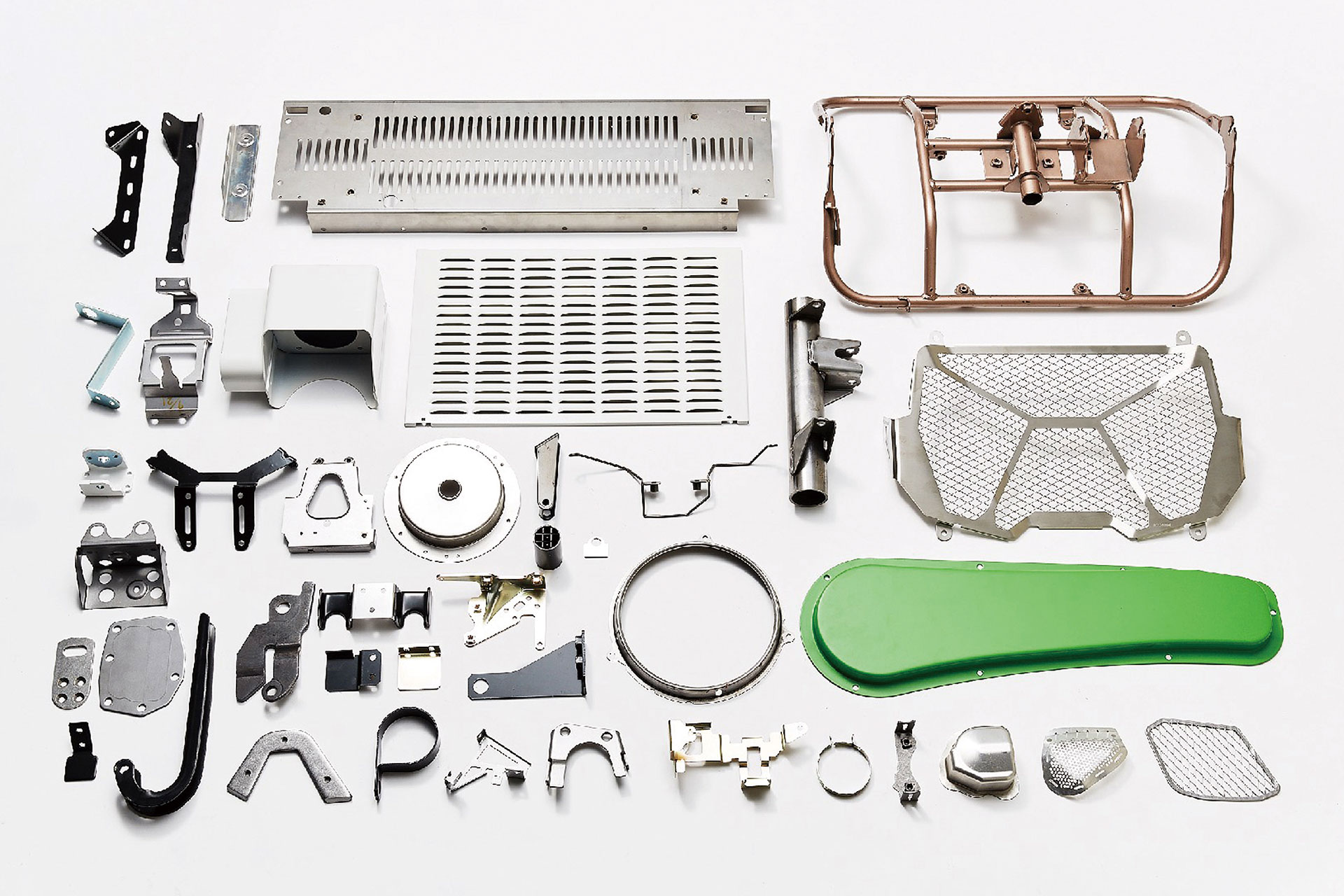
With its strength and track record in “ultra-high-mix, variable-volume production” since its founding in 1967, NOCHIDA has earned the trust of major manufacturers, and its knowledge and technical capabilities also provide development support for companies and organizations, including the design and manufacture of electronic shields for radiation cancer treatment machines and equipment for use in activity of daily living (ADL) training circuits.
“Ask Nochida and they always figure it out. ……”. Nochida says that it aims to be a company that customers feel that way about, and is capable of handling orders for a wide variety of products, even from a single piece. Thay have the facilities and systems in place to meet the diverse needs of its customers to the greatest extent possible, and currently manage more than 50,000 parts.
The key word for the launch of this project was also “ultra-high-mix, variable-volume production,” which is one of Nochida’s strengths.
“If there are only a few dozen or a hundred items to be handled, it may be OK to manage them by writing them down in a notebook or somehow. However, when it comes to tens of thousands of items, computerized management is necessary. Until now, we have managed them with a system we developed in-house. One day, the president asked me if we could use RaspberryPi for production management at the factory. We could use computers to manage the factory’s production status and exchange information in the cloud as a common language. We didn’t have that kind of technology.”
Mr. Takehashi, who led this project as the person in charge of Nochida’s side, explains how the project started.
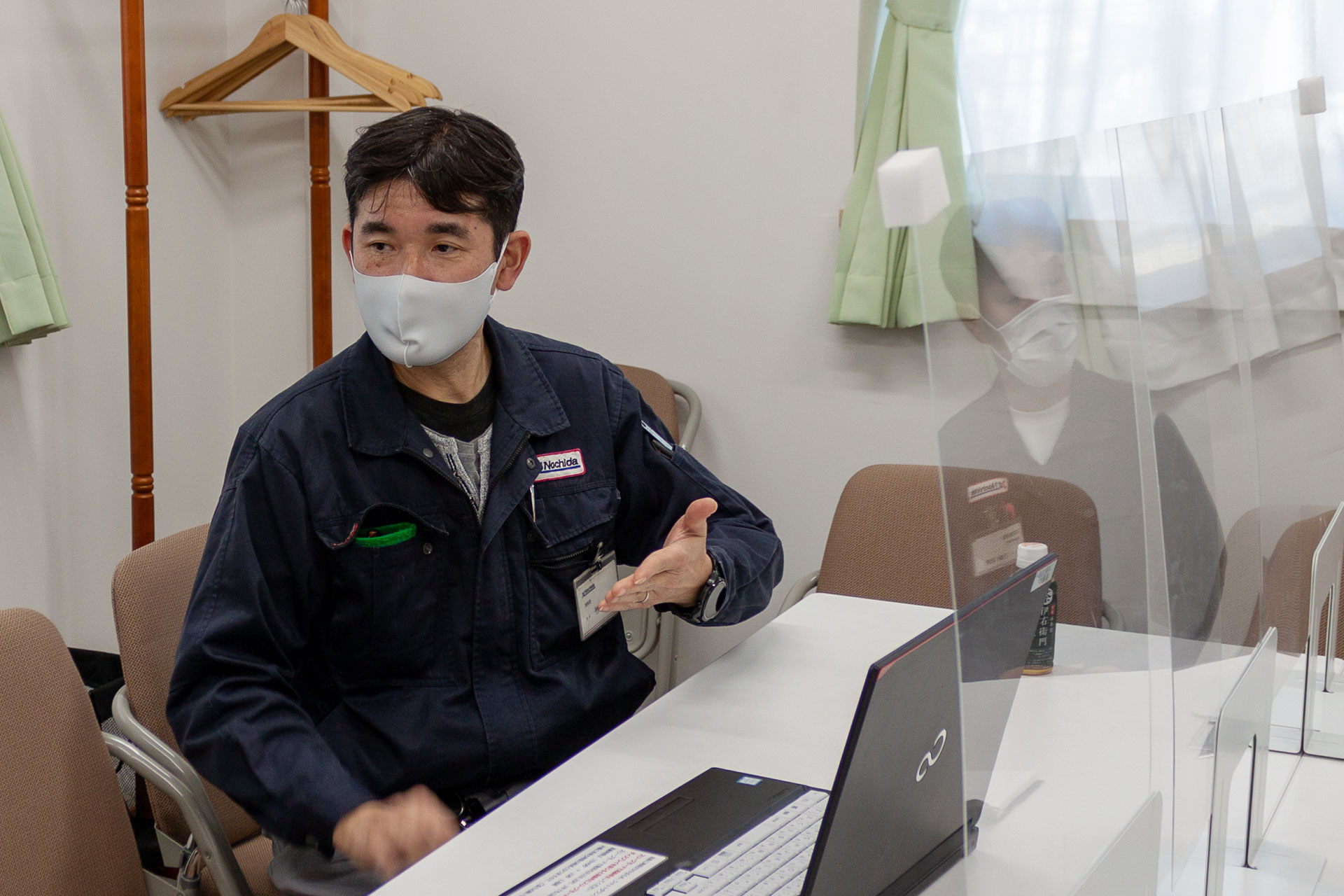
Nochida has two factories equipped to produce a variety of products in variable quantities, one in Yao City, Osaka Prefecture, and the other in Yasu City, Shiga Prefecture. This time, IoT devices were installed in the Osaka Division, where press work, spot welding, and robot welding are performed.
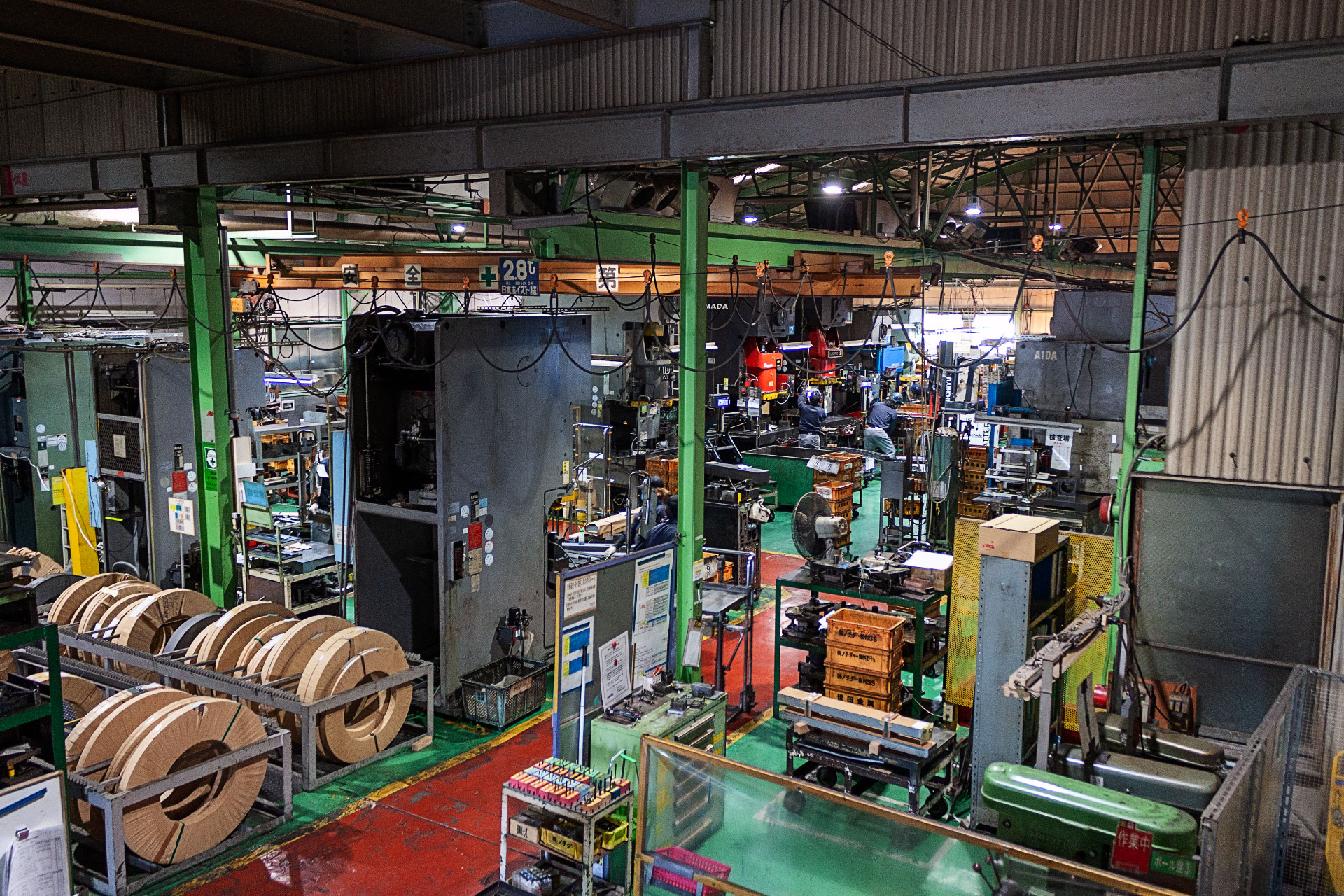
Mr. Furusawa, who is in charge of the company’s core system, explains the background behind the decision to introduce RaspberryPi as follows.
“We use Microsoft Access to manage our internal systems. Each product is manufactured in a different way, so even within the same system, there are functions that are used by different divisions and functions that are not used by different divisions. For example, the system used by the Shiga Division is a system that calls up drawing data from the server when the barcode on the instruction sheet is read, and it can be viewed. However, it does not use RaspberryPi, Windows.
In the past, it was very difficult to link a PC with equipment. The work to connect the communication cable and the program itself were very complicated. But with the introduction of the small computer called Raspi, it became easier to link them together. And in terms of operating systems, we can now use something very similar to Windows. However, we didn’t have this technology, so we started this project with the idea of asking eftax for a little help and seeing what we could do with it.”
Computerized Control of Work Procedures
Reduces Human Workload and Improves Quality
To build a production management system using RaspberryPi, the first thing we looked at was process management for press work.
Takehashi explains the process of introducing RaspberryPi: “I had a meeting with Ihara from the Production Department and asked him if we could use a computer to do what we were currently doing manually.”
The Osaka Division manages production progress by moving instructions on the status control board. Prior to the introduction of IoT devices, the start and end times of work were written by hand on a form by the worker, which was then input into a computer by another person in charge.
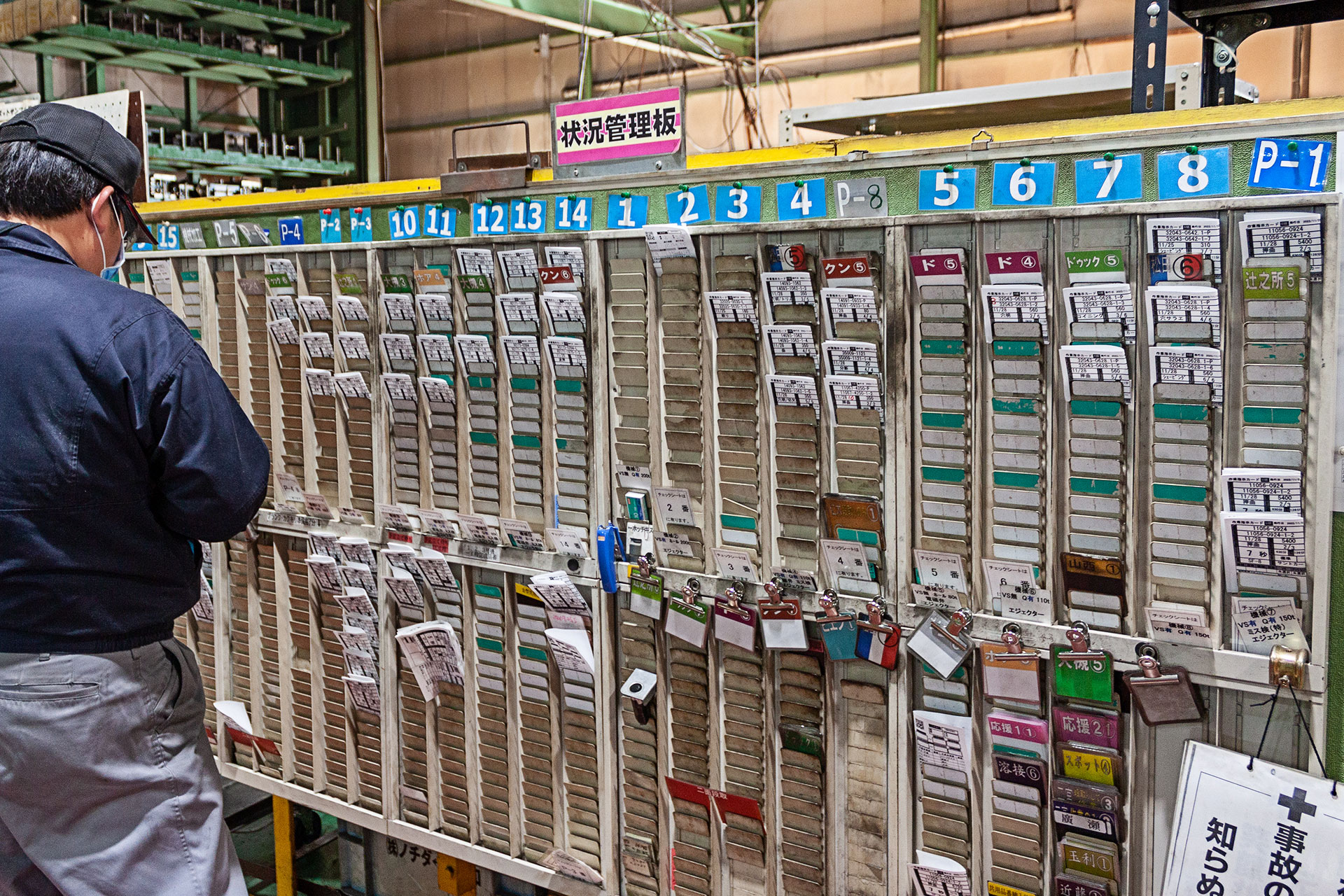
“Our first thought was that we could skip the process of retyping what was written on paper into the computer. Also, we did not know how much time the person would spend processing the product until the input process was complete. Now with the IoT system in place, this can be tracked in real time. We don’t need to input the data into a computer any more, but the data automatically collected along with the processing work lives on as raw data.
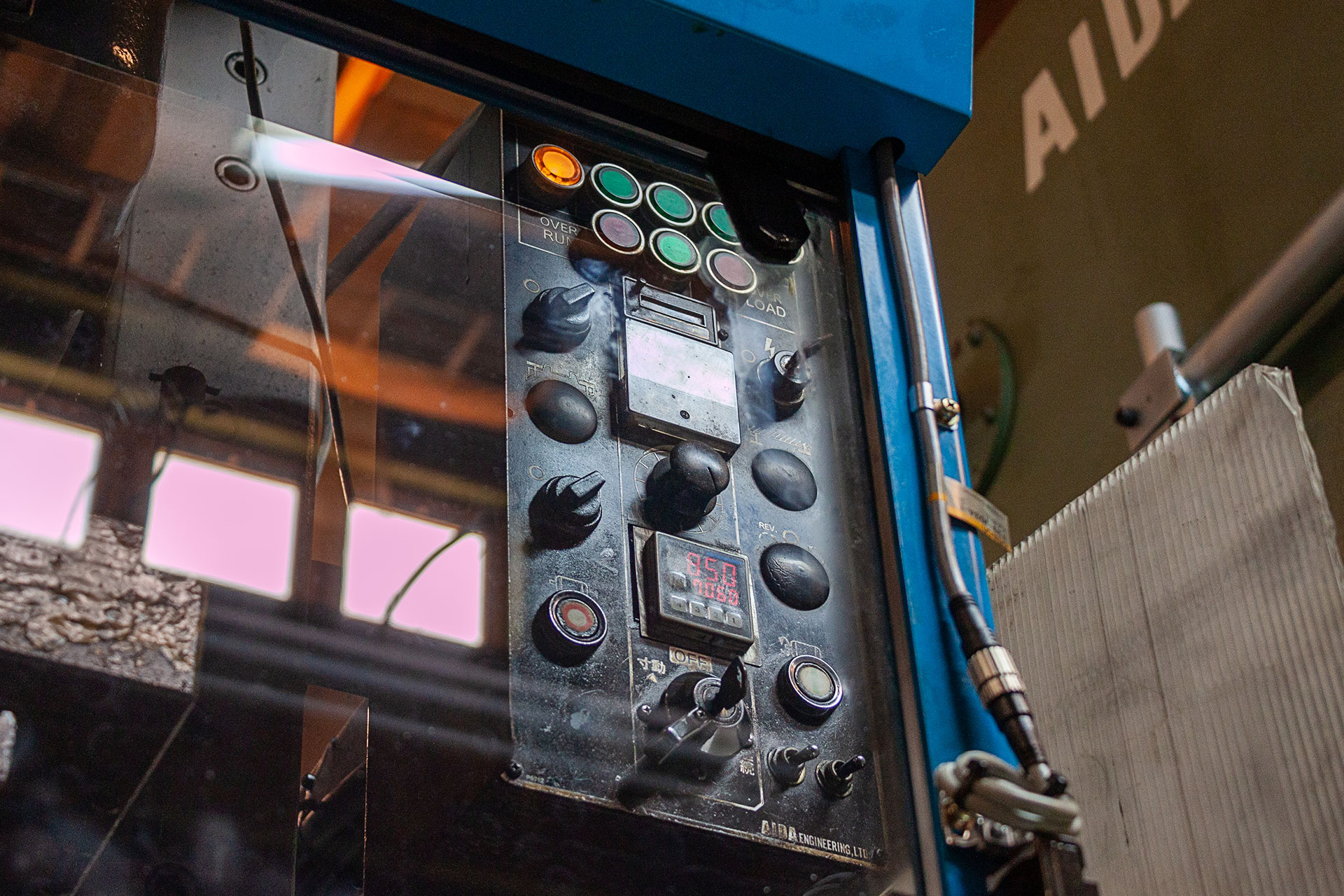
We can also see individual differences and changes in speed with work proficiency. We can use the data to see if a person is a fast and accurate doer. It will also help us to understand the problems of what is taking time, and lead to the formulation of measures for improvement.”
The development and implementation of this touch-panel operated IoT device to manage the press process took about a year and a half.
“We exchanged quite a lot of communication, haven’t we?”, Mr. Takehashi and Mr. Ihara look at each other and laugh.
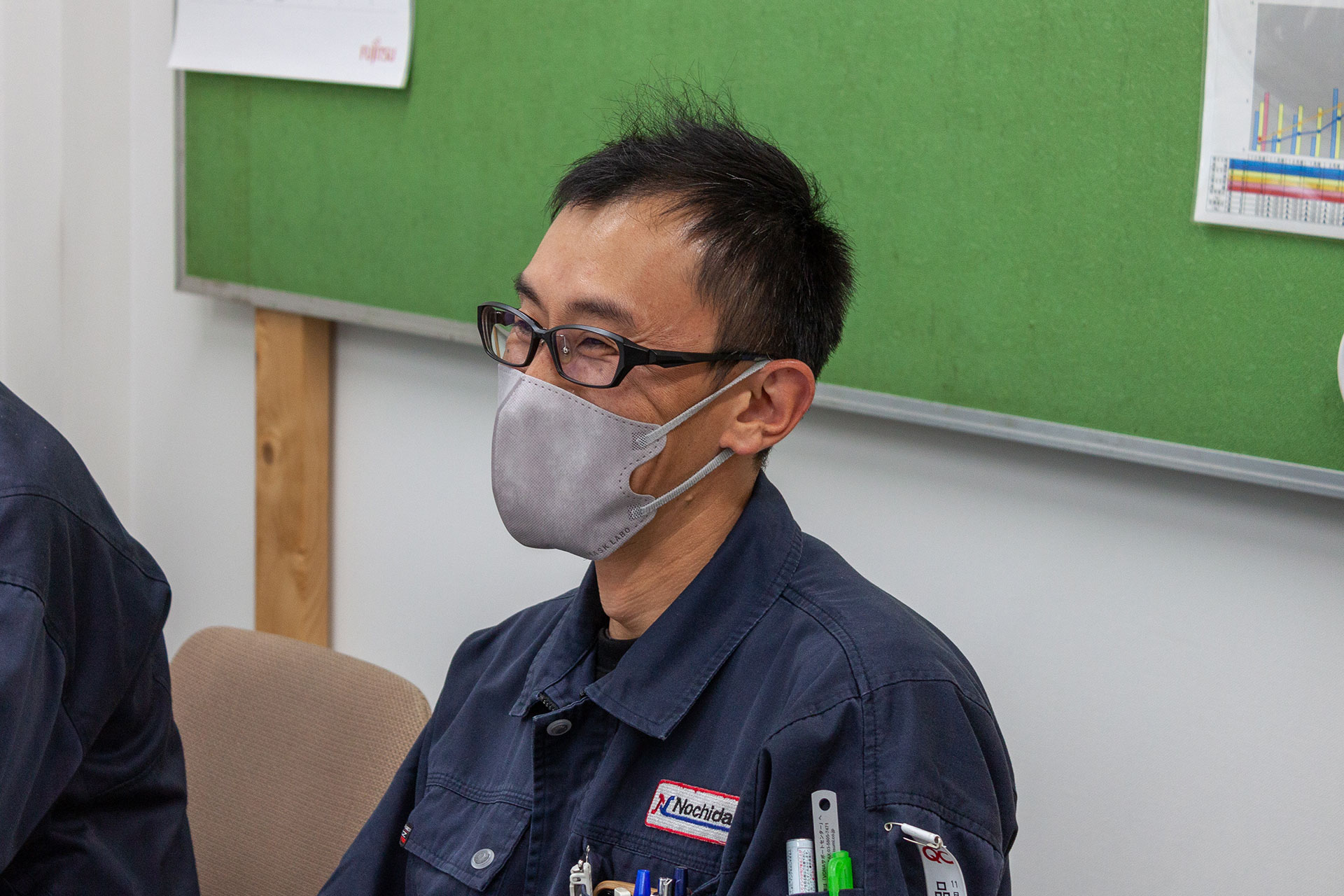
“What should the first screen look like? Like this? In such a way, we discussed a lot. We asked people who were involved in manufacturing, and then we discussed with Mr. Kobayashi whether it would be possible to do something like this.
We imagined, “This kind of screen would be easy to use,” “For example, this kind of system would be possible,” “If we could take such and such records, it would be a useful tool for the company. We went ahead with the project, imagining “This kind of screen would be easy to use,” “For example, this kind of system would be possible,” and “If we could record something like that, it would be a useful tool for the company.”
This process also led to the formatting of the know-how that had been in place as SOP (Standard Operating Procedures).
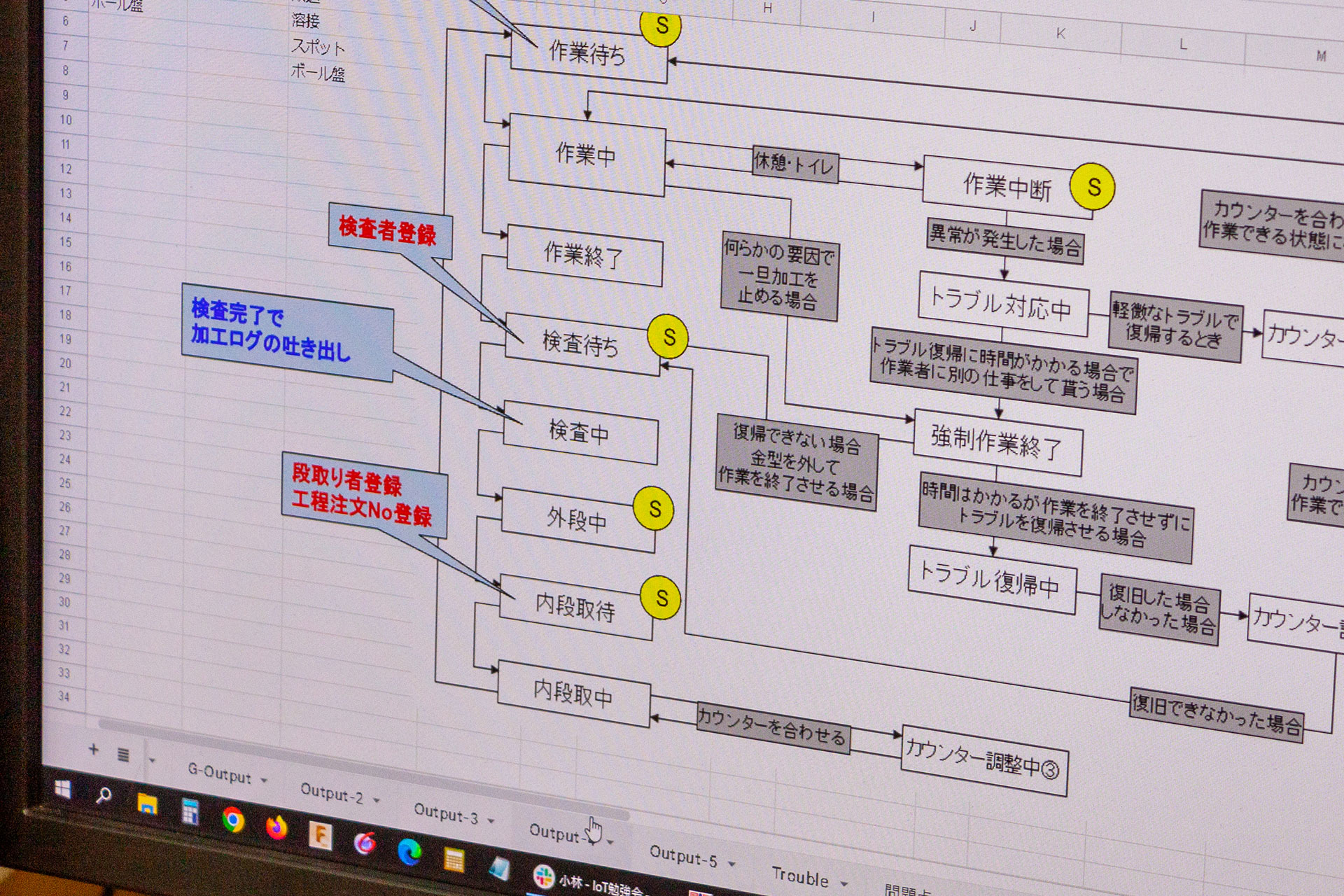
“It took quite a bit of time to organize the standard operating procedures while coordinating with the various departments, but it also took quite a bit of time to actually build the hardware and place it. Well, perhaps the most time-consuming was the placement.”
This is because, based on the planning, development, and design of this IoT device, it was Mr. Takehashi who assembled and set up the actual device.
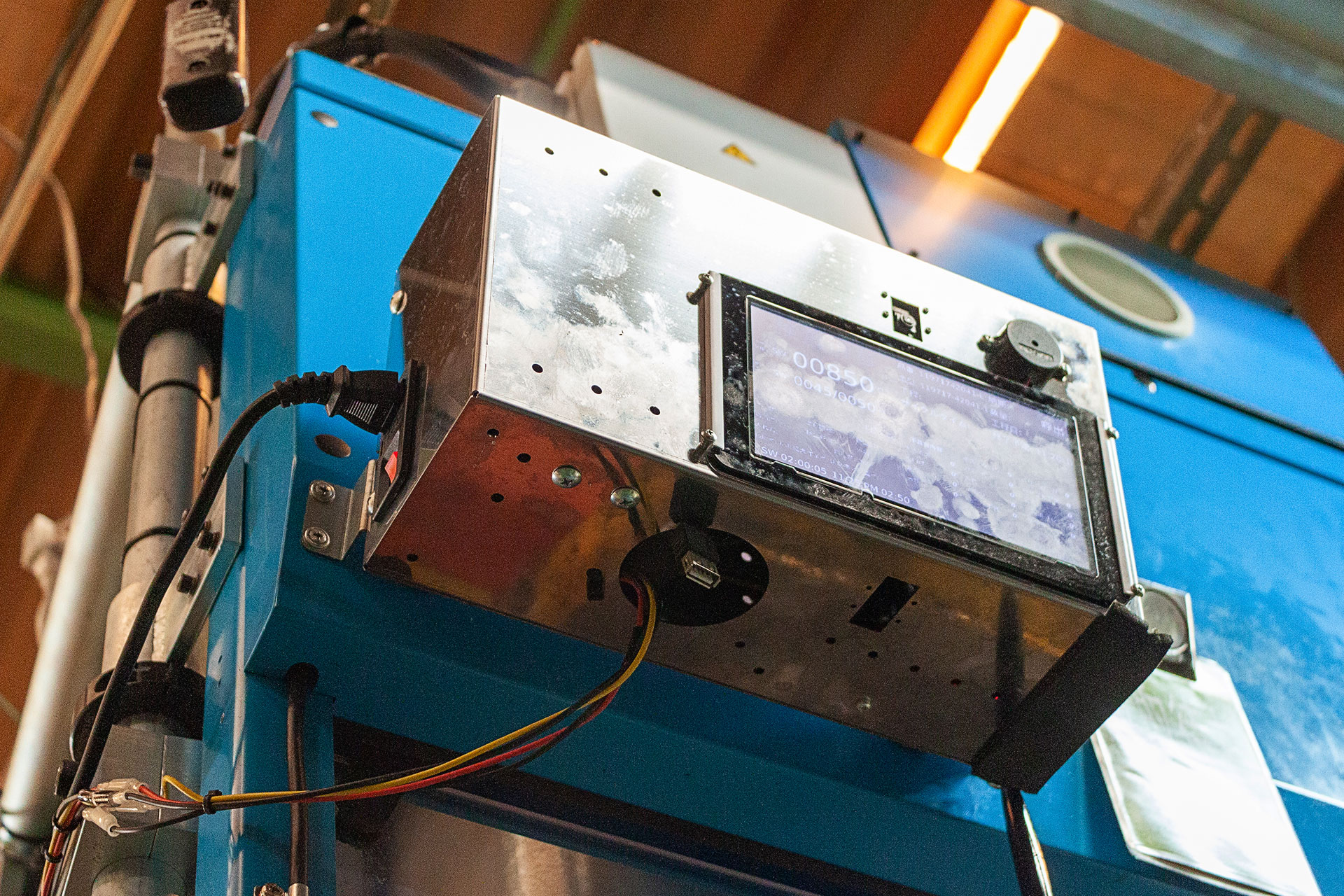
“I made the boxes and installed a total of 25 units. I couldn’t work that on weekdays when the factory was in operation, so I had to do the wiring on days off……” Mr. Takehashi looks back on the hard work.

Mr. Takehashi is actually the creator of Nochida Co., Ltd’s own B-to-C products. A laboratory has been set up in a corner of the Osaka Division, where research and development is conducted on a daily basis. It is in this lab that these IoT devices also took shape.
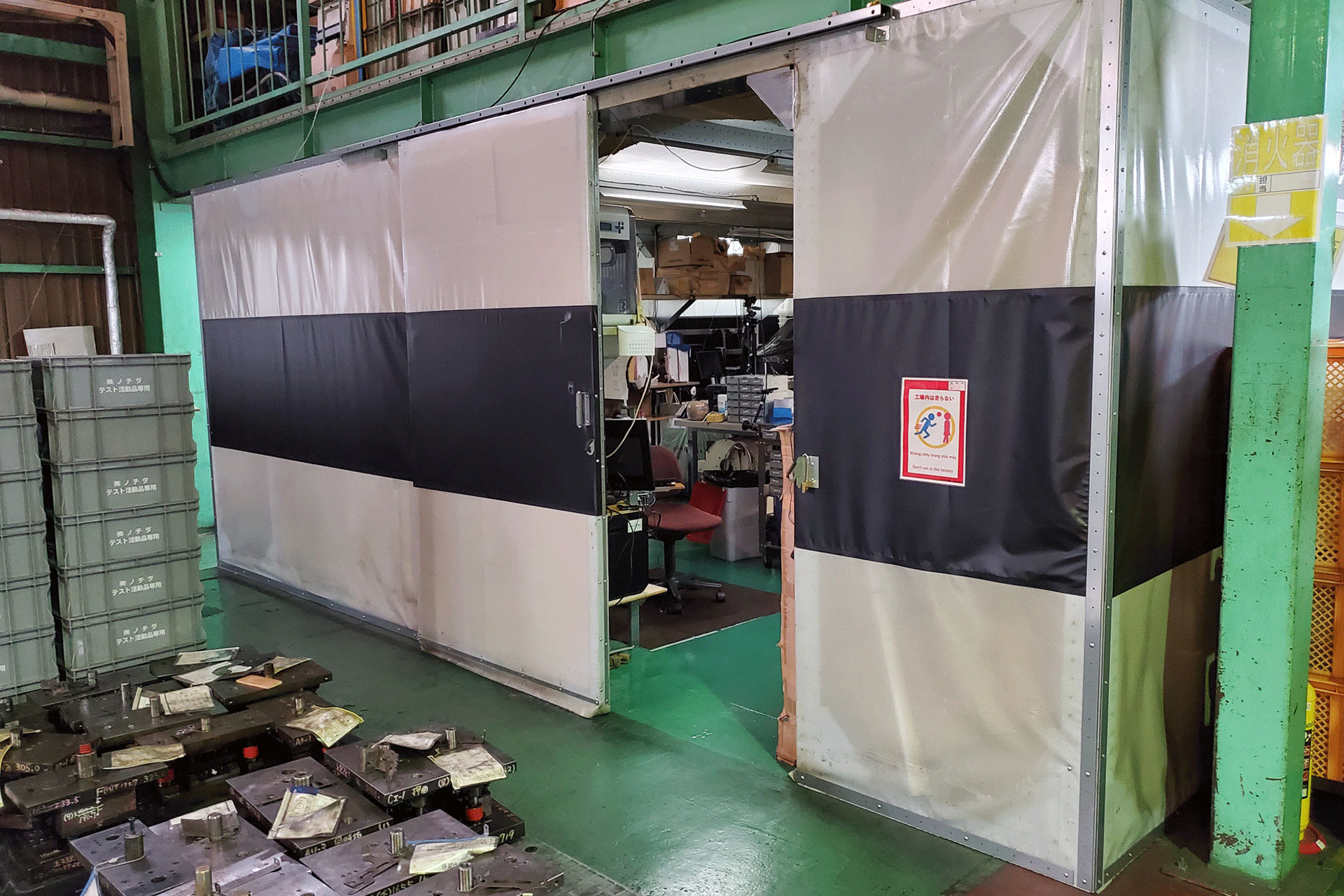
Further improvements will be made through discussions with eftax engineers based on feedback from Mr. Takehashi, who will install the system onsite, such as changing the application to read the barcode on the work instructions into the IoT device and adding a touch pen for screen operation.
The ability to develop in accordance with in-house resources may be a unique feature of eftax’s support style, as if they were running side by side.
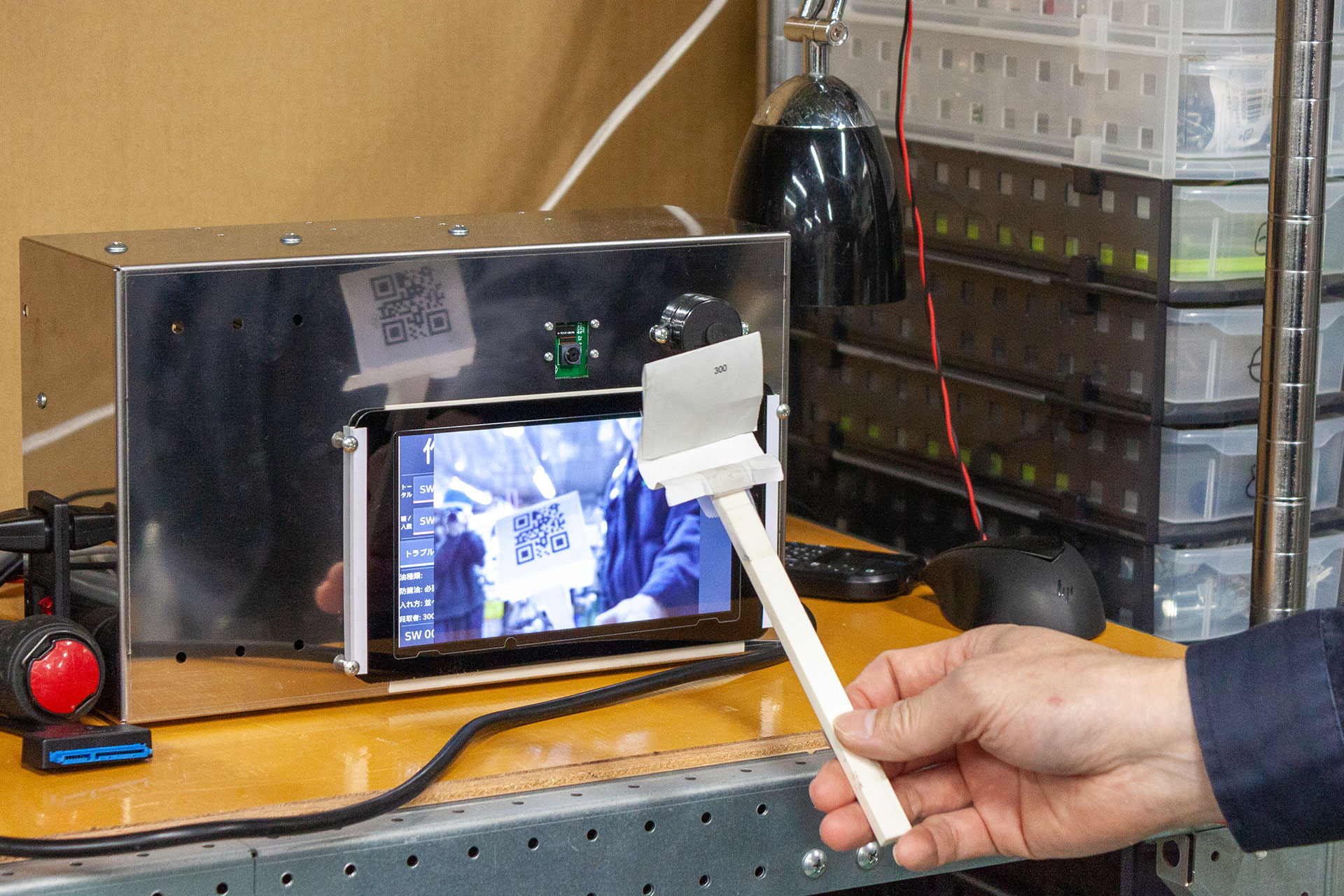
And the benefits of introducing IoT devices were not limited to process control.
“For example, I think that the function that tells the operator when to apply oil will be useful for improving quality,” says Mr. Ihara of the Production Department, and the other members of the team nod their heads in agreement.
“During the stamping process, the machine needs to be oiled, although the frequency varies depending on the product specifications. In the past, there was information that said, “You need to oil the machine only once out of 10 pieces to be processed”. But the operator had to count it in own mind. After the introduction of the IoT device, a beep sound is made based on the information to notify the operator when to apply oil. The worker no longer needs to count and never forgets. This reduces the workload considerably.
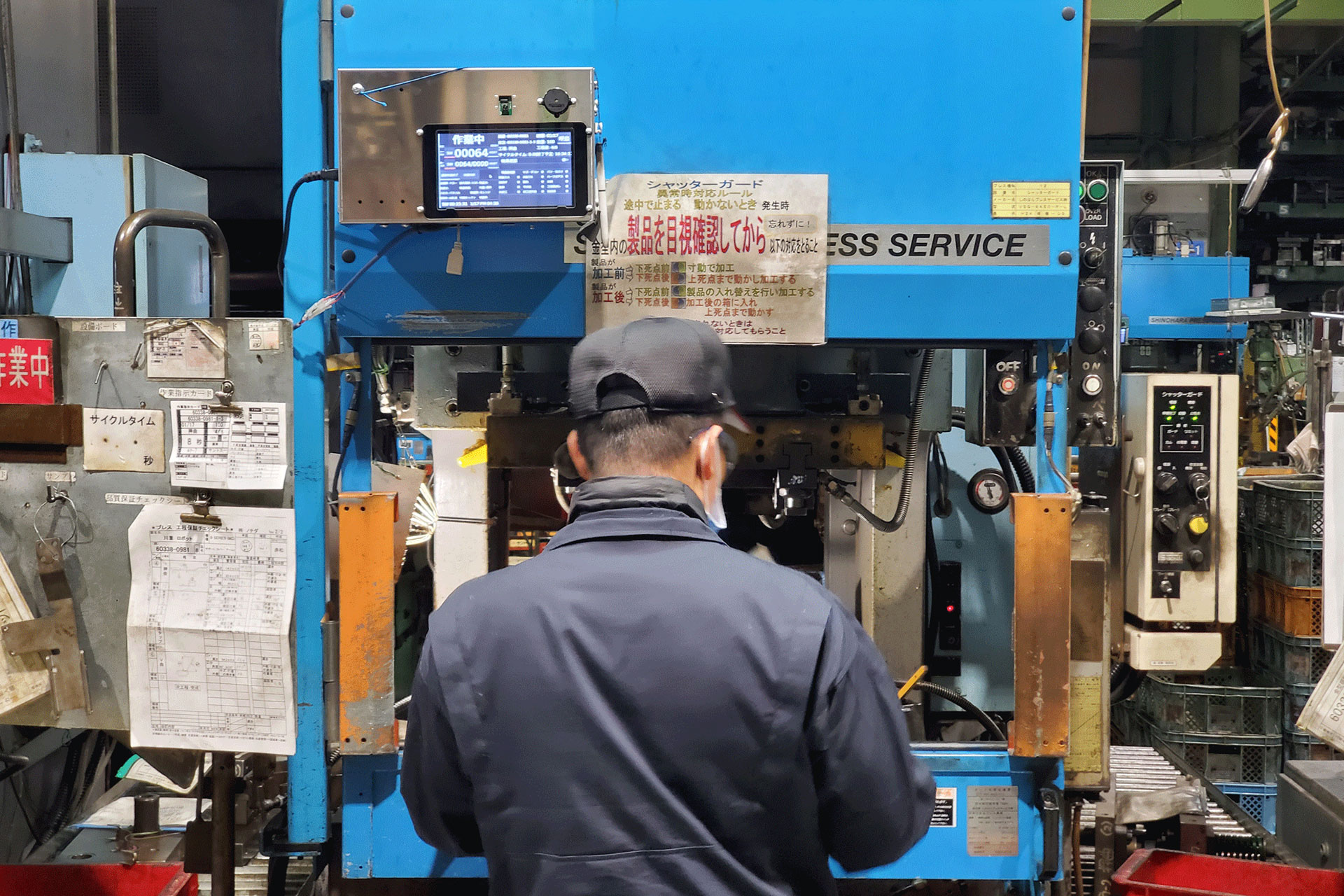
A similar example is the number of boxes. Although the information “X number of products can fit in one box” was already available, the operator had to set it in advance on the machine based on the specification sheet. The box that holds the processed products had to be changed once every 50 times, but there were cases where workers forgot to register the information in the machine and put more than 50 products in the box. Although the machine was designed to stop if the operator forgot to register the box, the operator would only realize that the number of boxes had been exceeded after checking why the machine had stopped…… Now the RaspberryPi picks up the information from the spec sheet and controls it!”
The IoT devices worked well not only for production control, but also for quality control. After installing all the presses, the next goal is to apply them to other processes and utilize the data.
Transforming to a Data-driven Organization
The simplest and most effective process when writing sequences in a program. That is why the press process was chosen as the first IoT implementation site.
One of the difficulties Mr. Takehashi encountered in this project was organizing the complex process.
“Systems are not made up of a single road, but are divided into branches. If you do not define all the branches in advance, you will not be able to use the data when you migrate the system.”
Currently, plans are underway to generalize the system built for press work to spot welding and robotic welding, which have more branches and are more complex.
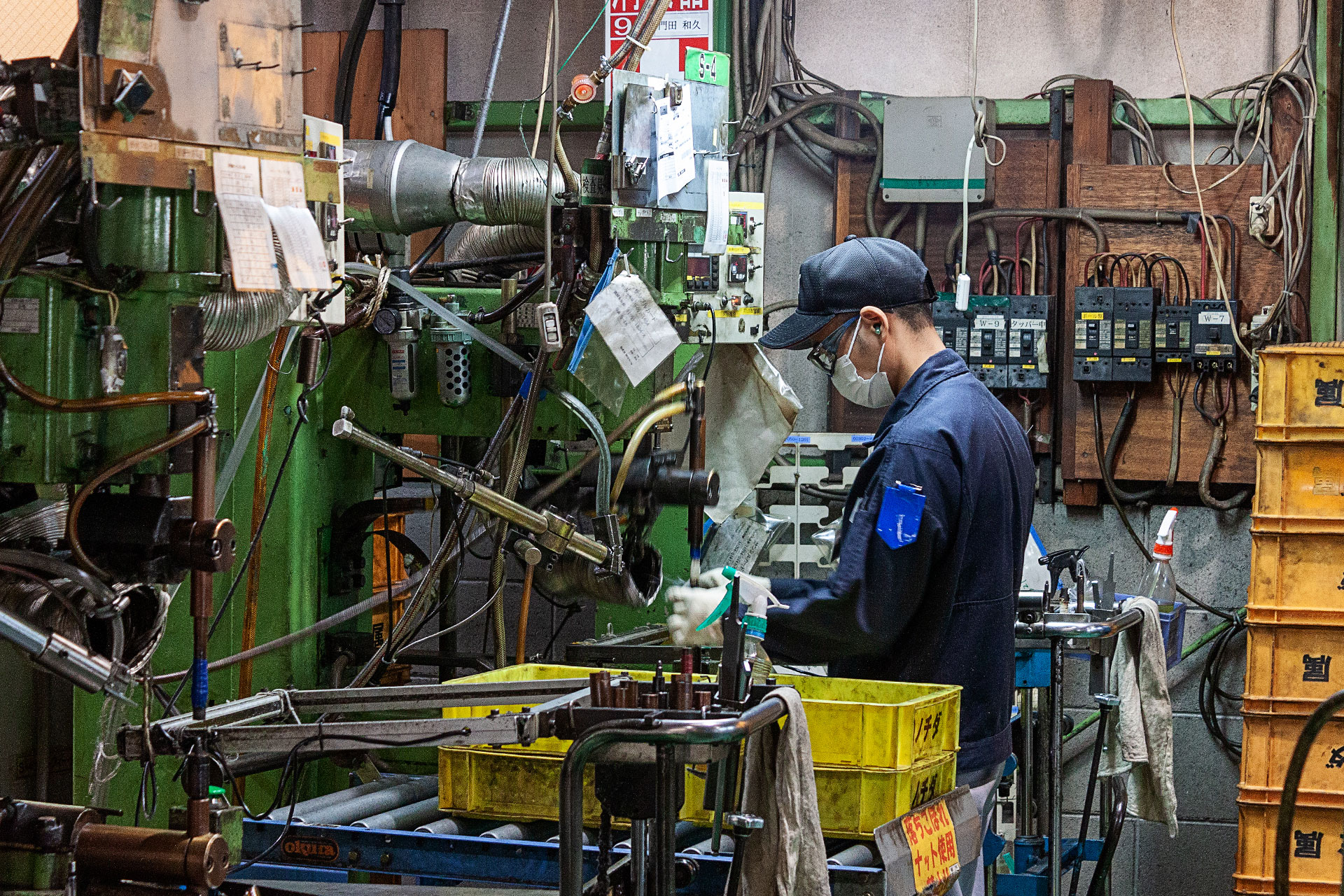
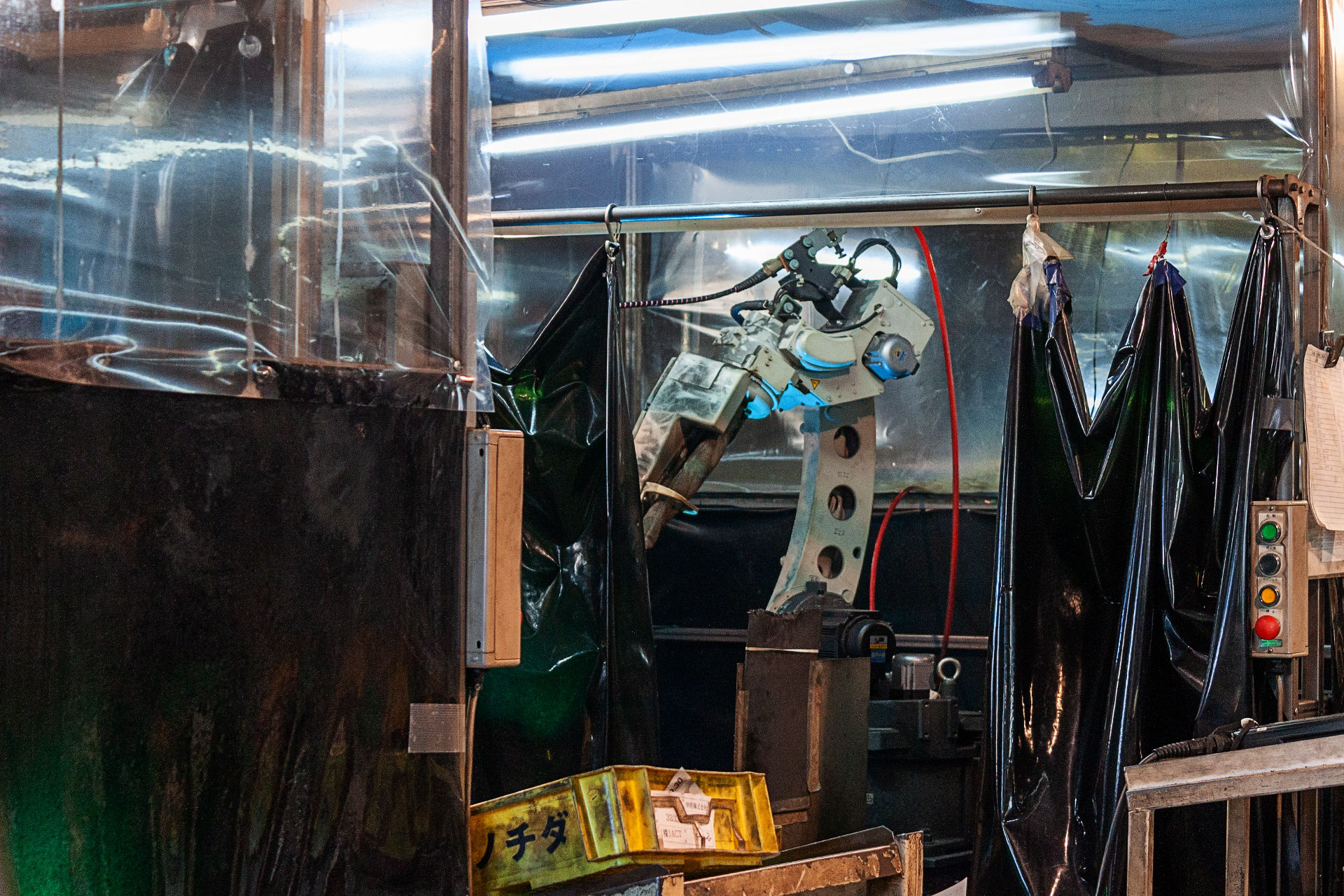
“All the information we want when utilizing the data, we made it cover”, Nochida says. What they are now looking at is the step to build a data-driven organizational structure.
“Once the data is properly obtained, it can be processed and used for management information. In the stamping process where we have introduced IoT devices, we can now see the cycle time (the time required to finish one piece) in real time. The shorter the cycle time, the higher the productivity. In other words, being able to control cycle time means that we can strictly control costs,” says eftax Kobayashi.
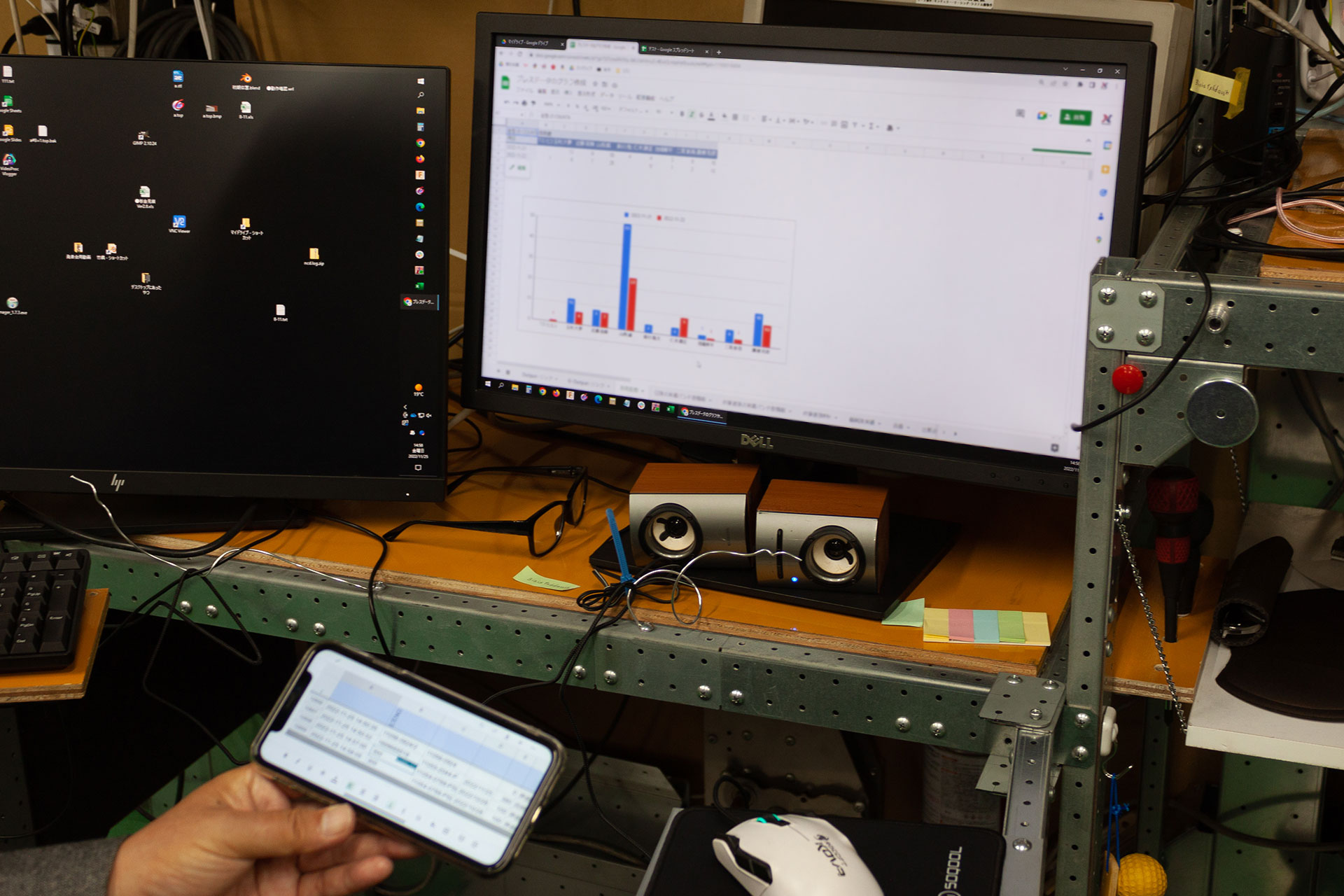
RaspberryPi, a small computer, can be deployed in a variety of possibilities. One example is the “Andon” (a tool used as a means of visualizing the status of lines and facilities) that Mr. Takehashi will talk about next.
“One of the things I am currently discussing with Mr. Kobayashi is Andon. We have many presses and when they have a problem, they sound a buzzer. Currently, we have to scurry around to find out where it is sounding. If we could see at a glance what each piece of equipment is doing and who is processing what, it would be clear what we should do next.”
Regarding the planned Andone, Mr. Kobayashi states the following.
“IoT connects things to a network to exchange information and control each other. In this project, we are also sending data from RaspberryPi to the cloud through Wi-fi. Based on the production information that is up in the cloud, you can get information about production from within the company or from your sales destination. If you create an Andon based on that data, you can display it whether you are in the first or second factory.”
Infinite Possibilities Expanded by IoT
In this way, eftax Mr.Kobayashi and Nochida Mr.Takehashi have built a production management system as if they were running in tandem. Their relationship began when they sat next to each other at MISERUBAYAO, a place where manufacturing companies communicate with each other.
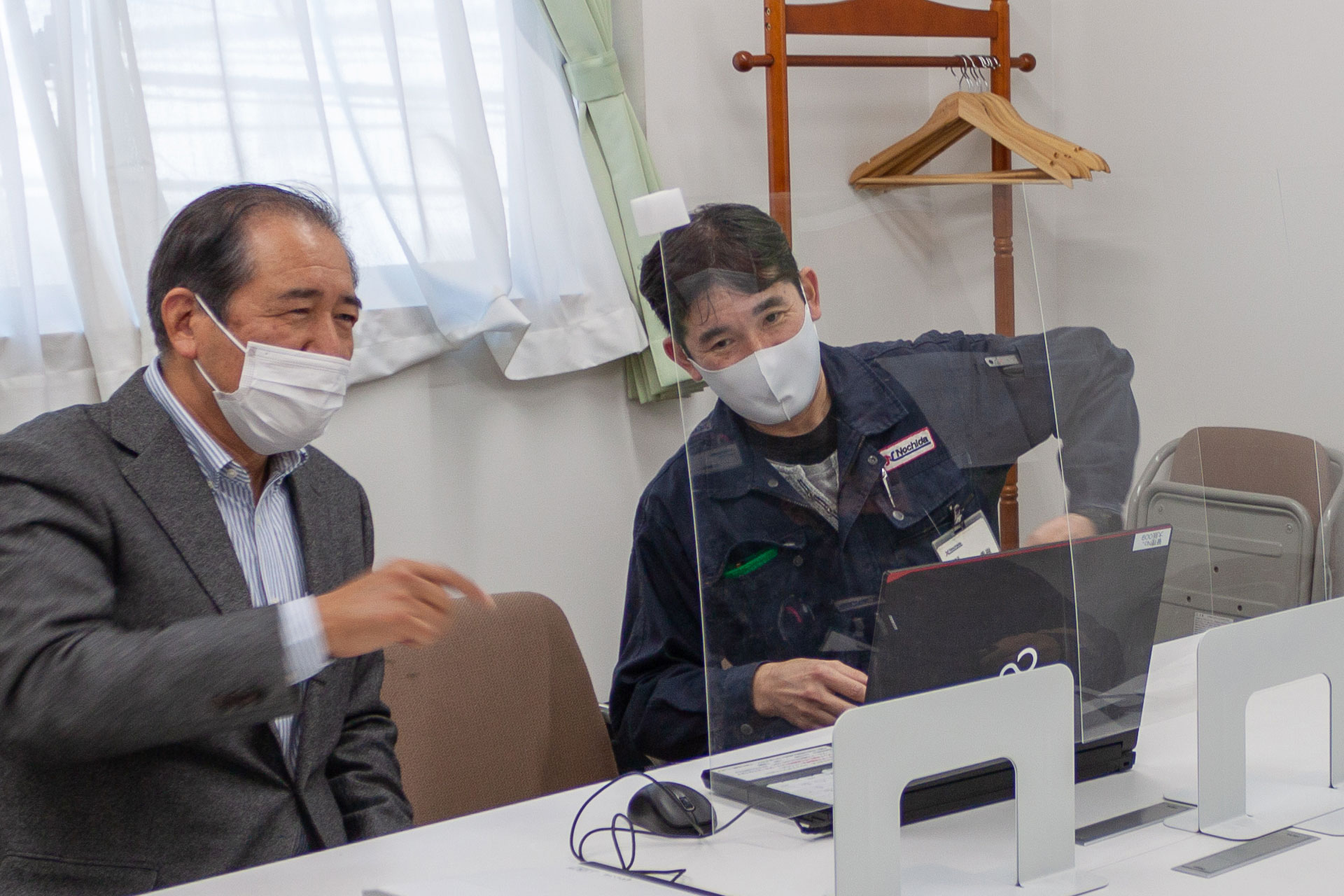
“Since then, I have participated in workshops and gone on factory tours to companies in Yao with him. I still participate in the IoT study group that Mr. Kobayashi holds every other week,” said Mr. Takehashi.
Is it useful for you?” Mr. Kobayashi asks, “It always makes me realize how much I can do with it.” Mr.Takehashi replies with a smile, and continues as follows.
“After interacting with Mr. Kobayashi and listening to him, it occurred to me that with his skills, we would be able to realize production management using RaspberryPi. If going all the way, I thought it would be better to work with eftax, a friendly, consultative company. With this in mind, I took the matter up with the company.”
What was the actual reaction at the company?
“To be honest, there are a variety of production management systems just by looking at them at trade shows. However, it is difficult to find one that fits our company exactly. When we talked to eftax, we got the feeling that they could handle it, so we started the project.” Mr.Ihara said.
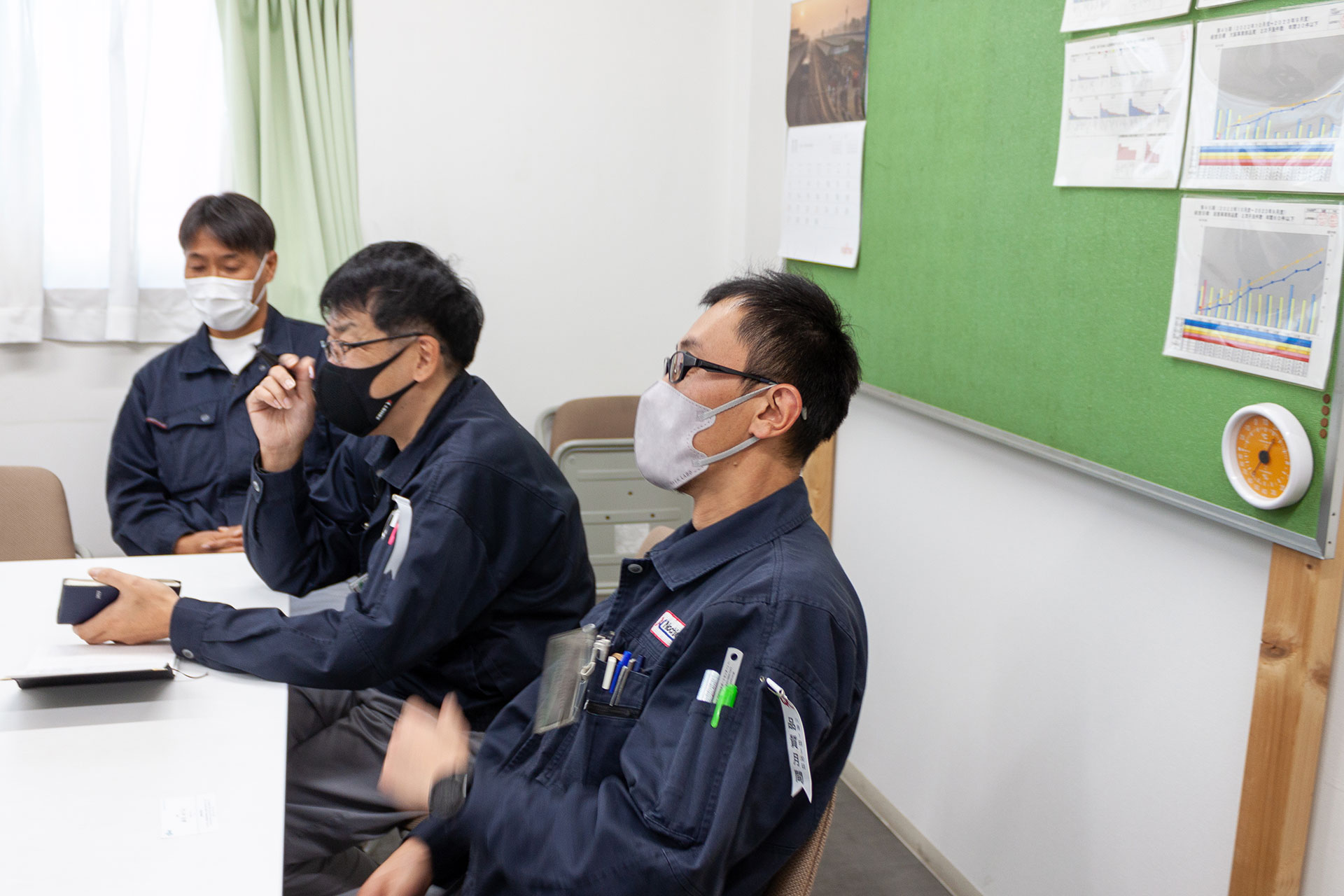
In contrast, “Accounting systems are almost the same, but production management is really different everywhere. However, unless you can properly manage the production process, production efficiency will not improve,” eftax Mr.Kobayashi concurs.
“Being able to do that on one’s own would be ideal, and I believe that is exactly what I am helping them to do. I think we will see more and more developments in AI in the future. For example, since Nochida has developed robotic welding technology, we have analyzed data based on that technology. I’m thinking that if AI can pick up sound, judge changes in sound in real time, and output the data, it could be used for something,” said Kobayashi.
On the other hand, Mr. Takehashi’s current goal is to promote it within the company.
“I am promoting various ways, such as using Google services to share information, but there is a limit to what I can do on my own. It would be nice if the data from the RaspberryPi became useful, and if it actually proved effective, and if opinions like “I wish we could do something like this” could be voiced within the company. I would like to be the first to take the lead, and I hope that we can gradually expand the scope of the project from now on.”
While talking about the above, one idea came out , “It would be nice to apply this technology to scratch identification.” from Mr. Ihara.
“I am already getting senile (laughs). It would be nice if a computer could see those things. The other thing is setting mistakes. I am asking if it would be possible to identify them with a camera, because if they are processed in a distorted state, they will be defective.”
The good thing about this unique eftax style of accompanying support is that it is not a ready-made product, so it can be set up in any way necessary. It is expected to be developed in a variety of areas in the future.
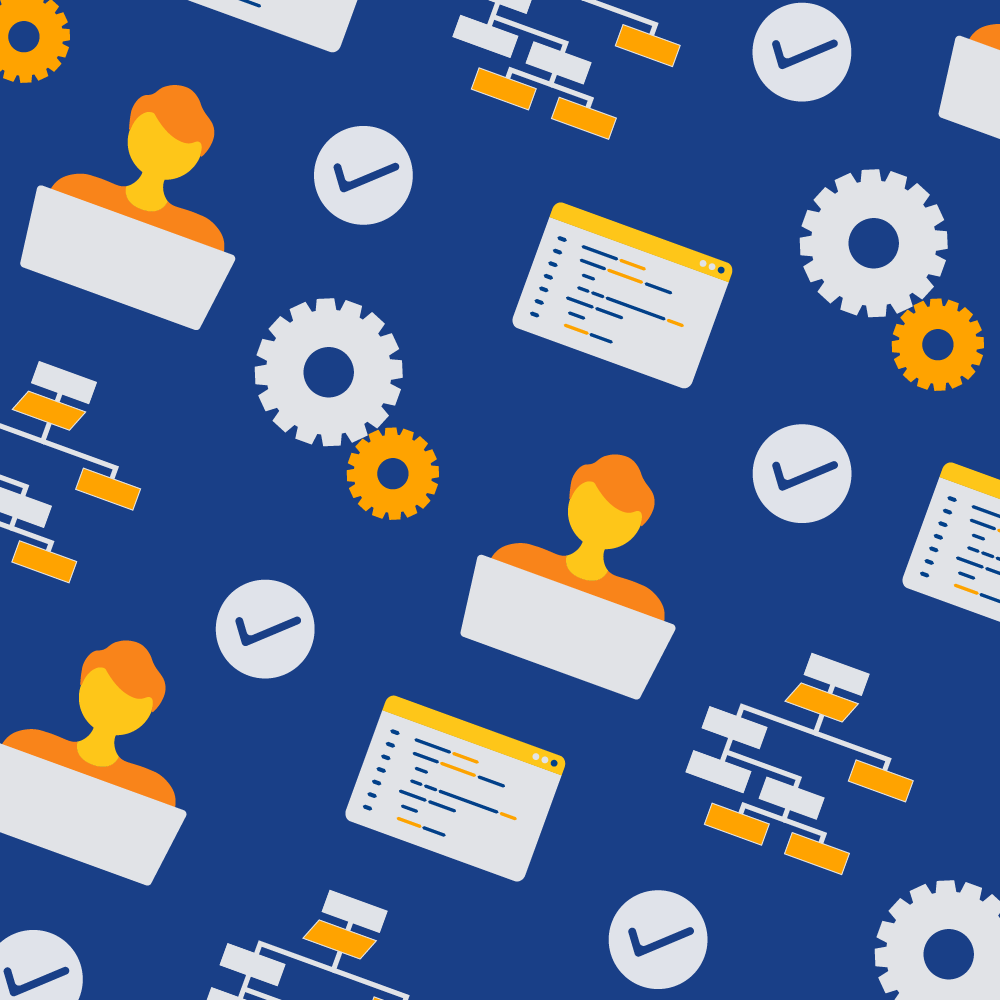
Construction and Operation Support of LMS (Learning Management System) at Kobe University
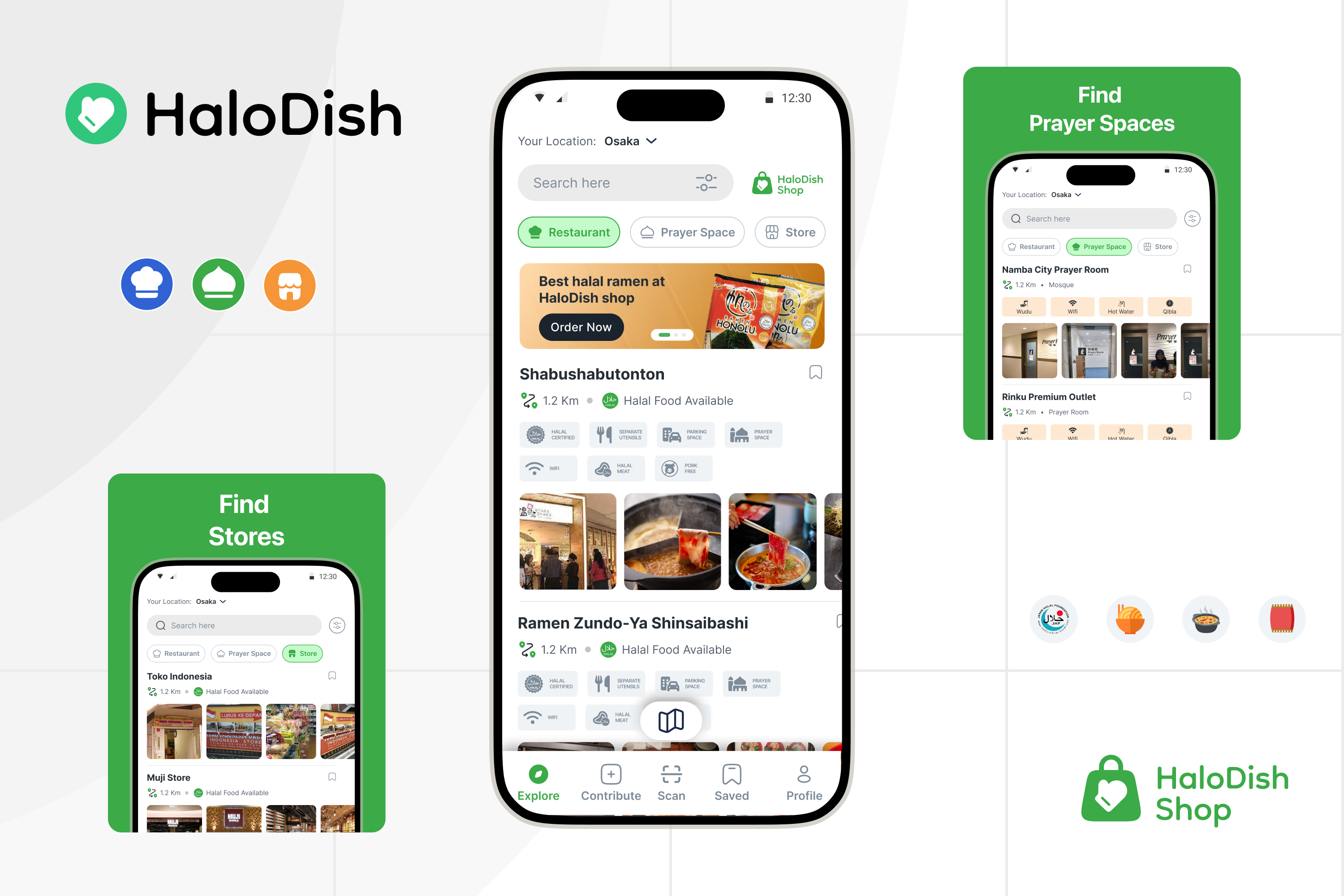
Cross-border app development: a roundtable discussion about collaboration, planning and development of halal locator app, HaloDish
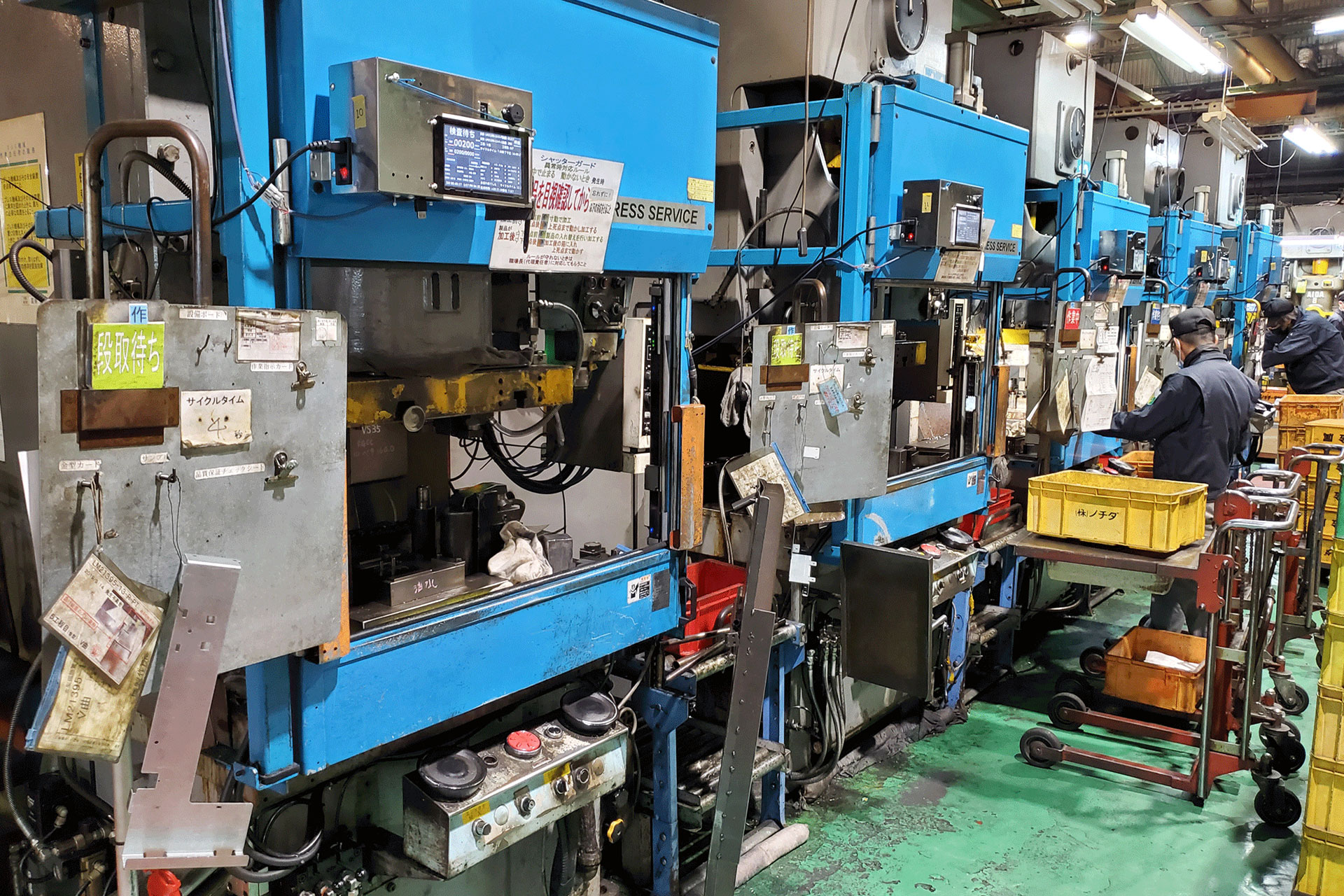