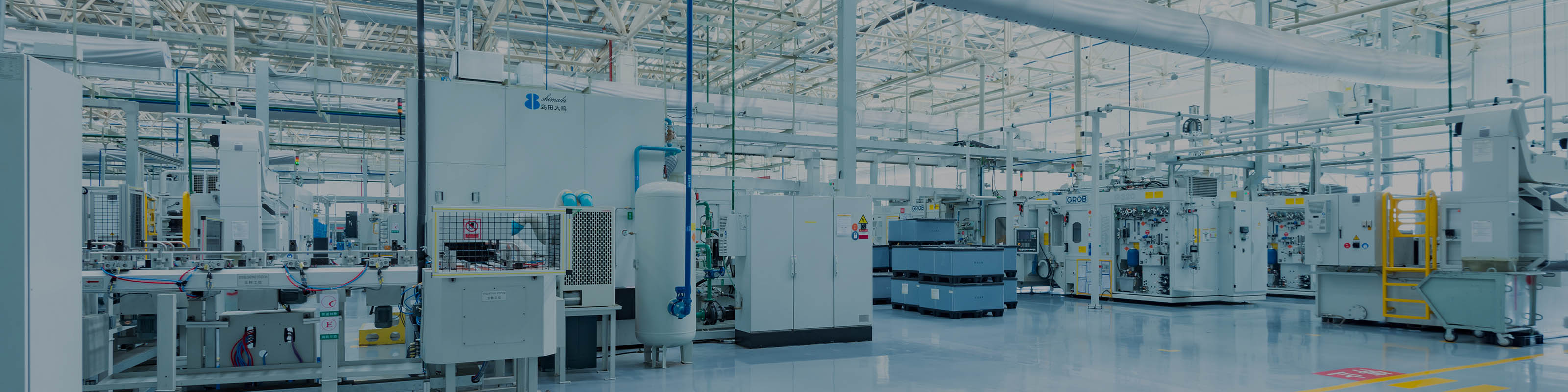
Product / Quality Control Case Study Utilizing AI/IoT Technology at Kane-M Industry Co., Ltd.
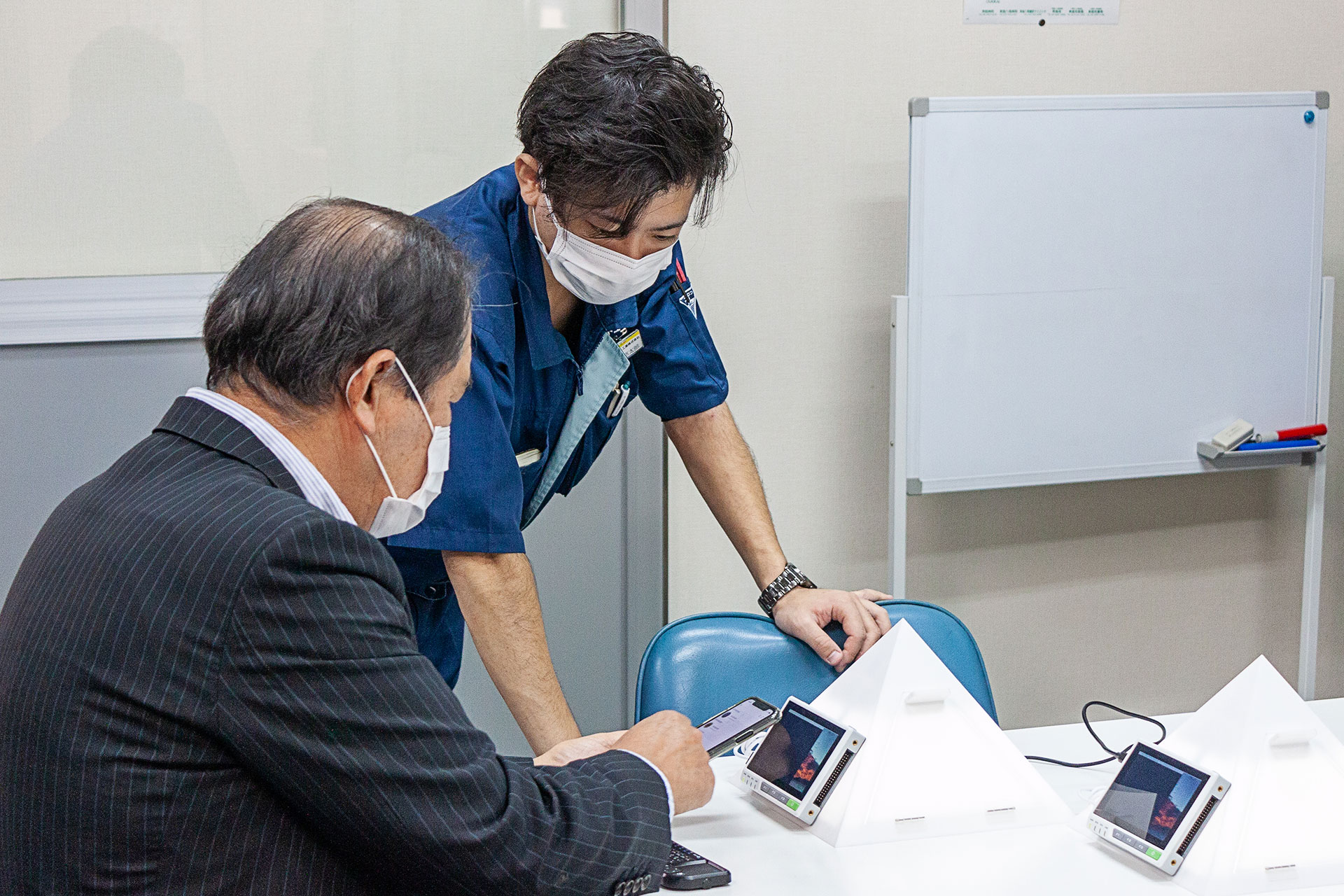
Development of Product / Quality Control System Utilizing Image Recognition Technology
Purpose of Introducing IoT System
Establishment of a quantitative quality control system for products
Our Areas of Responsibility
- System planning and design
- Development of IoT devices
- Data migration and various application settings for existing products
The Voice of Mr. Kitamura, Kane-M Industry Co., Ltd.
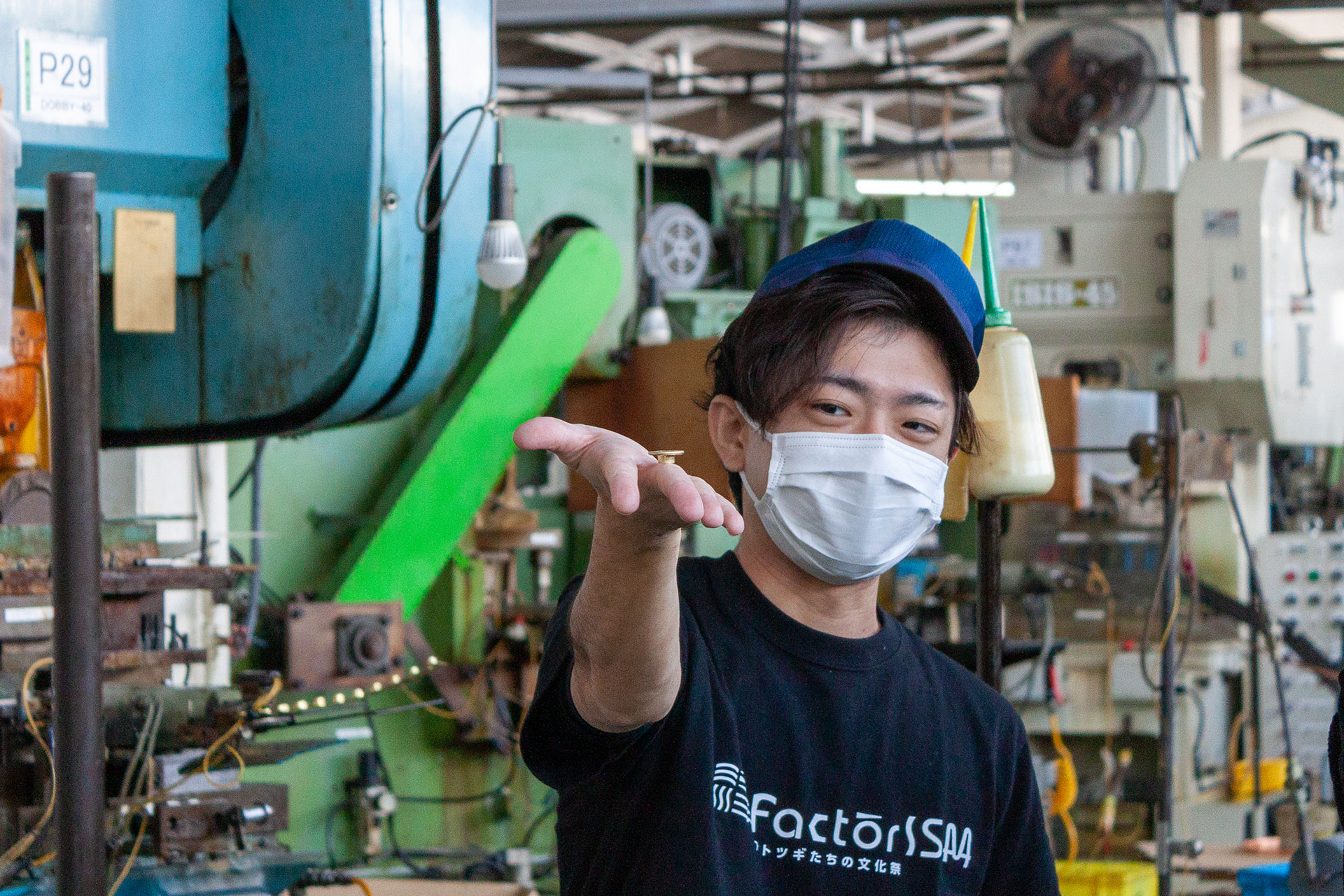
Strengths and Challenges are Inextricably Linked
Diverse Products and Technologies
Kane-M Industry is an auxiliary materials manufacturer that develops and supplies jeans buttons, rivets, dovetails, and other products with superior design and functionality under the slogan “Create the Future of Parts”.
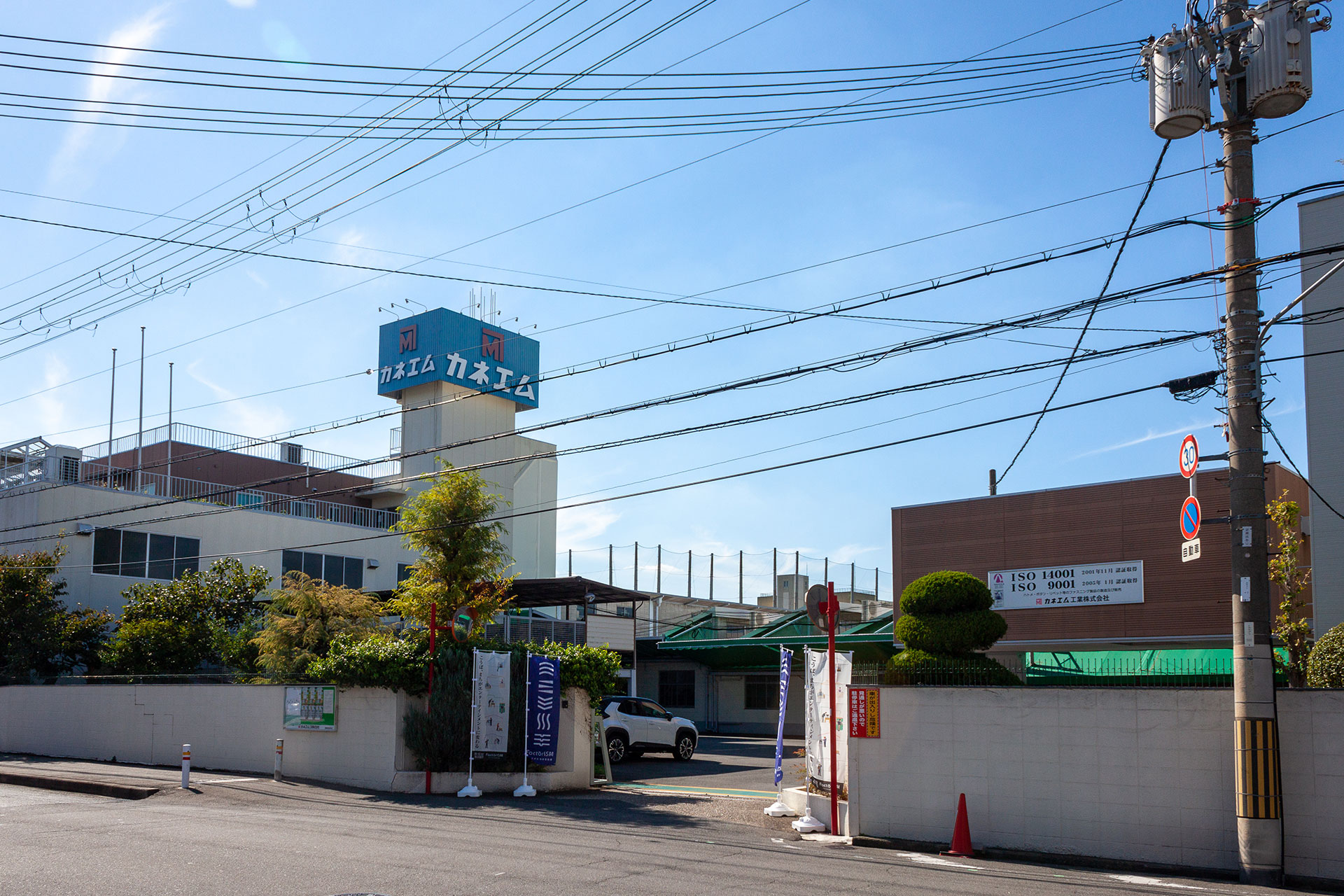
Our products are used in everyday life in such apparel products as sneaker doilies and coat buttons, as well as in automotive floor mats and construction sheets. You may even find our products on your clothing.
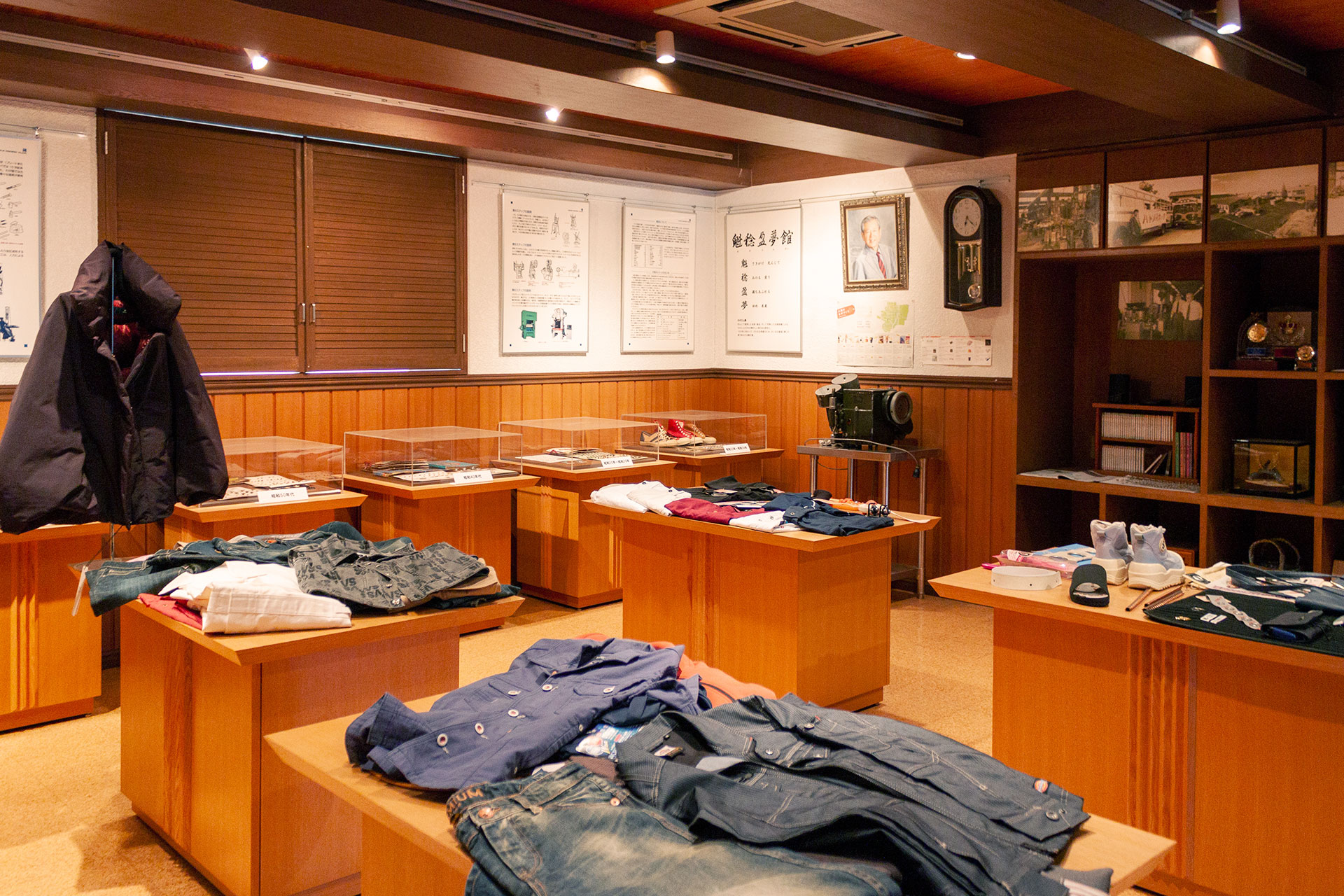
The daily production of jeans buttons ranges from about 2 to 3,000 hand-assembled buttons to about 25,000 machine-assembled buttons of one type.
Many of our customers are particular about design and function. We are creatively engaged in daily technological development to meet a wide range of customer needs and to propose new value-added solutions.
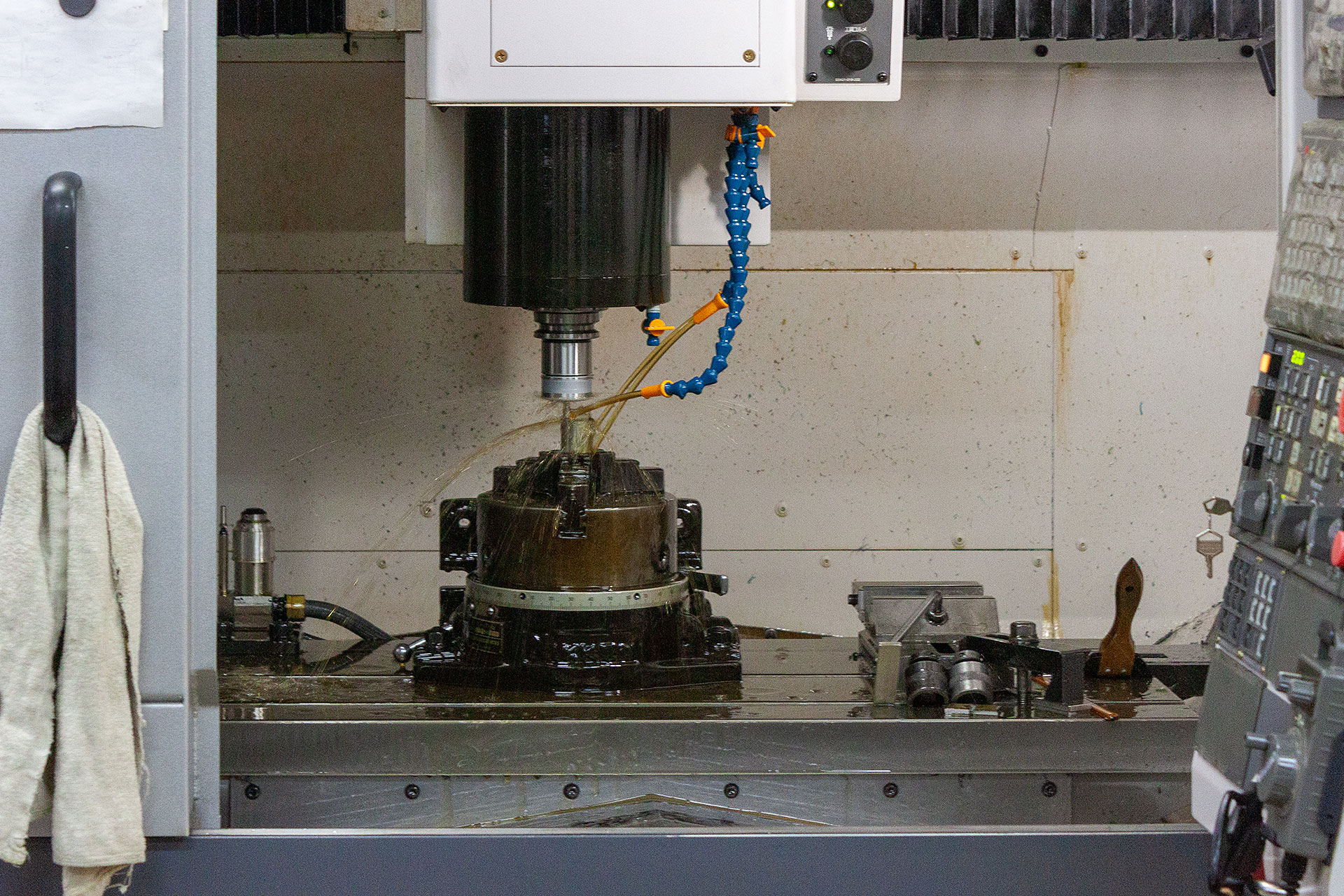
Our unique strength is the integrated production of highly original products by multiplying various processes, such as adding design to press work. Two to three new designs are created every day.
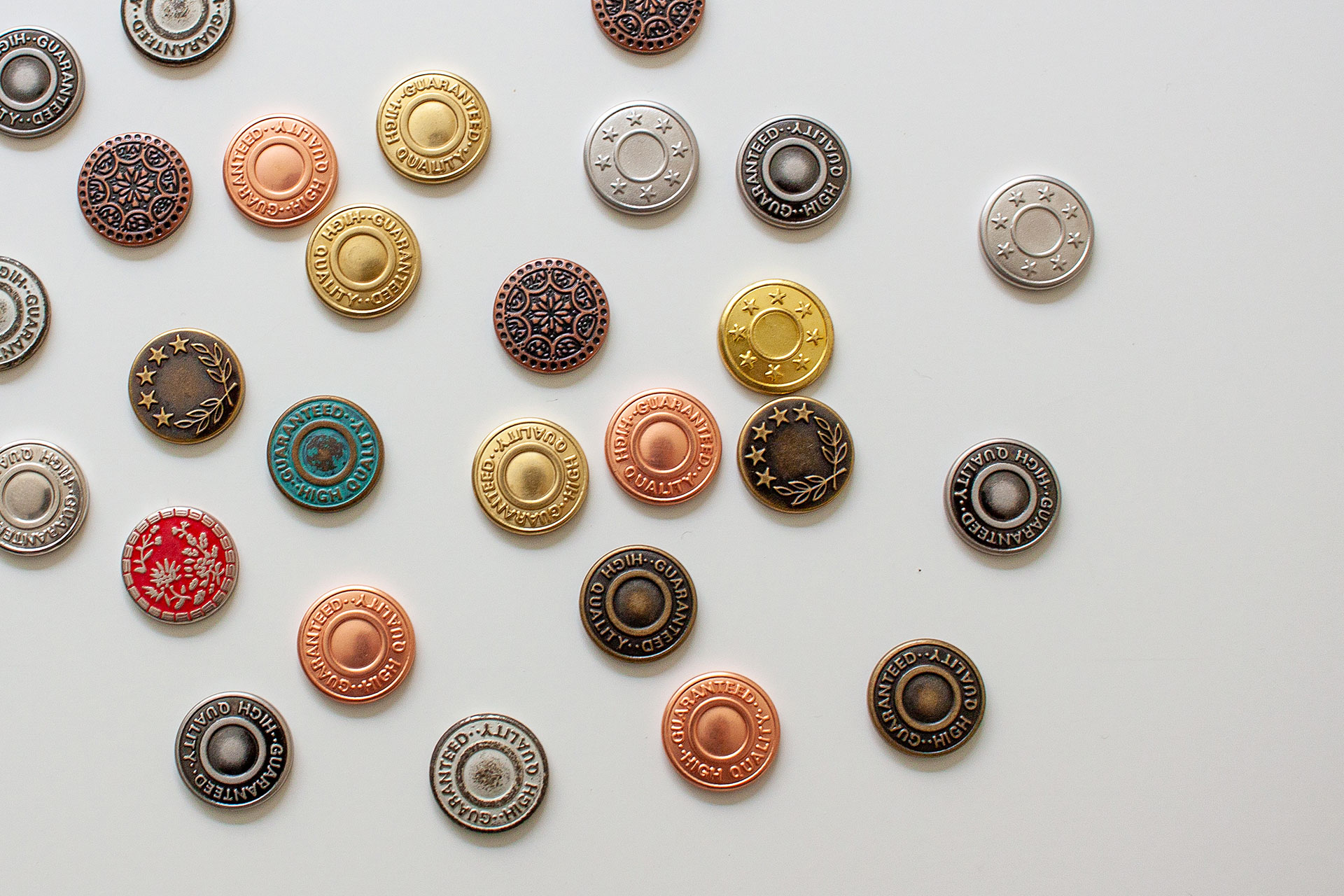
However, we also saw the challenges that come from being able to respond to a wide variety of needs. The development of this system was the solution to this problem.
Quantify Color and Make It a Common Language
We ask our subcontractors to do electrolytic plating, but the color of the plating is sometimes blurred.
For example, the color P-HBK has a glossy blackish tint. We must have the color finished to “this color,” but when we look at the finished product, the color may differ. This tends to be a problem in communication with plating companies.
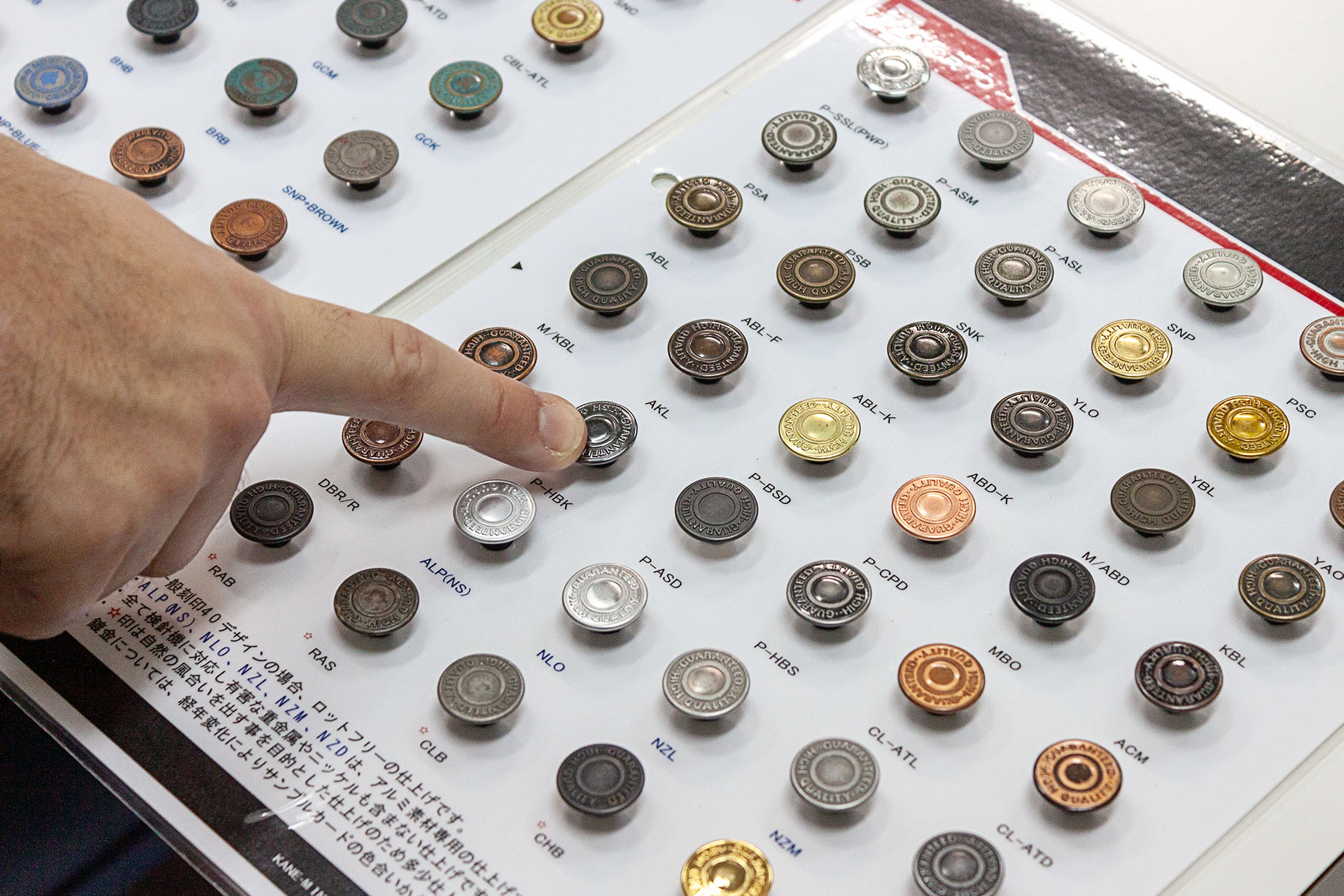
If we can’t capture color quantitatively, then “…on what basis is it black?” and it will be an endless argument.
The same is true not only for the plating company, but also for in-house. Processing, mainly antique colors using chemicals such as caustic soda, is done at Kane-M industry.
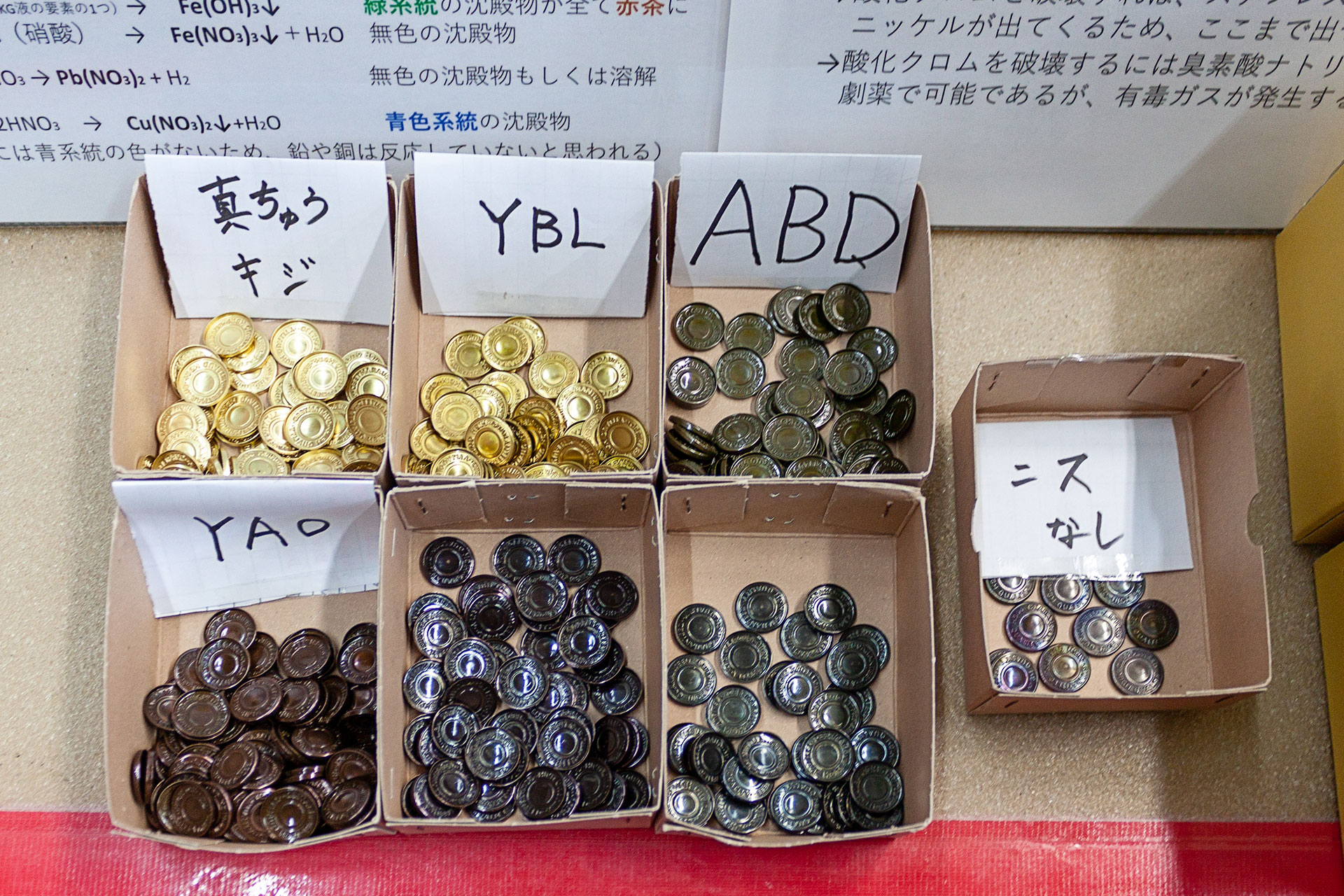
If the color can be quantified, instead of a person comparing the sample and the finished product, for example, we can define that if the color is 92% or more similar to our standard, it is OK, and if it is less than that, it is not the right color.
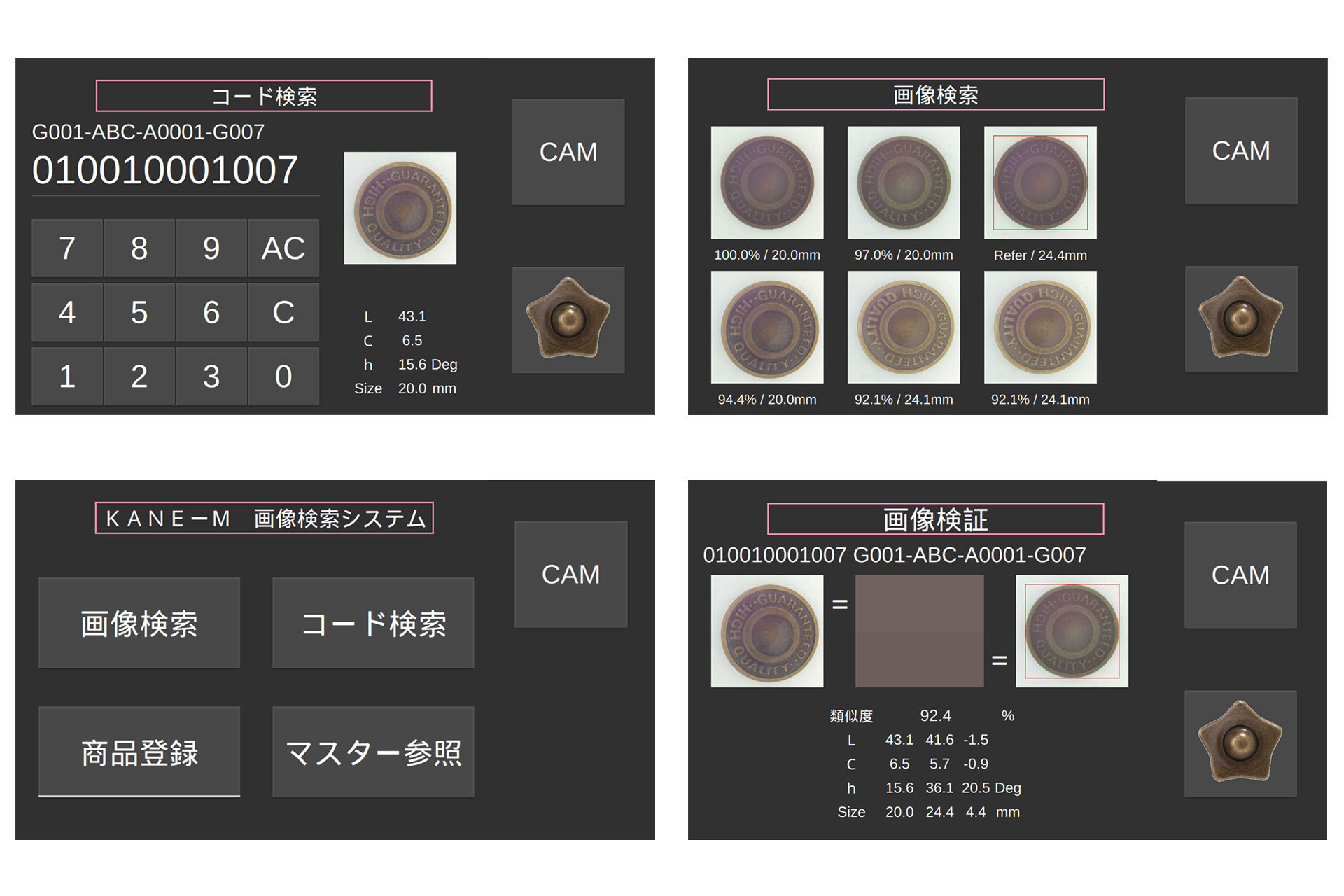
These indicators are not the only color-related issues.
Since metal is colored by plating or chemical coloring, it oxidizes and darkens over time. Even if you keep track of your products in a sample book, the question arises as to when this sample book was made. For example, the color of a freshly made YBL is technically a bit lighter than this sample book.
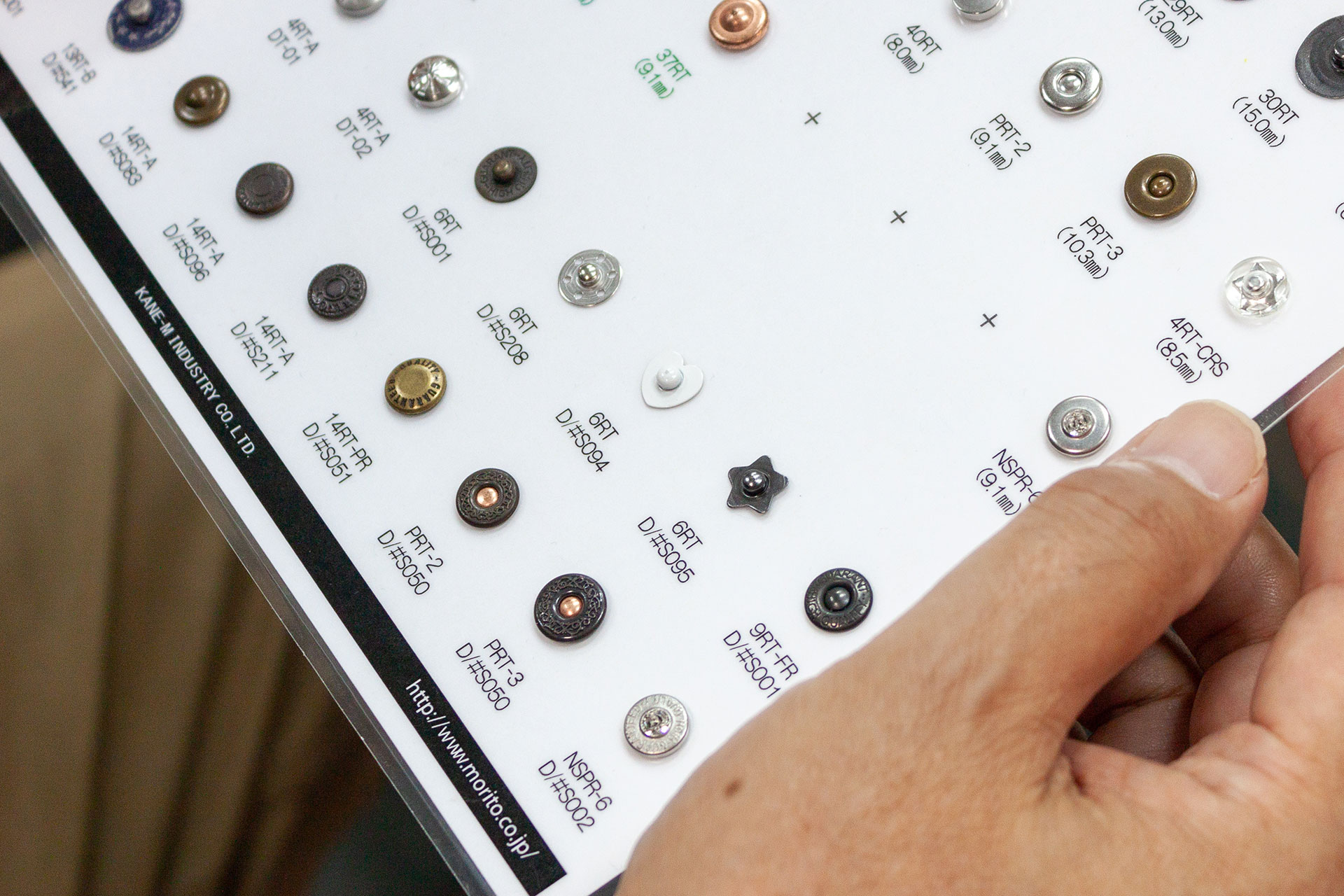
As the sample book of actual samples deteriorates over time, it is best to keep data of images taken in the same environment. Although we have been working on photo shooting, there was a problem that the images and the actual product were totally different due to the different shooting environments.
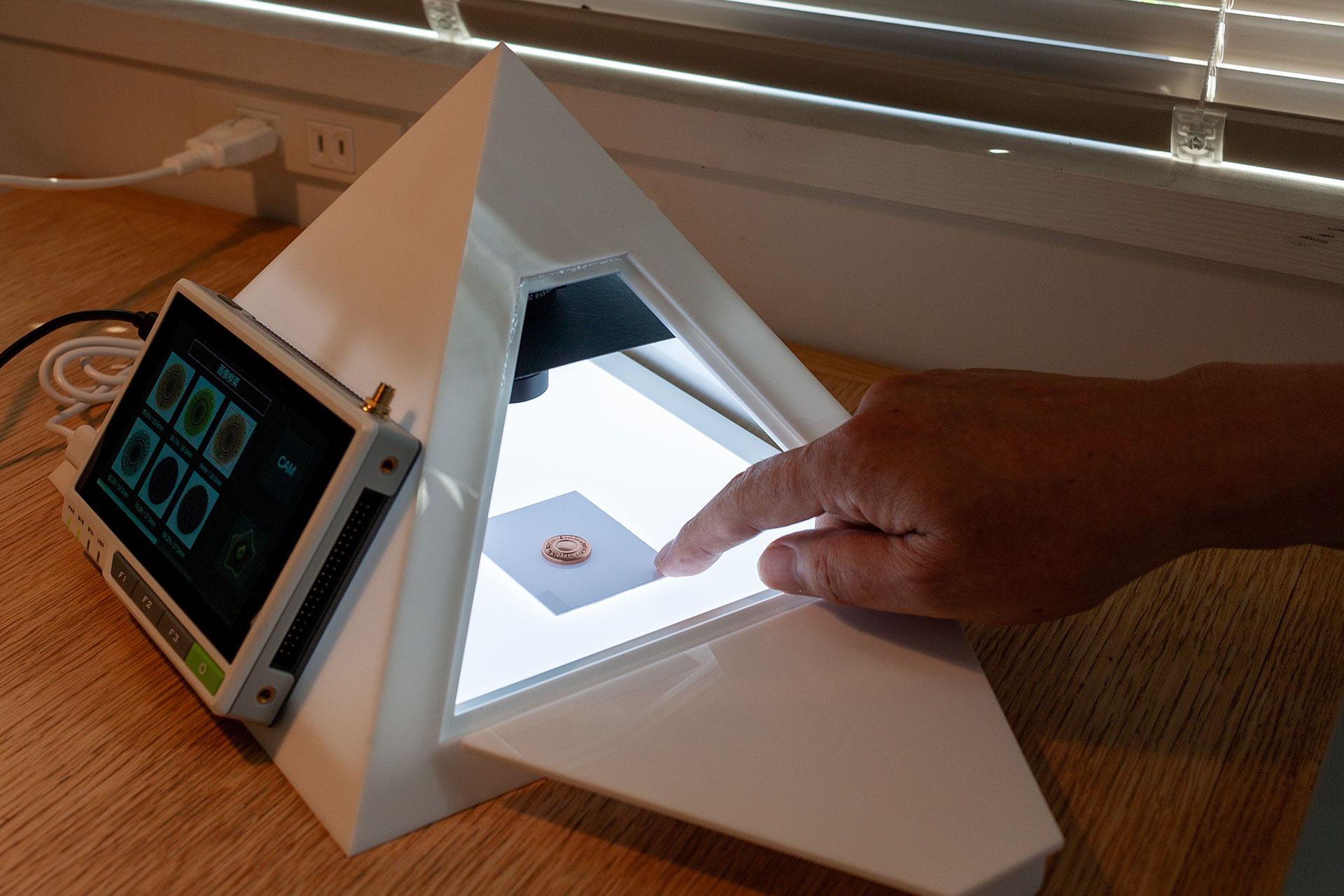
Because of these problems, I have always thought, “I would like to have something that sees color quantitatively, not by human senses”. I heard that our company had already tried this 5 or 6 years ago, but it was difficult to achieve at that time.
With these issues in mind, I visited the DX Forum held at MISERU BAYAO, thinking “I would like to introduce a new system”.
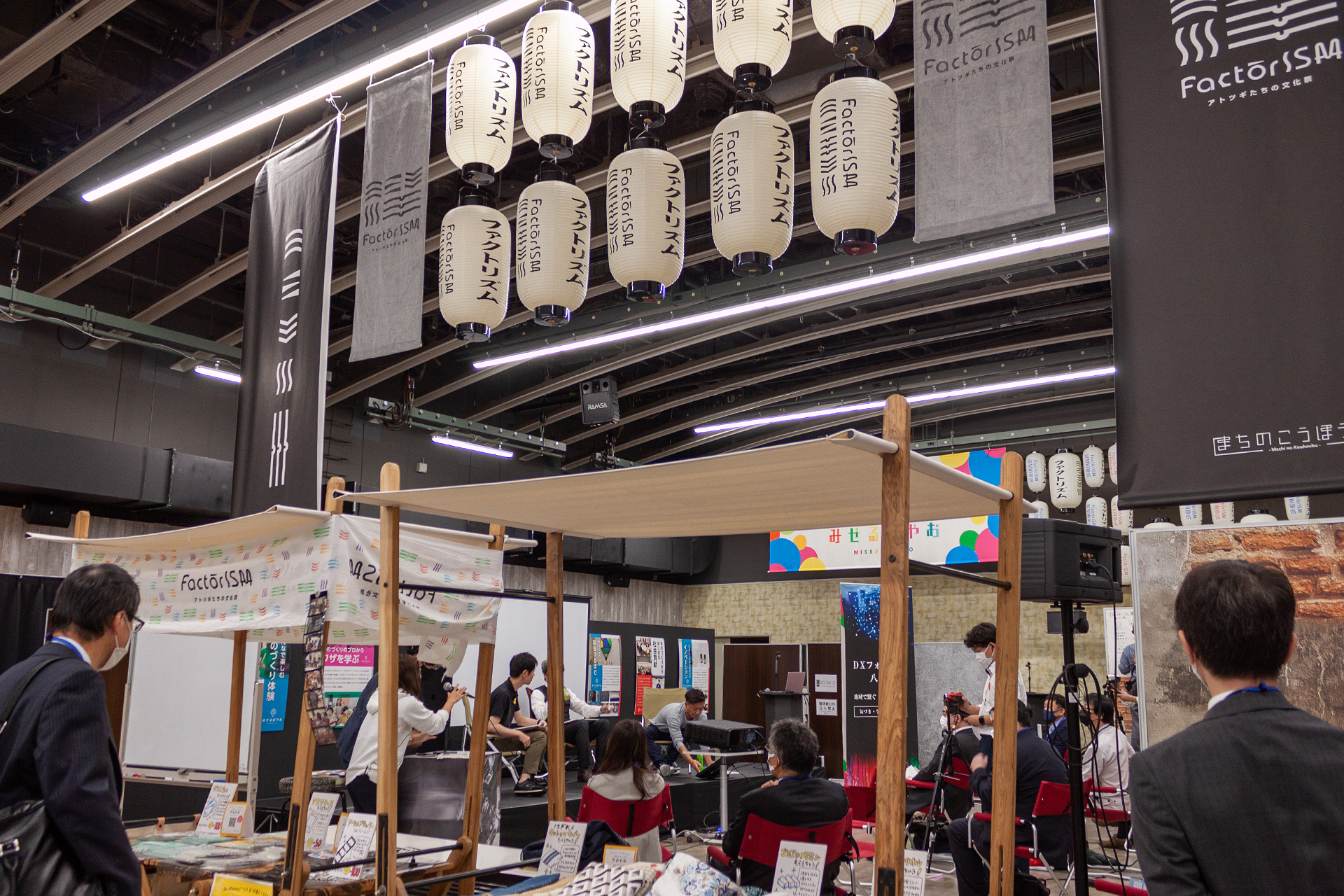
Mr. Kobayashi of eftax was demonstrating his quality control imaging system at the booth of Abel, well known for “Abel Black”.
So I asked him, “We have this problem, and I wonder if you can make something that can solve it”. That was the beginning of this project, a year ago.
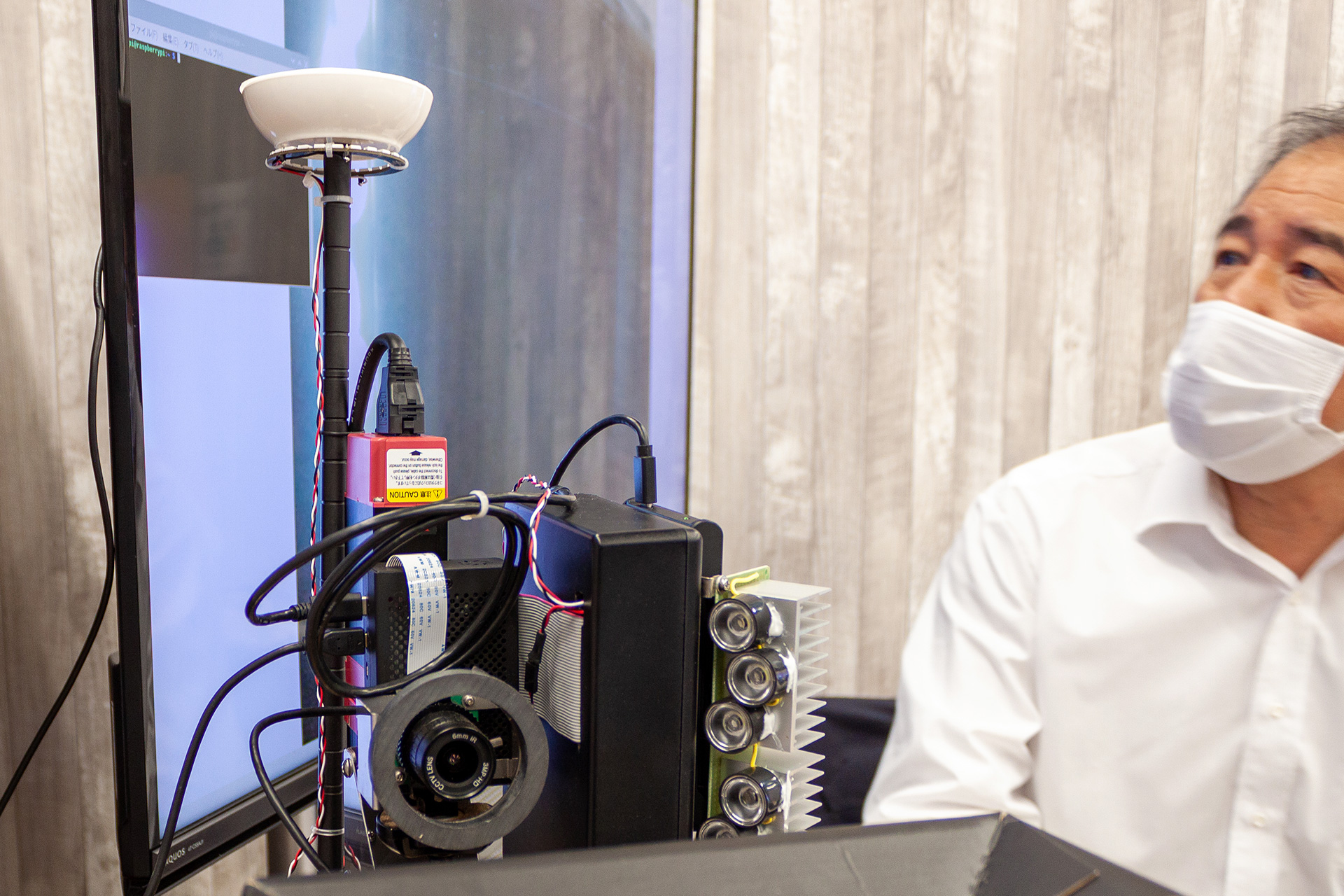
Discriminate Designs and Build an Inspection System
As I have said, the idea of “quantitatively judging color” was the starting point of our project, but if we could do that, there was one more thing we wanted to do in addition. That is, “to distinguish differences in design.
We receive orders for parts of various designs from various customers. What must not happen is that a part with a brand name on it is mistakenly delivered to another customer. Basically, this should not happen, but as long as human operators are involved, human error is not zero. I thought it would be best if we could realize a system that could manage to suppress such errors as well as quantitative color judgments.
The idea was that if we were going to take a picture to determine the color, it would be better if we could also determine the design using the same picture. We have introduced a variety of machines for inspections, but until now we have only been able to compare designs by human inspection.
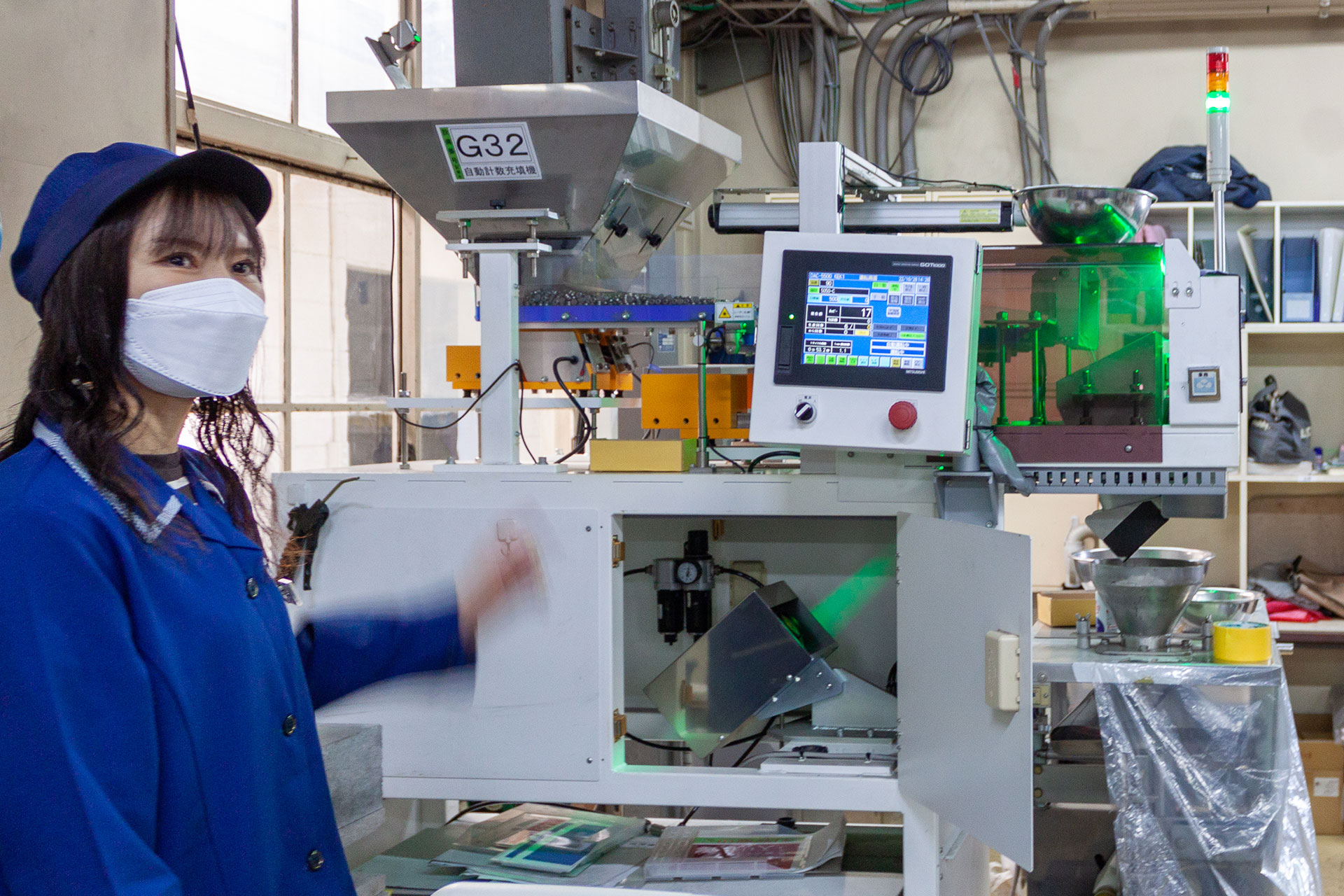
Design discrimination is not limited to differences in design. If we can quantify the degree to which we can allow for the depth or shallowness of the engraving, we can save the correct answer and make a judgment.
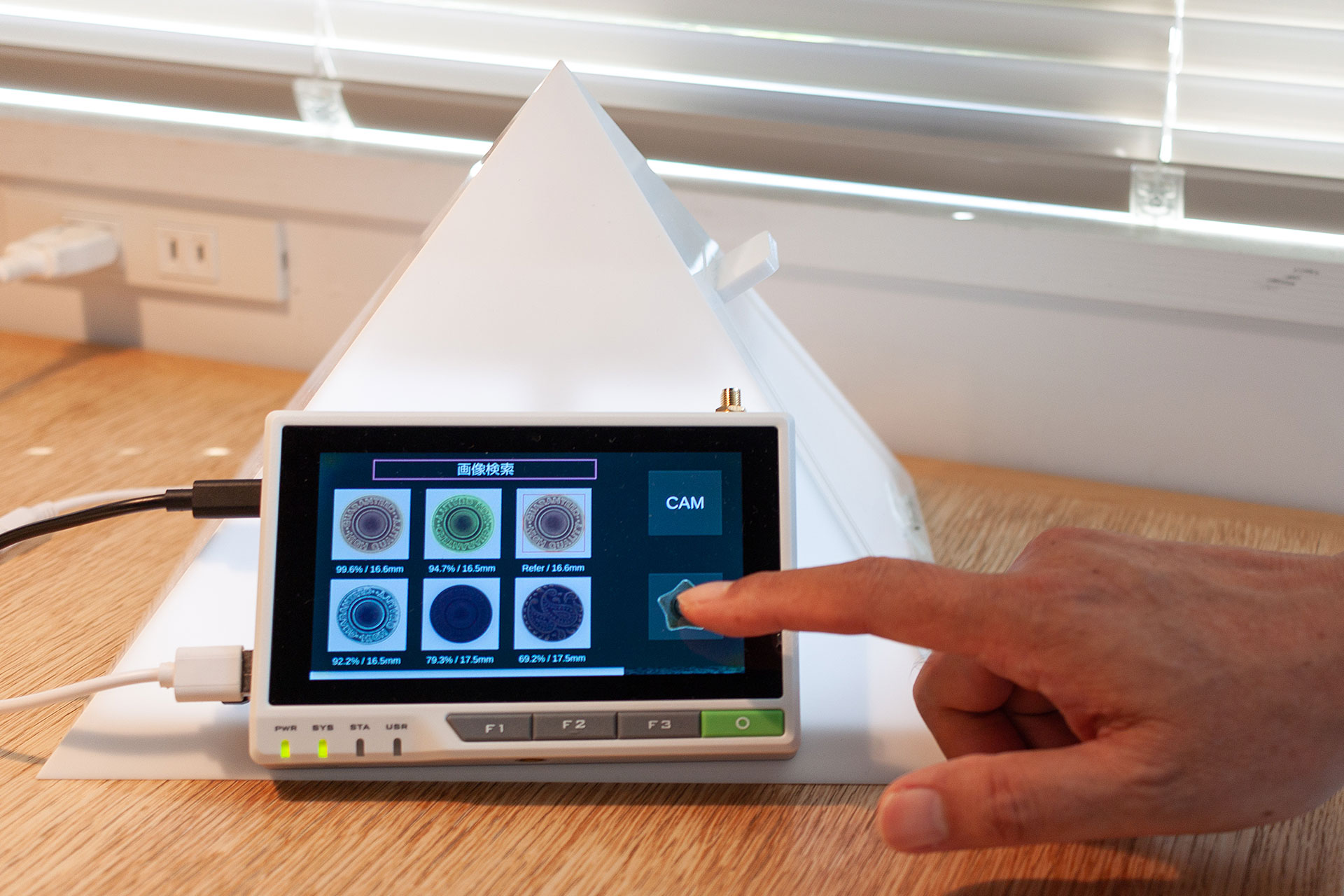
Quantitatively determine color. It should be able to distinguish between designs. The system should also be easy to use in the flow of business. We consulted with eftax Mr.Kobayashi from these perspectives.
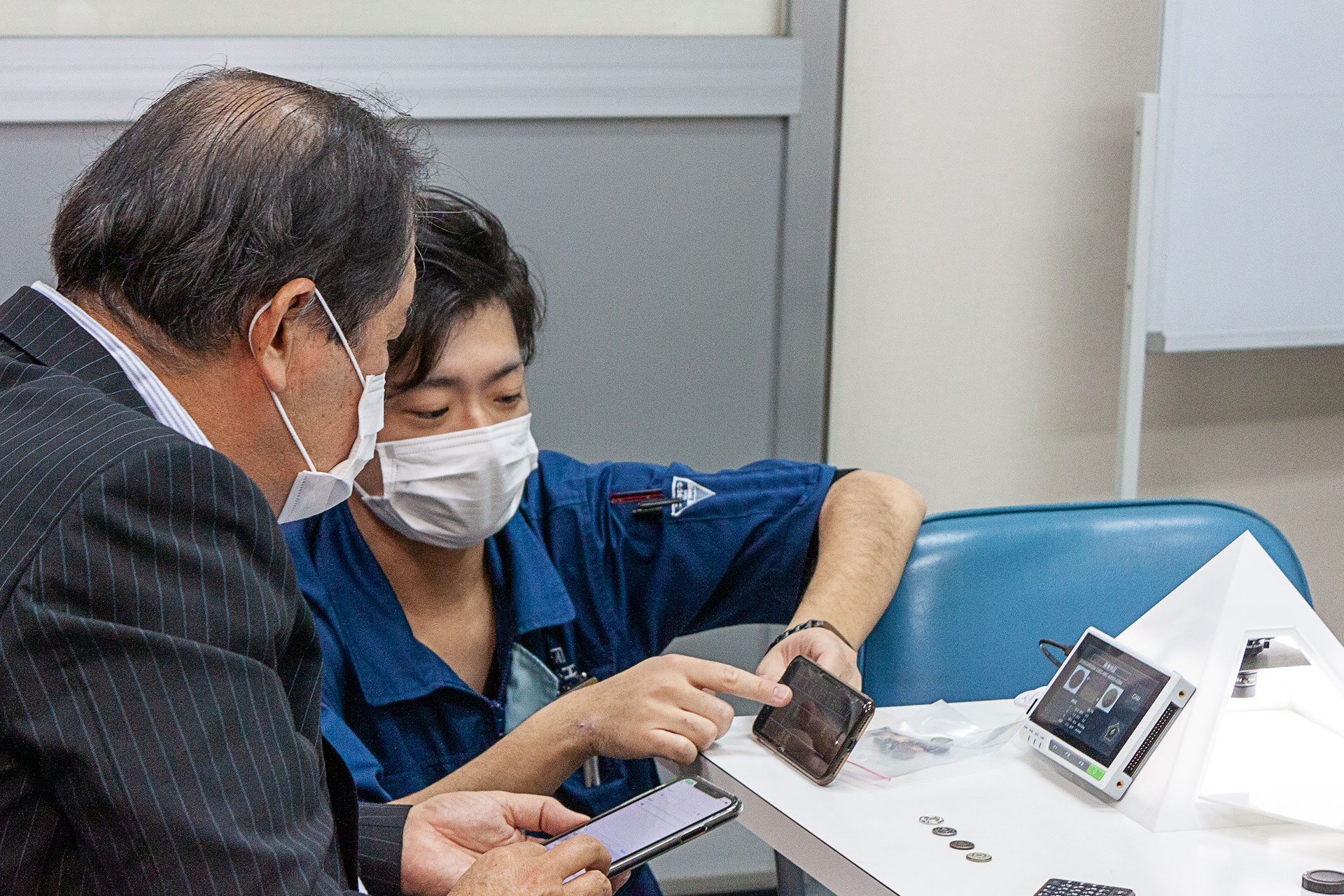
Not Lost, Easy to Search; DX Becomes a Valuable Asset
Unlike IT companies, “DX” and “IT” are difficult to penetrate in a manufacturing industry like ours. However, in my opinion, the two biggest advantages of DX are the lack of loss and the superior searchability. I think this scale is easy to visualize and effective even for those in the manufacturing industry.
Having a large number of things stored and accumulated on paper is also an asset. On the other hand, I believe that having the data you want in a ready-to-use format is an even greater asset than paper.
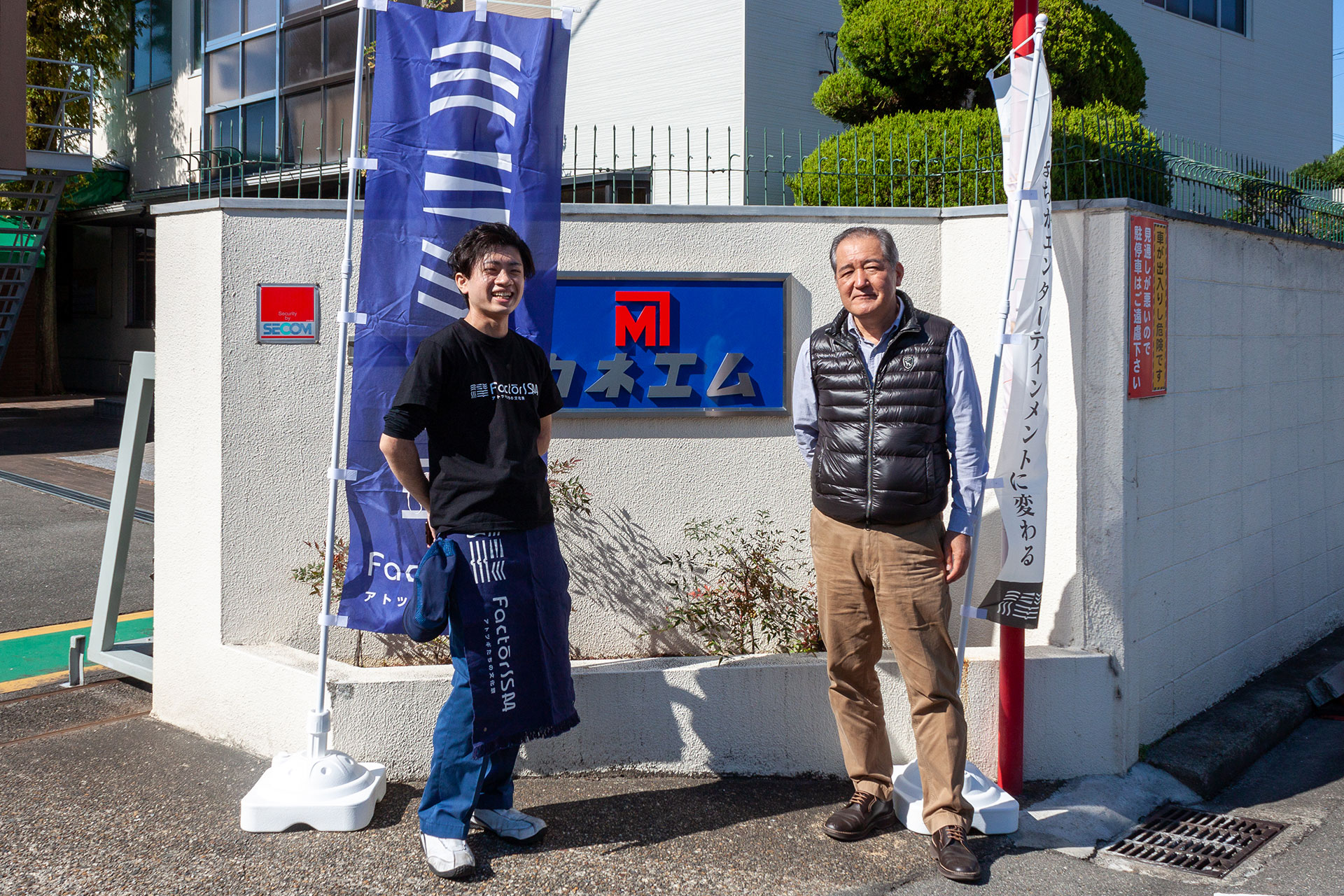
From the Person in Charge of the Project
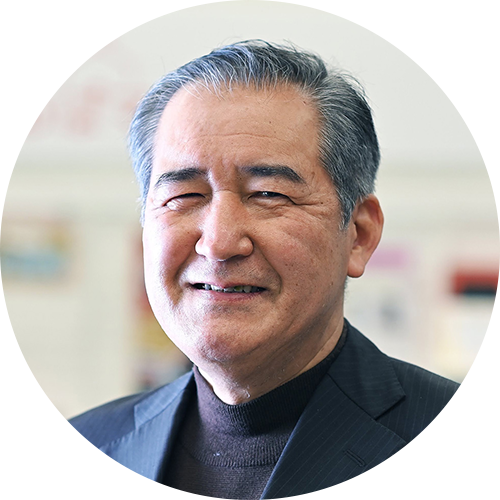
This project was about establishing the digitization of paper and real objects.
Between Kane-M Industry’s products and the end user, there is often the designer of the ordering company. For designers who pursue materials, designs, and colors from various perspectives, Kane-M Industry’s products are very attractive because of the wide variety of products and combinations. In fact, they provide many companies with excellent products.
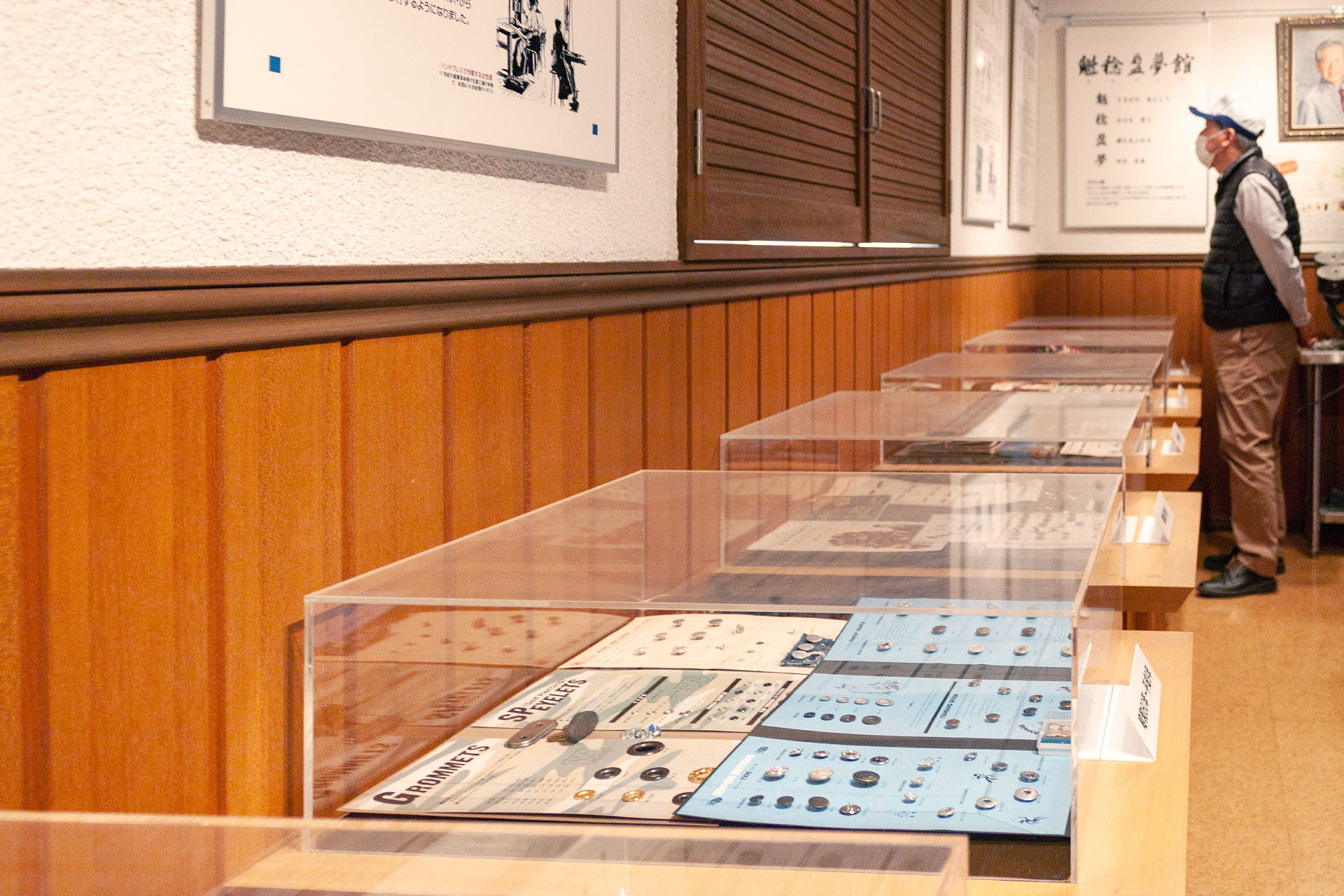
The key point is to provide a product that matches the designer’s sense of color. Digital quantification was required to ensure that the image at the time of order and the delivered product would not differ, and that the product would be stable as an industrial product.
As for the equipment, the lighting was the important point this time. The ability to take pictures under certain conditions naturally led us to the pyramid shape.

Since the search can be performed using image recognition technology, even non-experienced users can quickly learn the model number. It can also be viewed from smartphones and tablets via a linked application, so it may be used during sales meetings.
The selection of materials and technologies to be used, as well as the linkage with applications that can be used free of charge, show the flexibility that is uniquely ours.
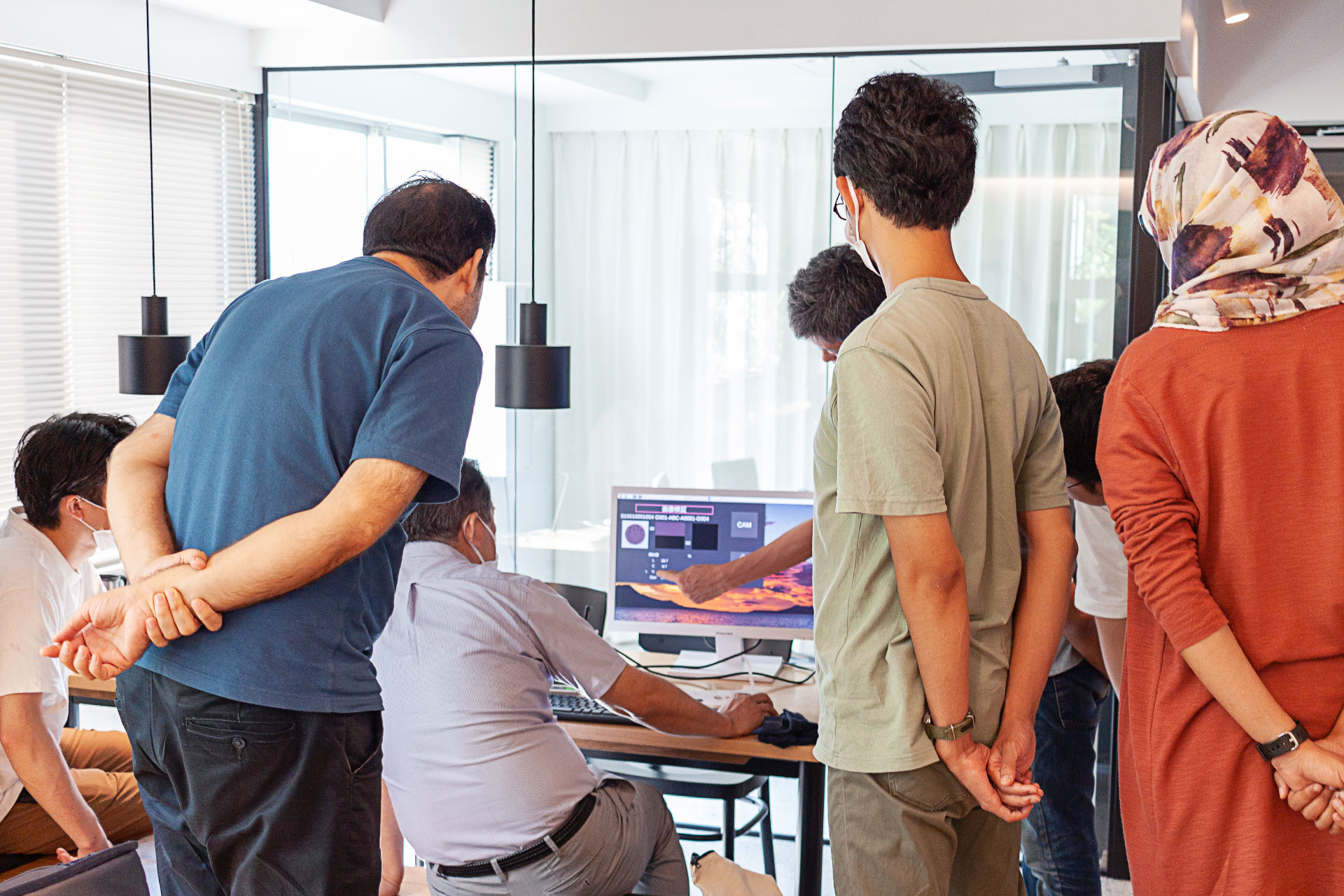
The need for reskilling has been a growing concern in recent years, and this is especially true for digital skills. Technology is expected to improve business efficiency and create innovation, and the demand for such skills is increasing regardless of industry. I personally believe that disruptive innovation should be accepted by SMEs. However, it is time-consuming, labor-intensive, and costly, and there are many barriers even if there are like-minded people in the organization. In light of this reality, I felt that the accompanying support I provide is similar to reskilling.
This system has just been delivered, and the project is still to come. We hope to continue to play a role in creating innovation at Kane-M Industry.
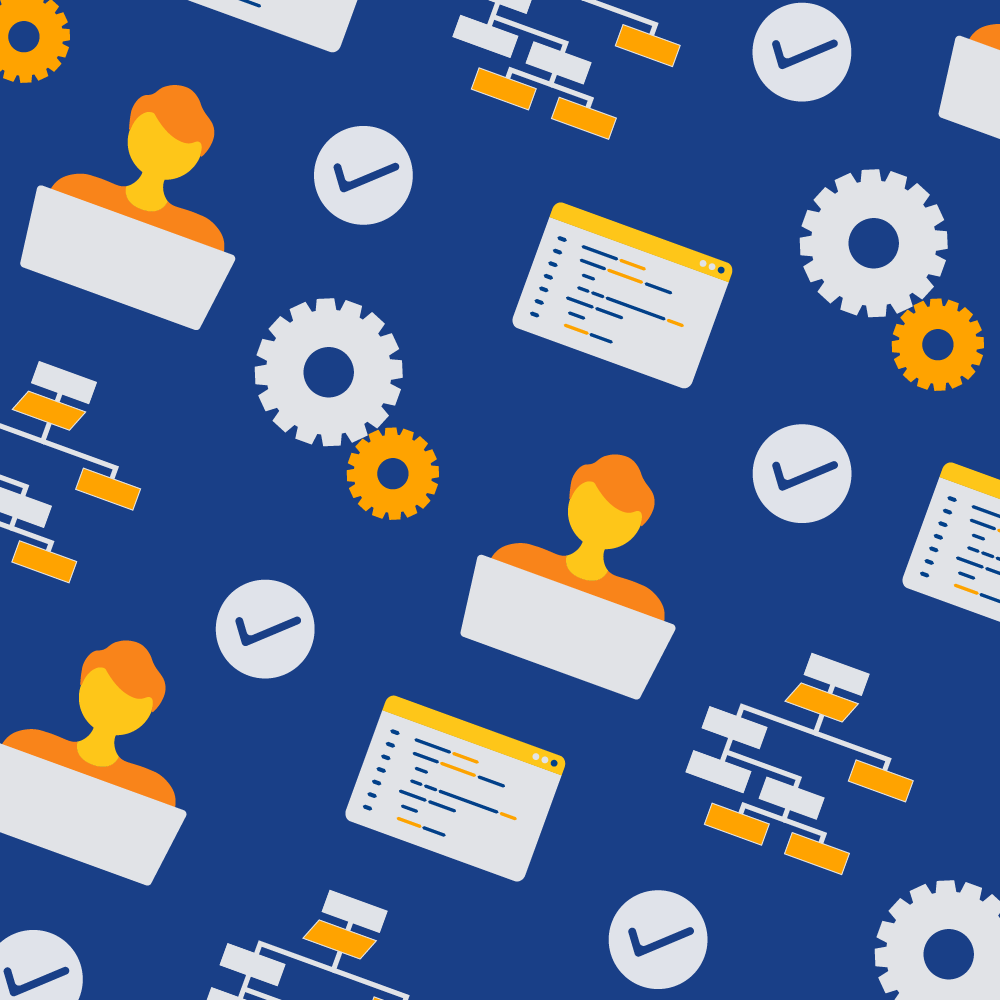
Construction and Operation Support of LMS (Learning Management System) at Kobe University
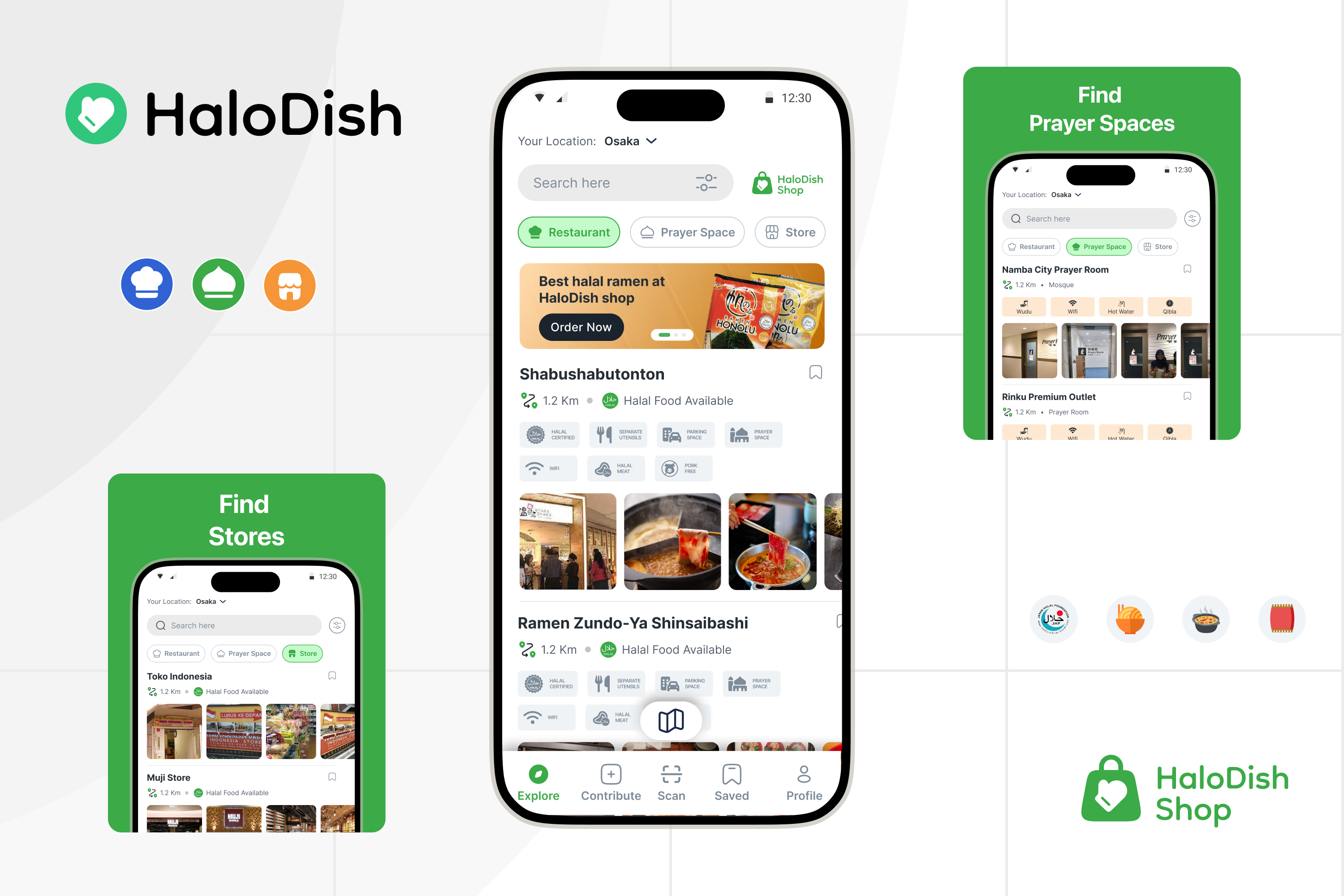
Cross-border app development: a roundtable discussion about collaboration, planning and development of halal locator app, HaloDish
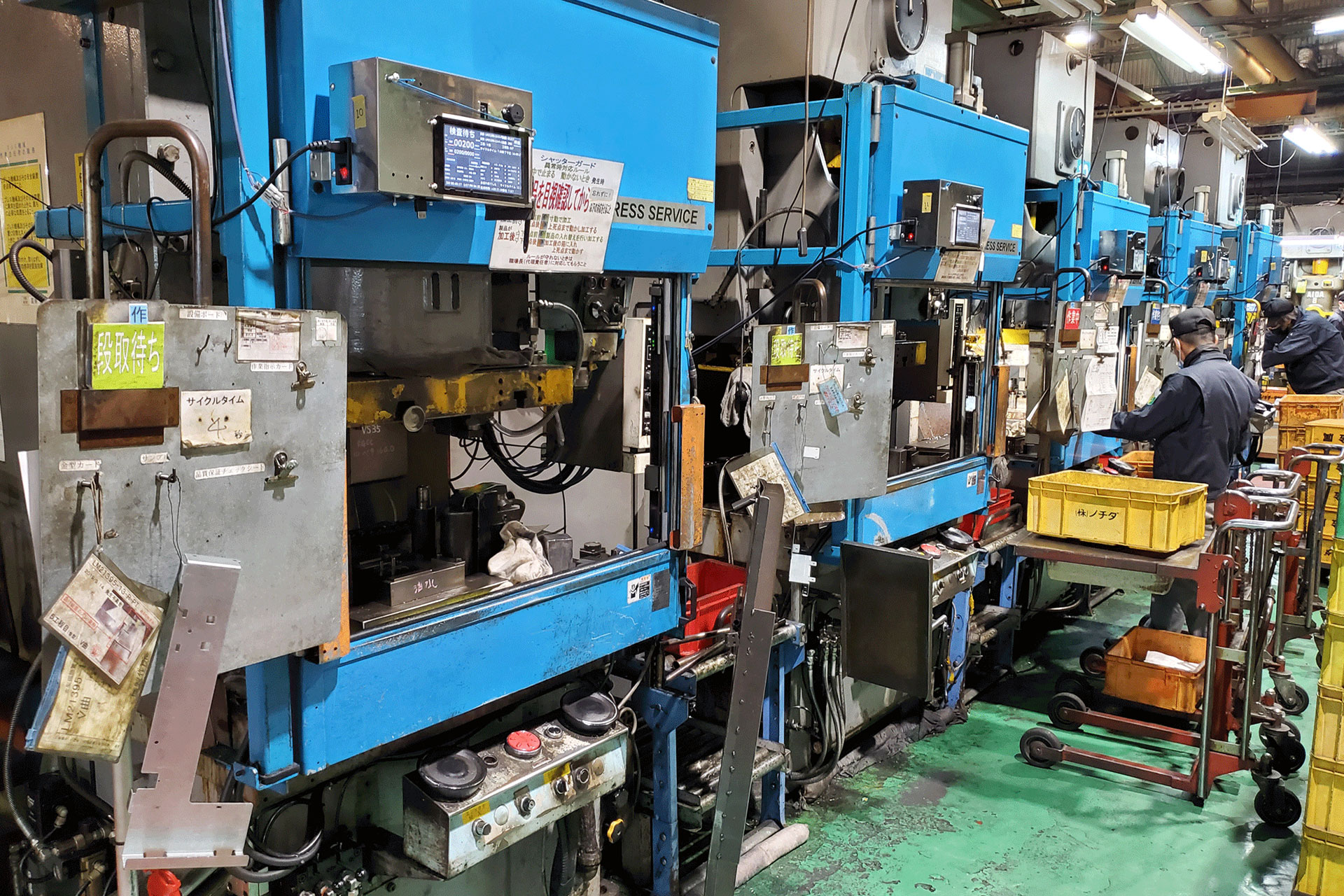