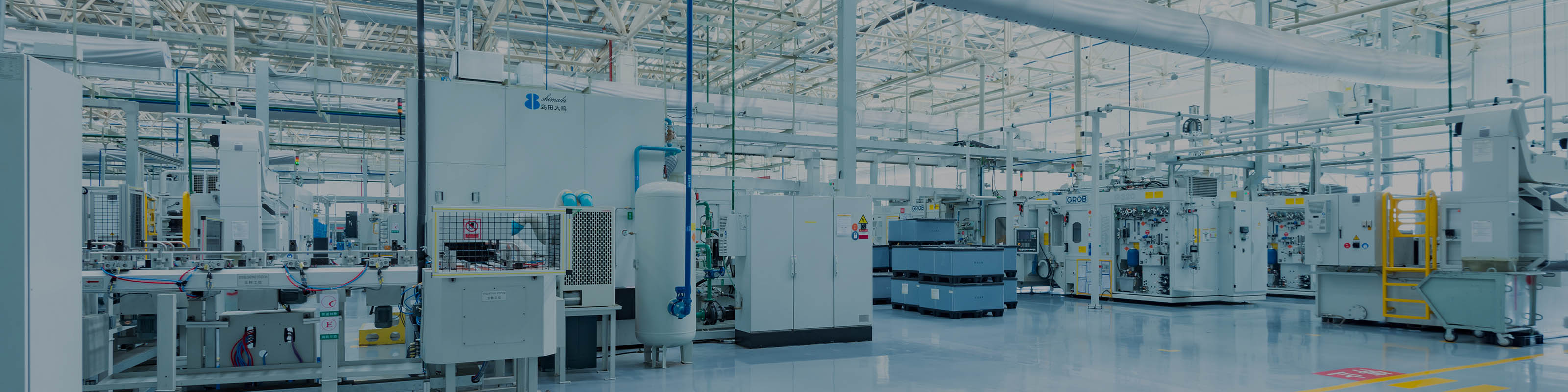
カネエム工業株式会社様におけるAI・IoT技術を活用した商品/品質管理事例
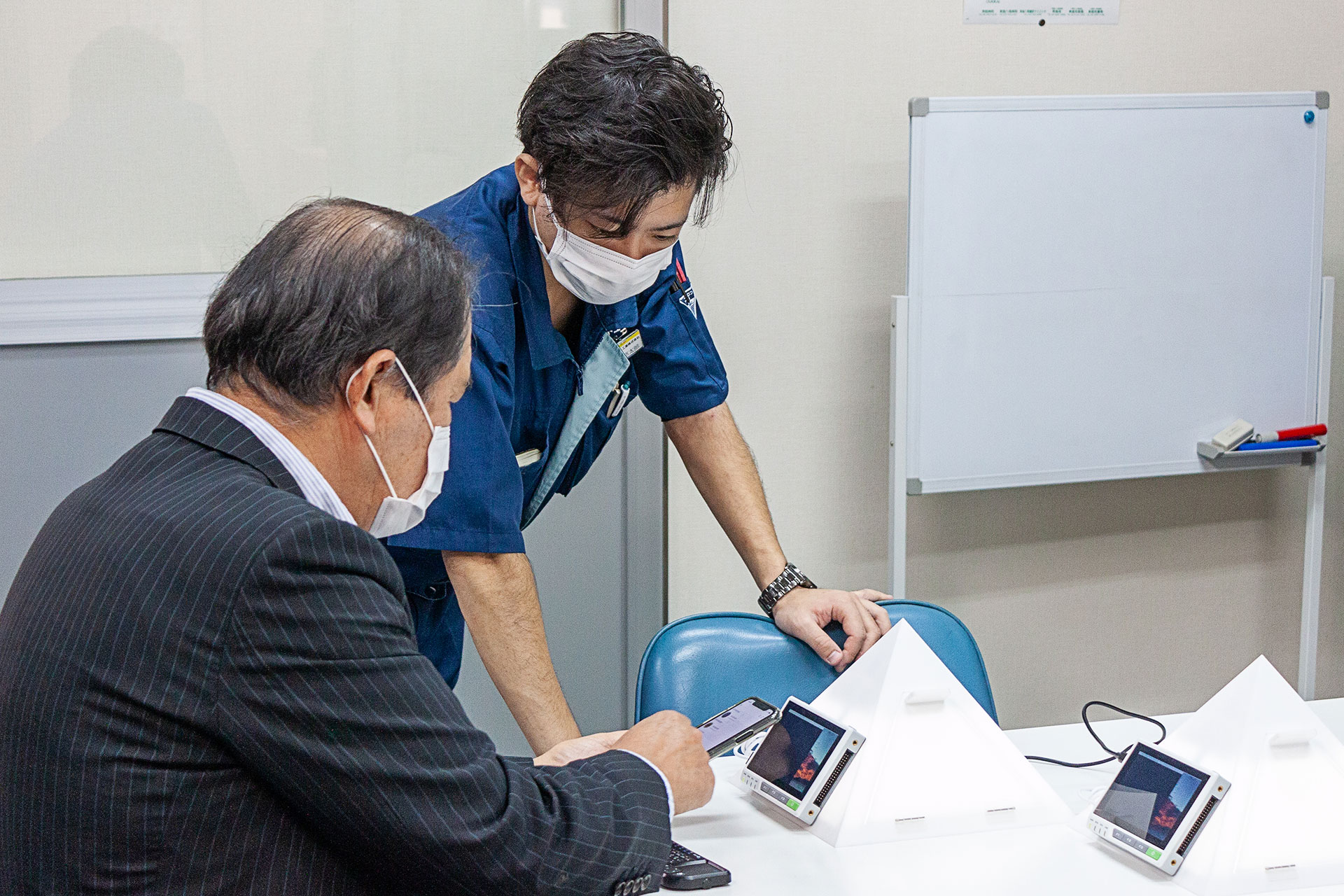
画像認識技術を活用した商品/品質管理システム開発
IoTシステムの導入目的
商品の定量的な品質管理体制の構築
弊社の担当範囲
- システムの企画・設計
- IoT機器の開発
- 既存商品のデータ移行と各種アプリケーション設定
カネエム工業株式会社 北村様の声
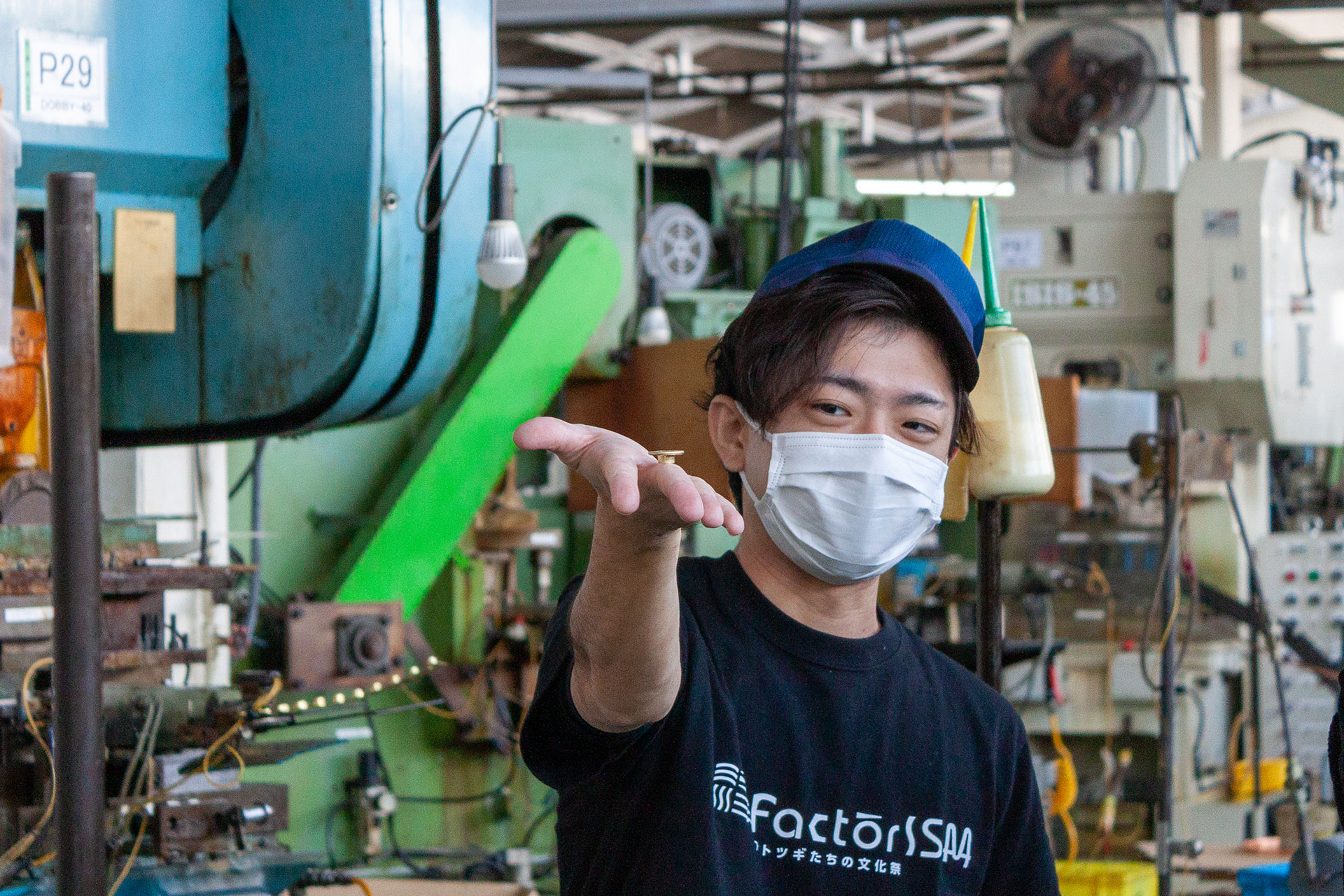
強みだからこそ、課題もあった
ニーズに応え、シーズを生み出す多様な製品と技術
カネエム工業は「パーツの未来をつくる」をキーワードに、デザインや機能性に優れたジーンズボタン、リベット、ハトメなどの製品を開発・提供している副資材メーカーです。
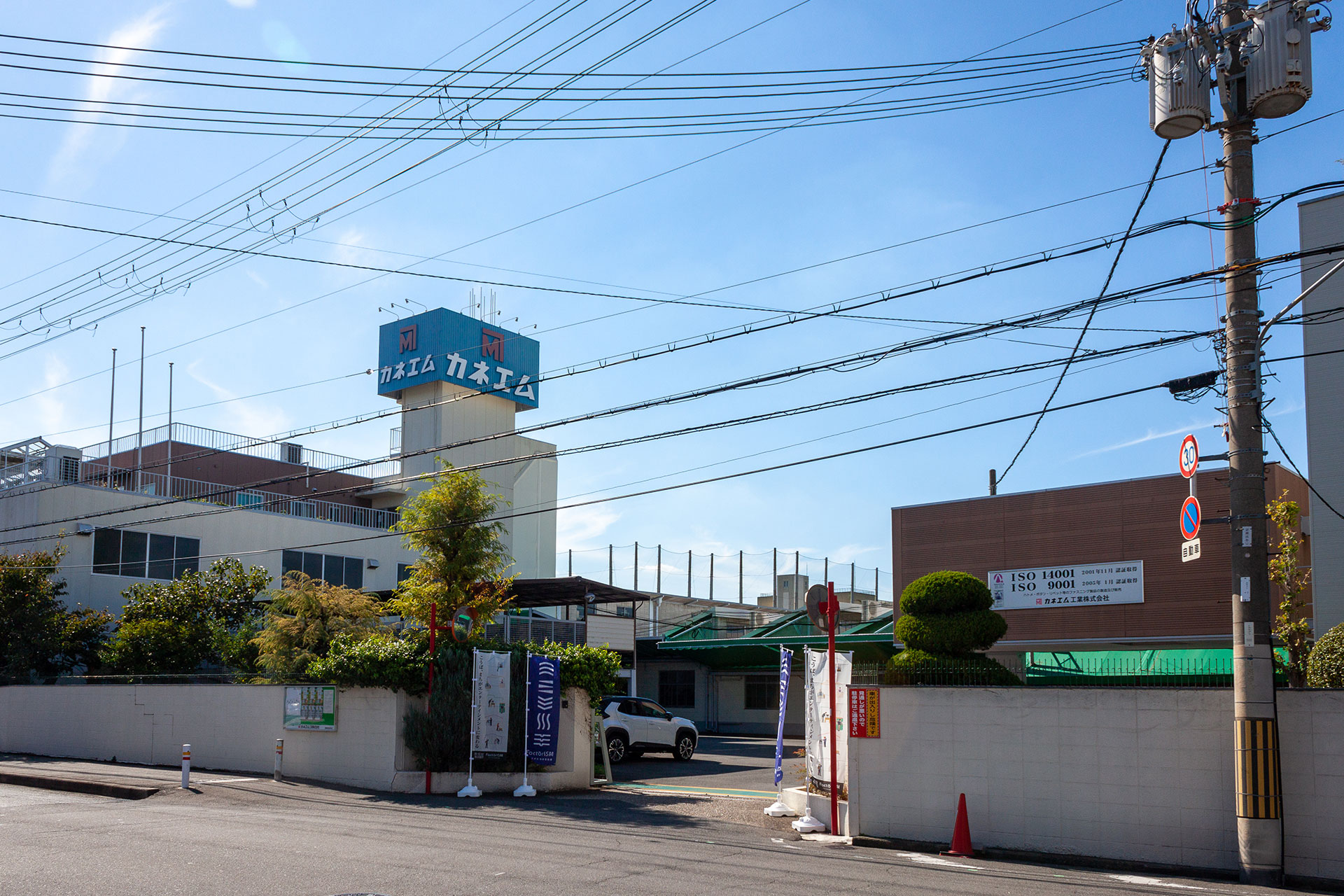
私たちの商品は、スニーカーのハトメやコートのボタンなどのアパレル製品の他、自動車のフロアーマット、建築シートなど、生活に身近なところで使われています。もしかしたら、皆様のお召し物にもカネエム工業の商品が付いているかもしれません。
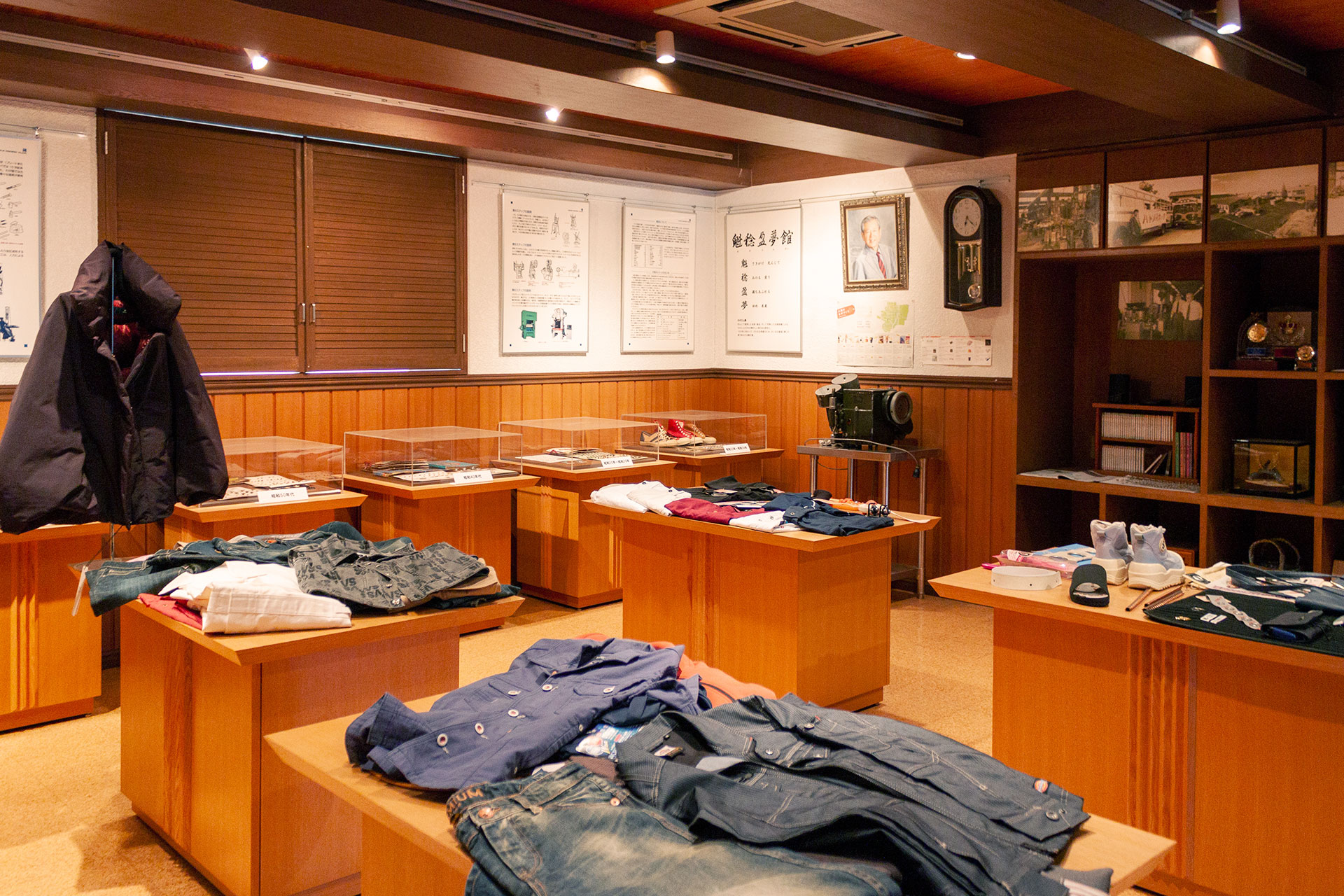
1日の生産数は、ジーンズボタンで言うと手組みでも約2〜3千個、機械なら1種類のボタンでおよそ2万5千個にも及びます。
デザインや機能にこだわりを持ったお客様が多いのは、弊社の特徴です。お客様からの幅広いニーズに応え、さらには新たな付加価値のご提案ができるよう日々励んでいます。
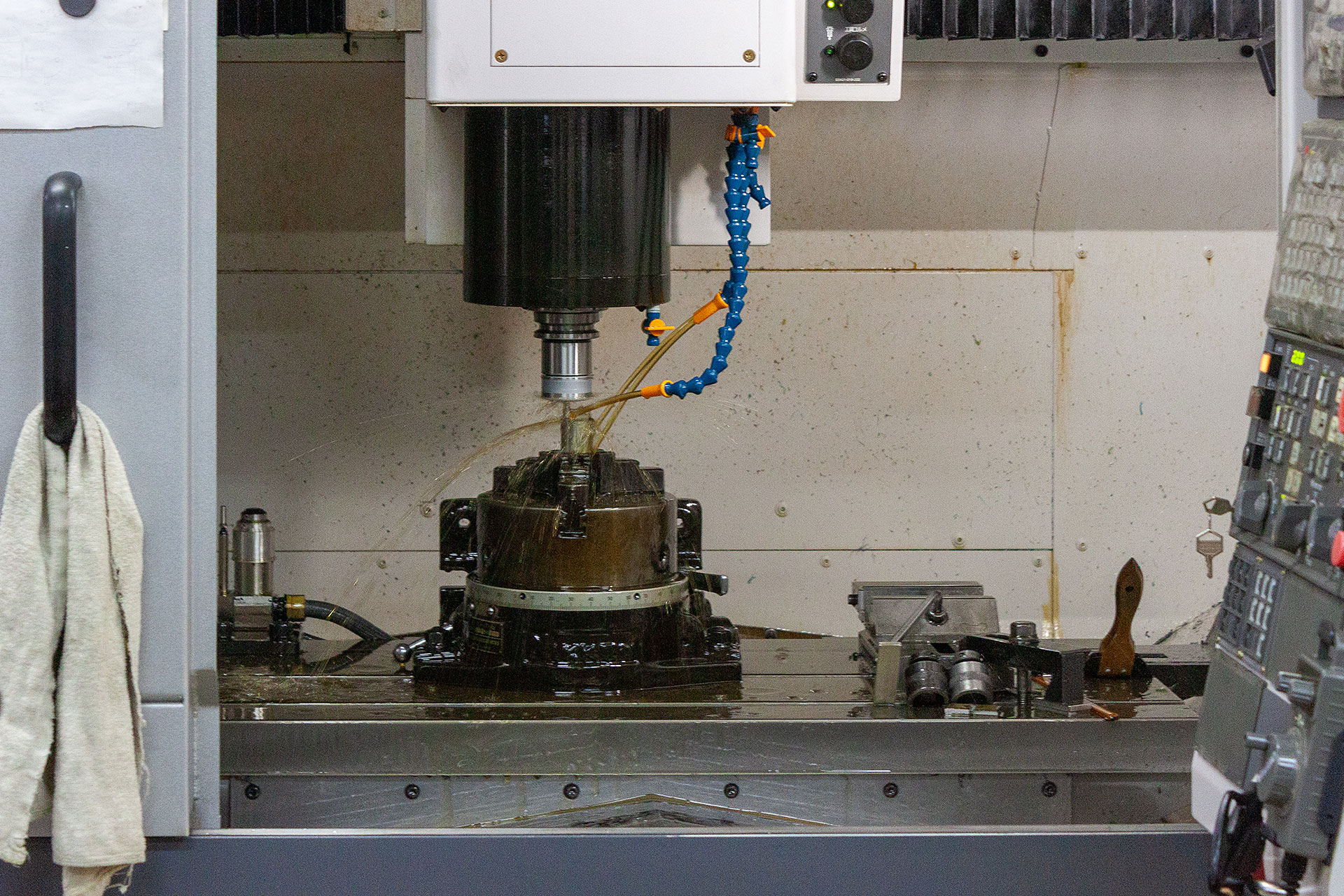
プレス加工にデザイン性を付与するなど、多様な工程の加工を掛け合わせてオリジナル性の高い製品を一貫生産できるのは、当社ならではの強みだと思っています。6種の材質、400種の商品、200種の色を掛け合わせることで生まれるデザインは無限大です。1日に2〜3個は新しいデザインが生まれていますね。
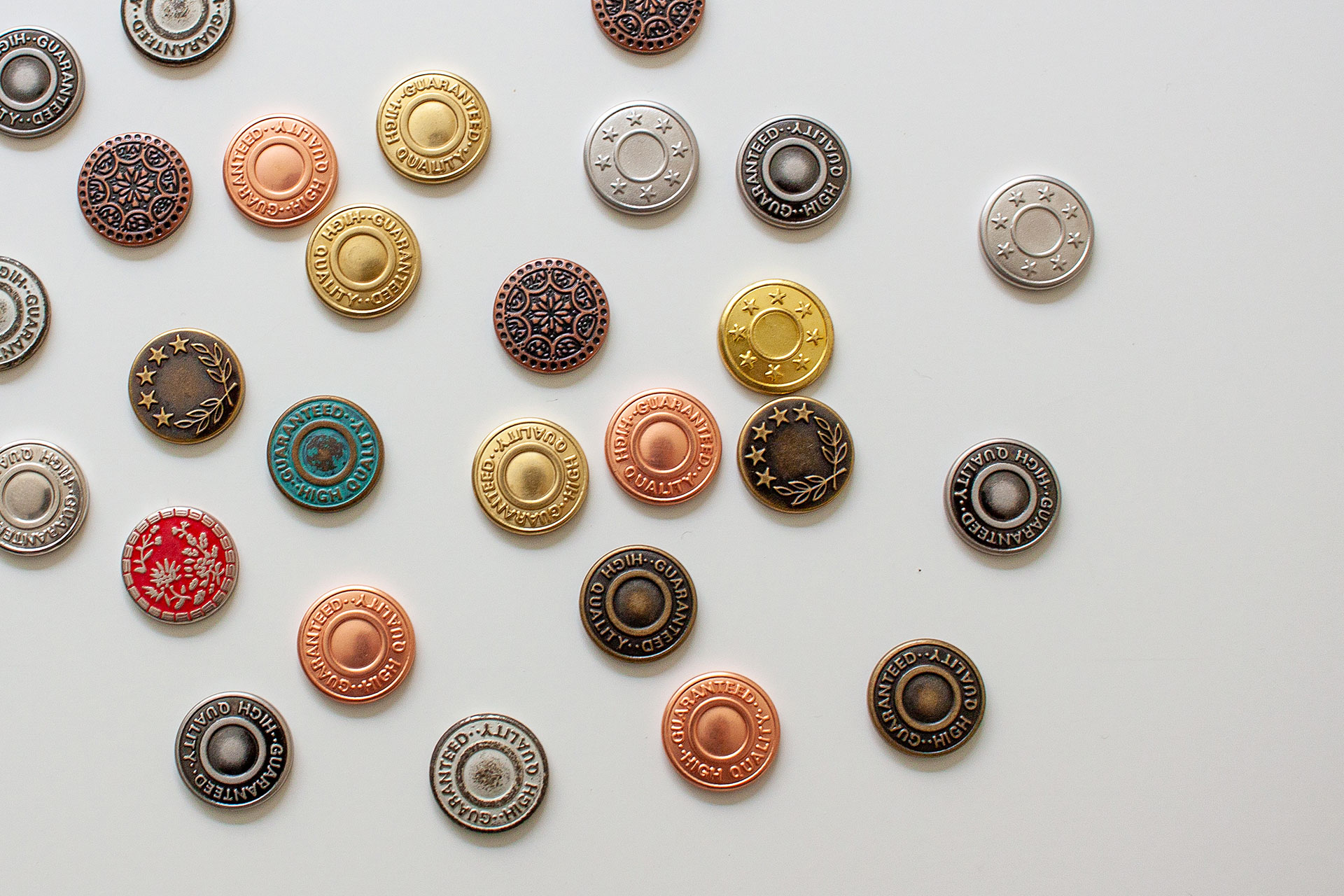
しかし実は、多種多様なニーズに応えられるからこその課題も見えていました。それを解決する手立てとなったのが、今回のシステム開発だったのです。
水掛け論に終止符を。色を定量化し、共通言語に
当社では電解メッキは自社ではなく協力業者さんに依頼しているのですが、メッキの色がブレることがあるんです。
例えば、このP-HBKという色は光沢のある黒味がかった感じですよね。当社としては「この色」に仕上げていただかないとなりませんが、仕上がった納品物を見ると色合いが異なることがあります。これって、メッキ屋さんとのやりとりの中で結構問題になりがちなんです。
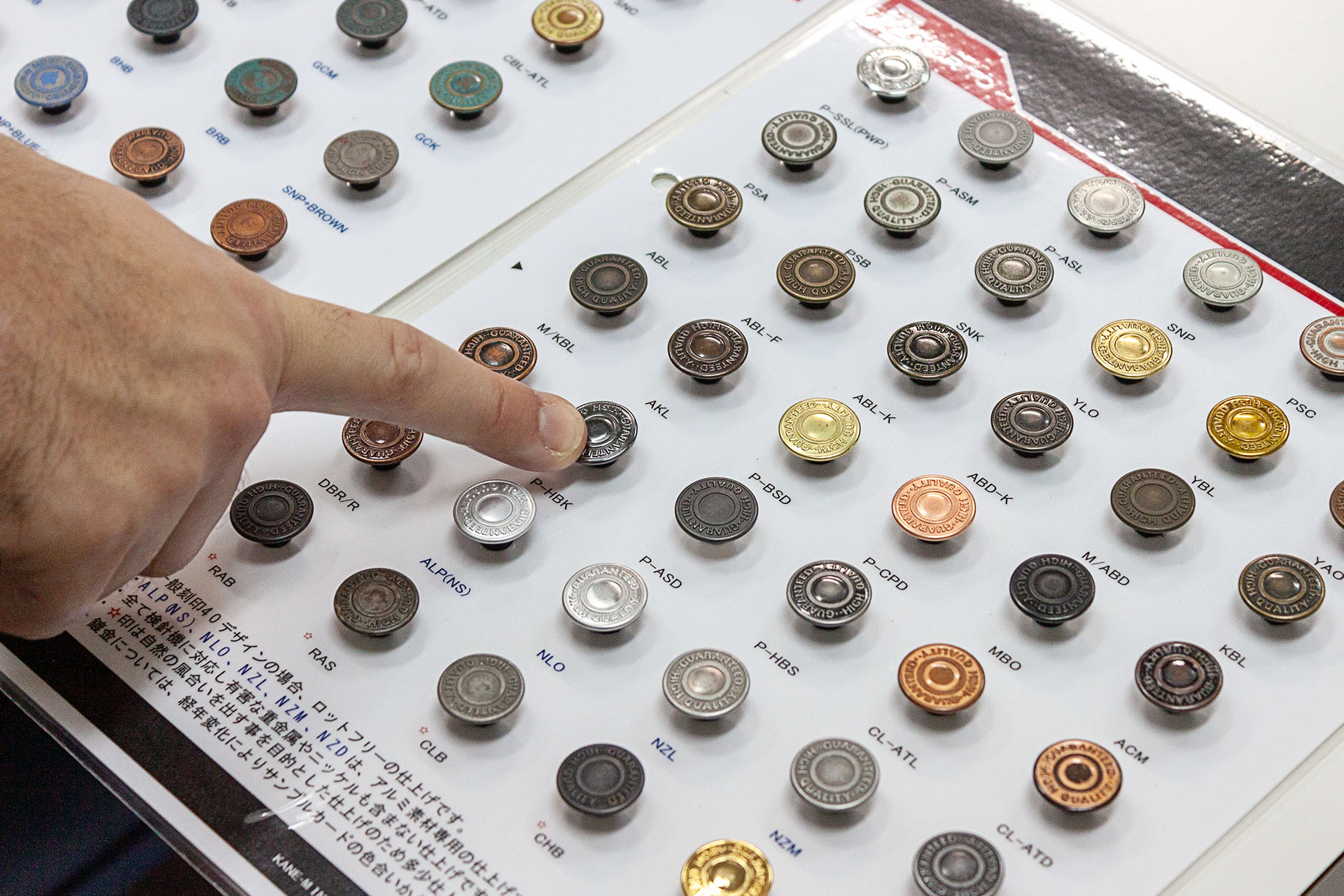
色を定量的に捉えることができなければ、「何をもって黒いんですか?」と水掛け論みたいになってしまいますよね。
メッキ屋さんに対してだけではなく、社内に対しても同じことが言えます。苛性ソーダなどの薬品を使用したアンティーク色を中心とした加工は、カネエム工業で行っているんです。
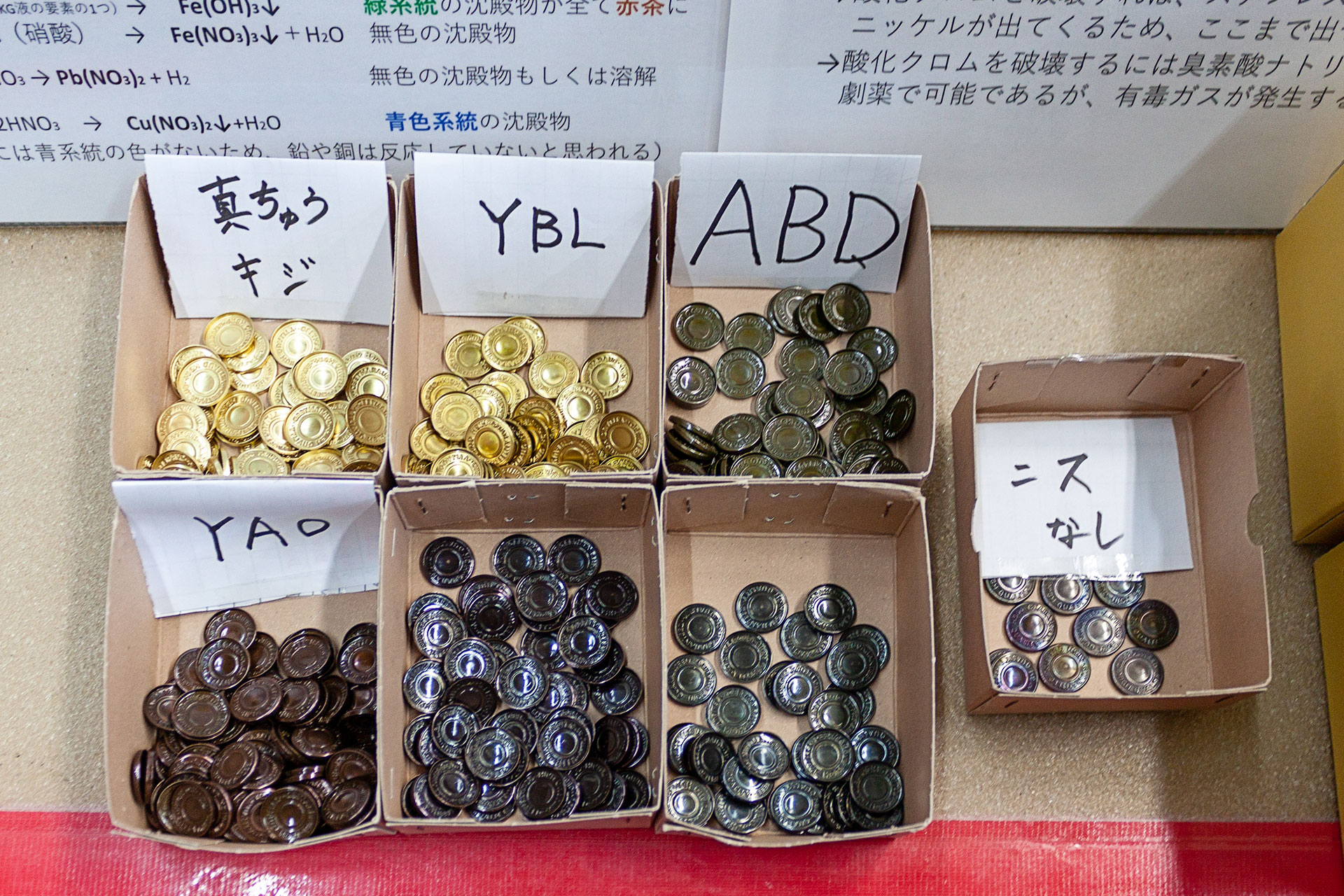
色を定量化できれば、見本と仕上がった実物を見比べながら「どうでっか」ではなく、例えば弊社の基準として92%以上近似していたらOK、それを下回ったら「この色じゃない」と提示しましょうと取り扱いができます。
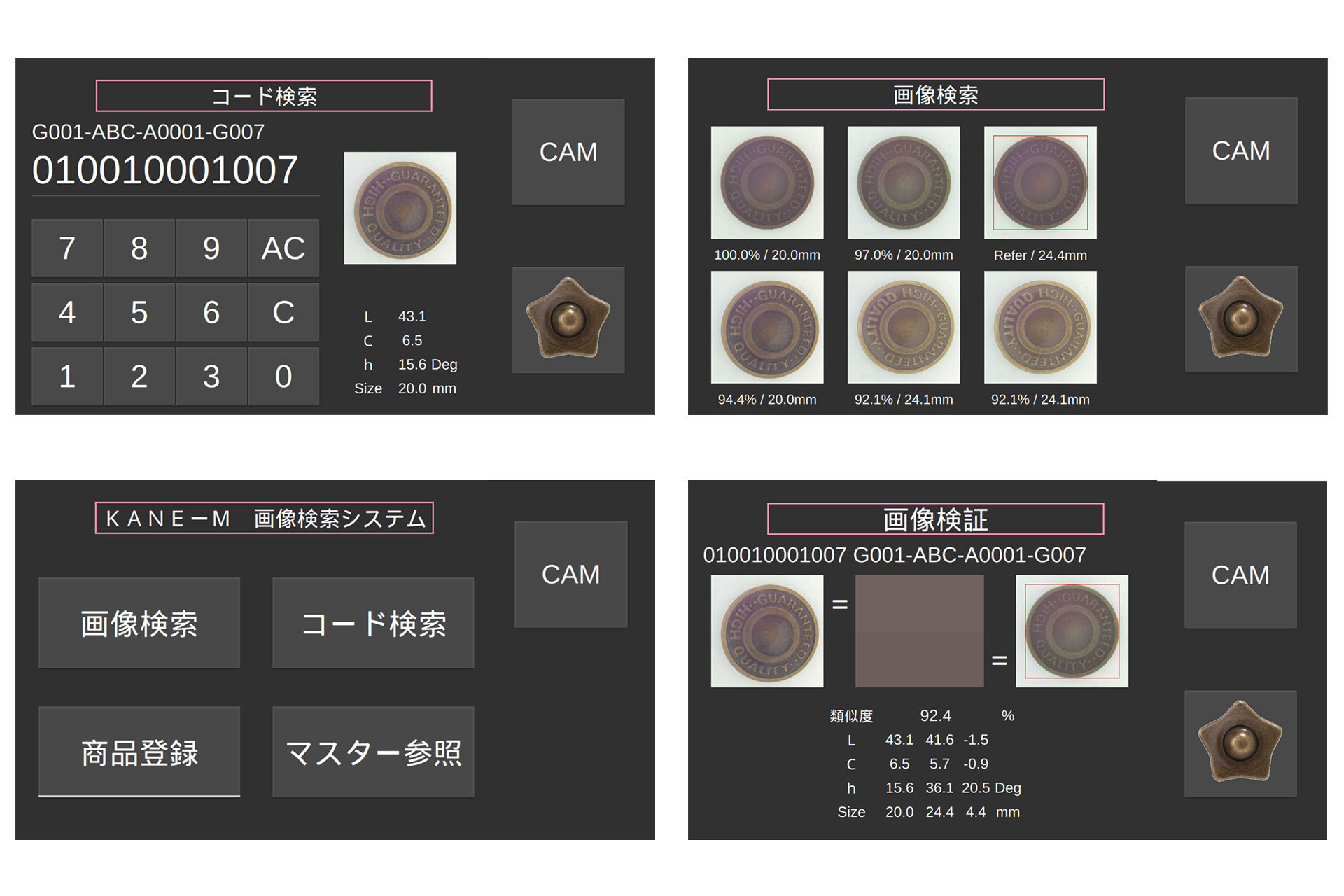
色に関する課題はこうした指標だけではありません。
金属にメッキや化学着色などで色を着けているので、経年により酸化して黒ずんでくるんです。見本帳で商品を管理していても、果たして「この見本帳を作った日付がいつなのか」という問題が出てきます。例えば、できたてのYBLの色は、厳密にはこの見本帳よりもうちょっとだけ明るいんです。
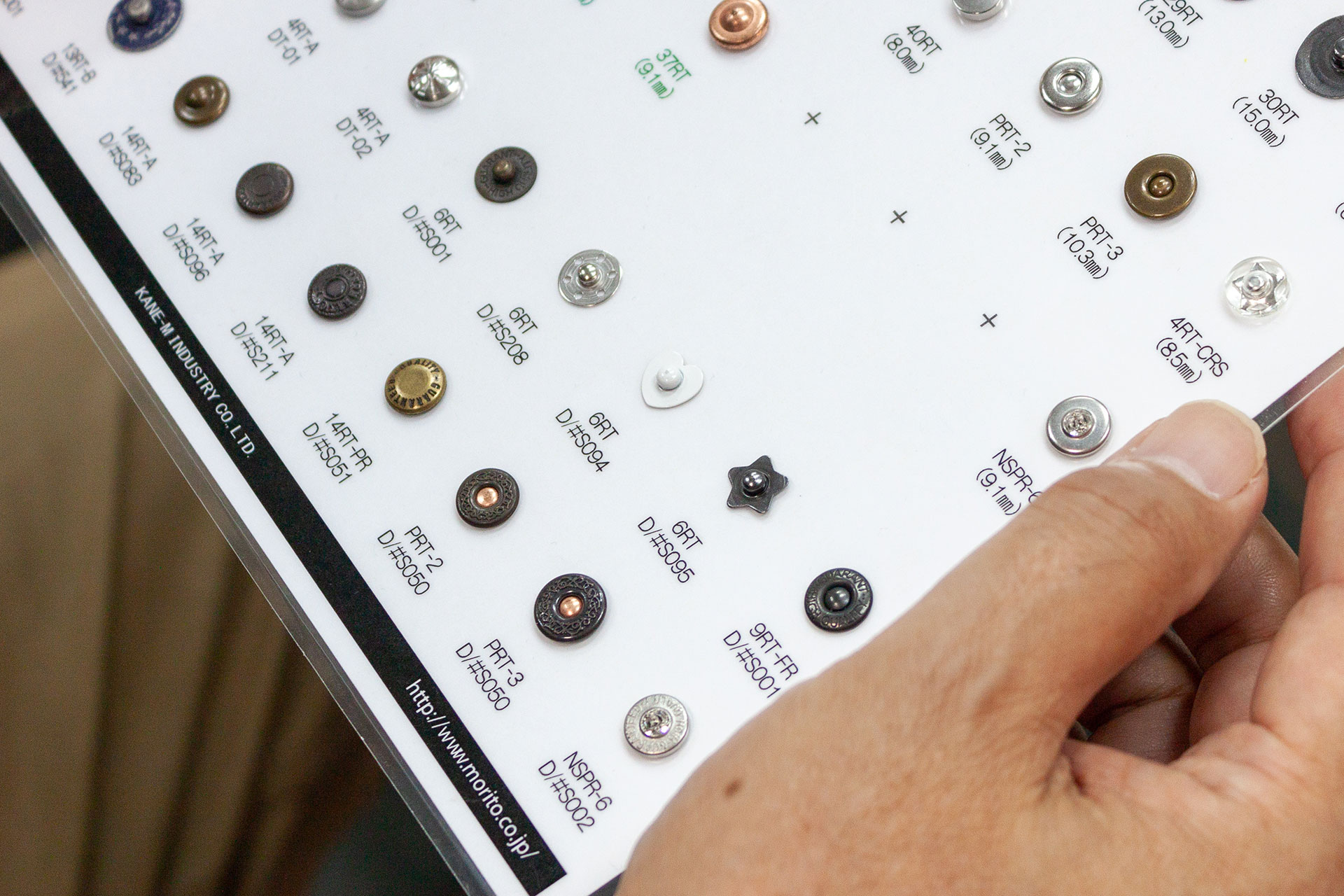
実物サンプルの見本帳は経年劣化していくので、同じ環境で撮影した画像をデータとして残せるのがベストです。当社でも写真撮影などに取り組んではいたのですが、やはり撮影環境がまちまちだったりして、画像と実物とが全然違うといった問題がありました。
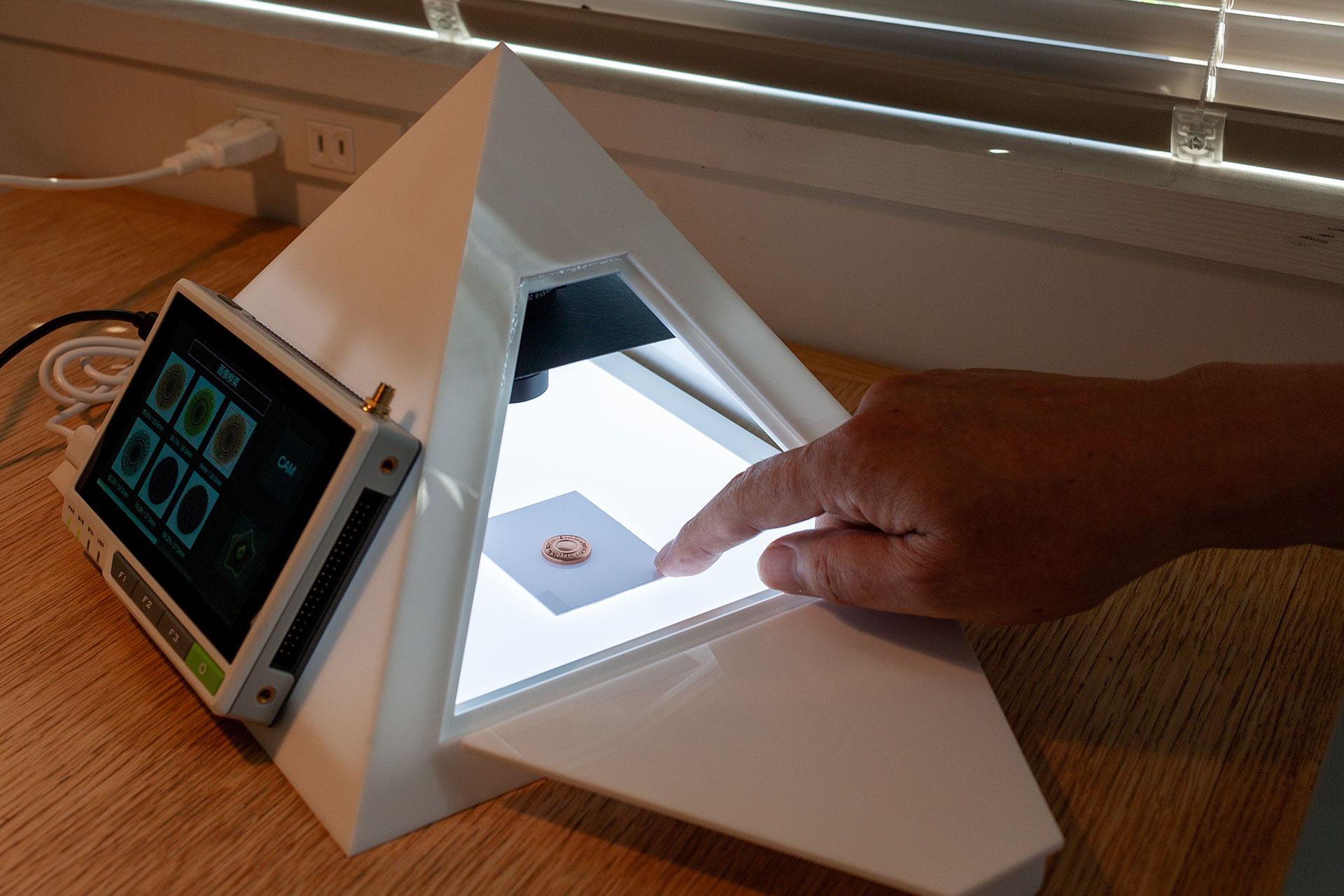
だから「人間の感覚ではなく、定量的に色を見るものが欲しいなぁ」とは、ずっと思っていたんです。当社で既に試みた時期が5、6年前にあり、その時は難しく実現できなかったと聞いています。
そんな課題を抱えながら、「新しいシステムを導入したいなぁ」と僕が視察に訪れたのがみせるばやおで開催されていたDXフォーラムです。
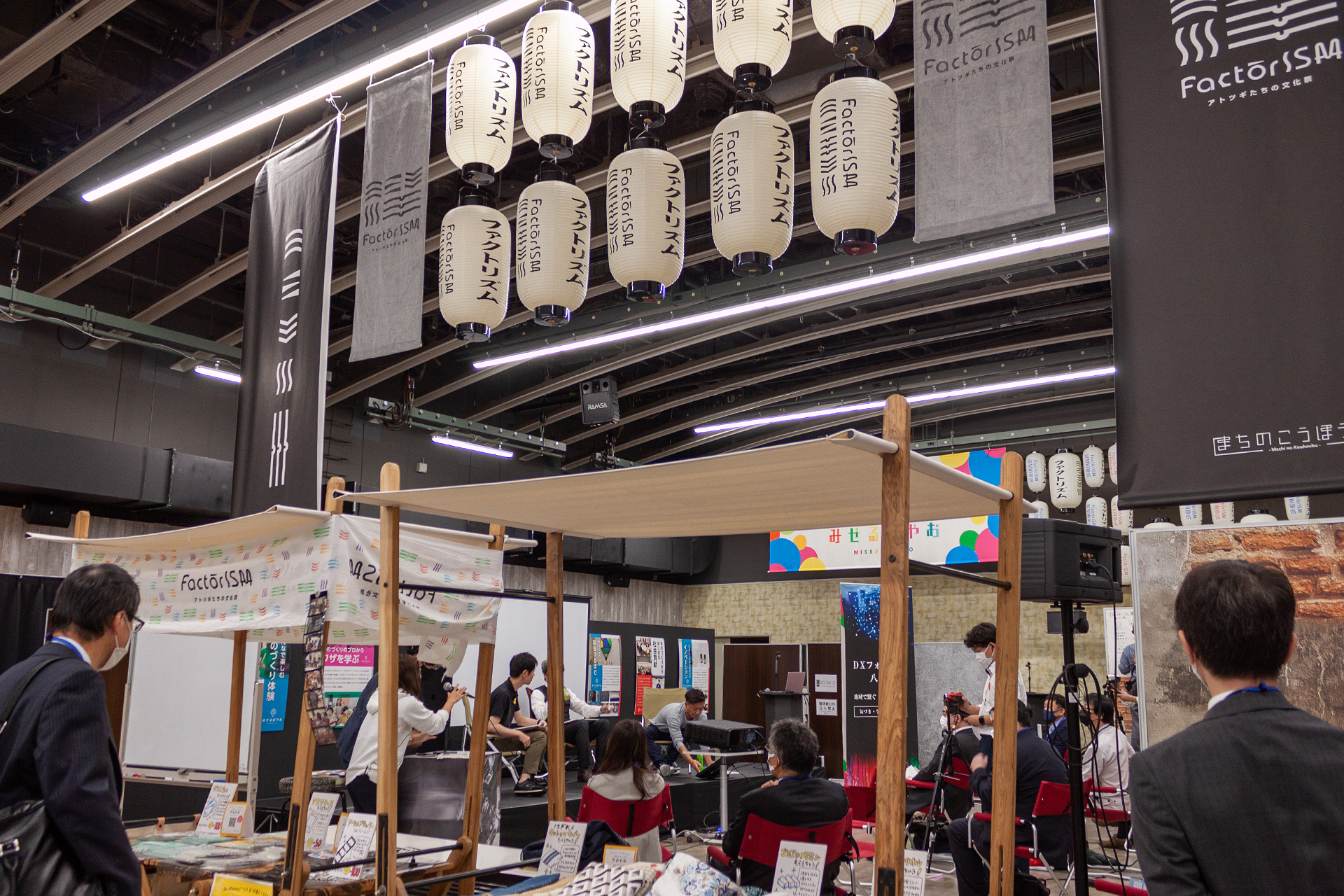
「アベルブラック」でお馴染みのアベルさんのブースで、品質管理画像システムをeftaxの小林さんがデモンストレーションしていました。
そこで、「うちにはこういう課題があるんやけども、解決できるもの作れませんかねぇ」と相談させてもらったのが、このプロジェクトの始まりです。もう一年も前のことになりますね。
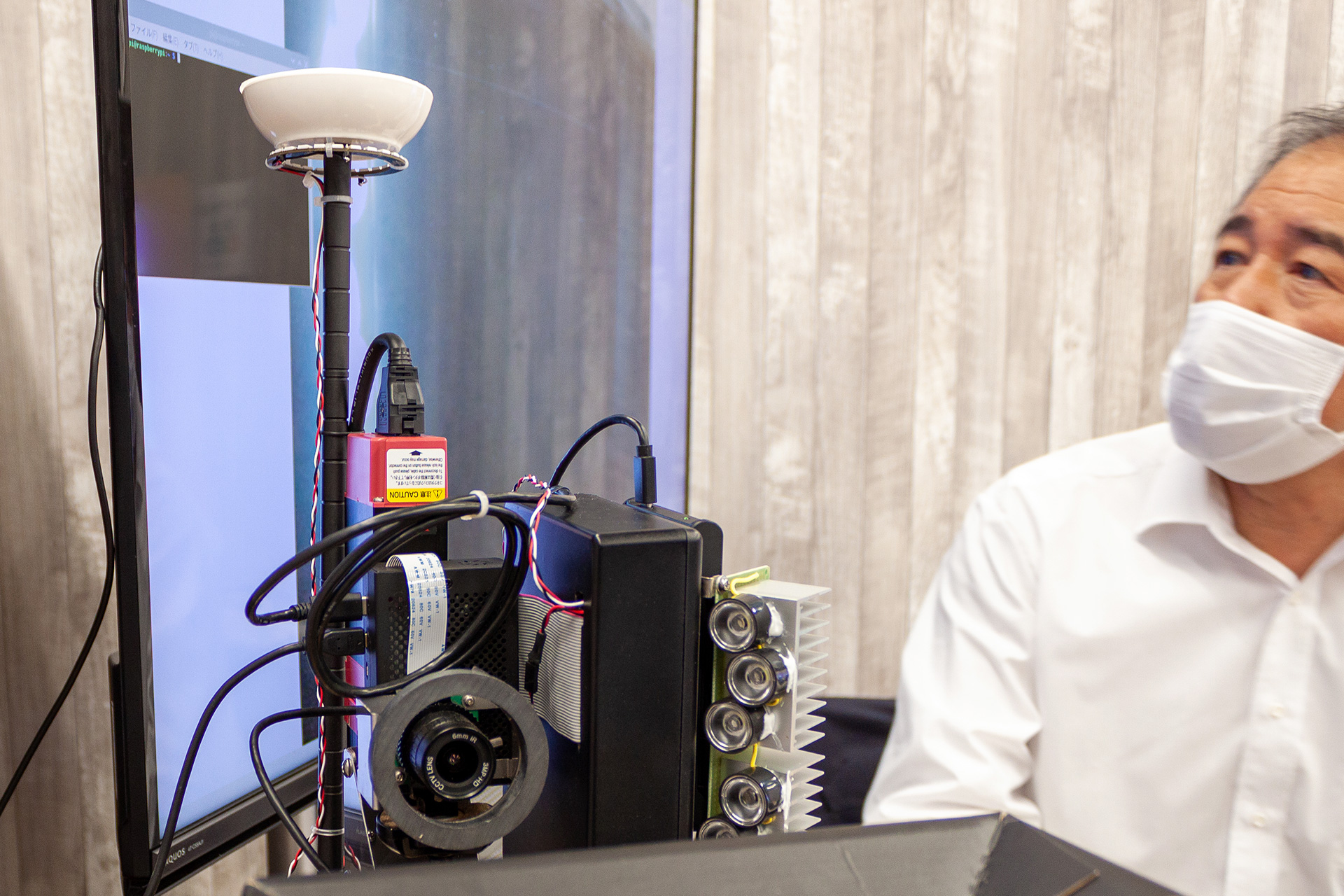
デザインを判別し、人に依存しない検査体制を構築
ここまで話してきた通り、「色を定量的に判断したい」というのが話の発端だったわけですが、それができるのなら加えてやりたいことがもう一つありました。それは、「デザインの違いを見分けること」です。
当社では様々なお客様から、様々なデザインのパーツをご注文いただきます。そこで、あってはならないのが、ブランド名が入ったパーツを別のお客様へ誤納品してしまうことです。基本的にはないことですが人間が動かしている以上、ヒューマンエラーというのはゼロではありません。それをもなんとか抑えられるシステムが、色の定量判断と併せて実現できるのなら一番いいなと思いました。
どうせ写真を撮って色を判断するんだったら、同じ写真でデザインも判別できたらなという発想ですね。当社では検査においても様々な機械を導入していますが、デザインの部分はこれまで人が見比べることしかできませんでした。
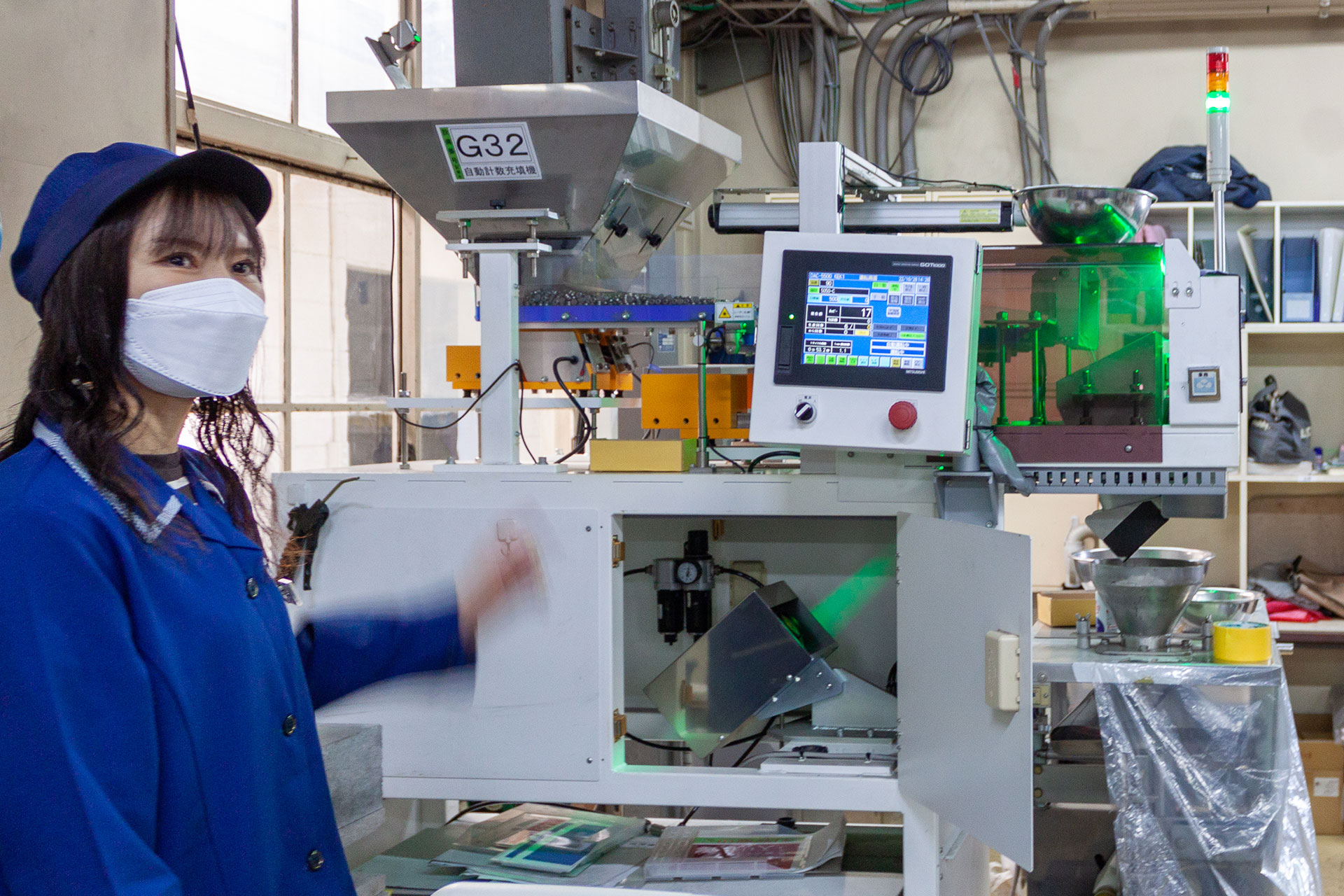
デザインの判別というのは、意匠の違いだけではありません。刻印の濃さ/浅さをどこまで許容するか等も、数値化できれば当社としての正解を保存して判断ができます。
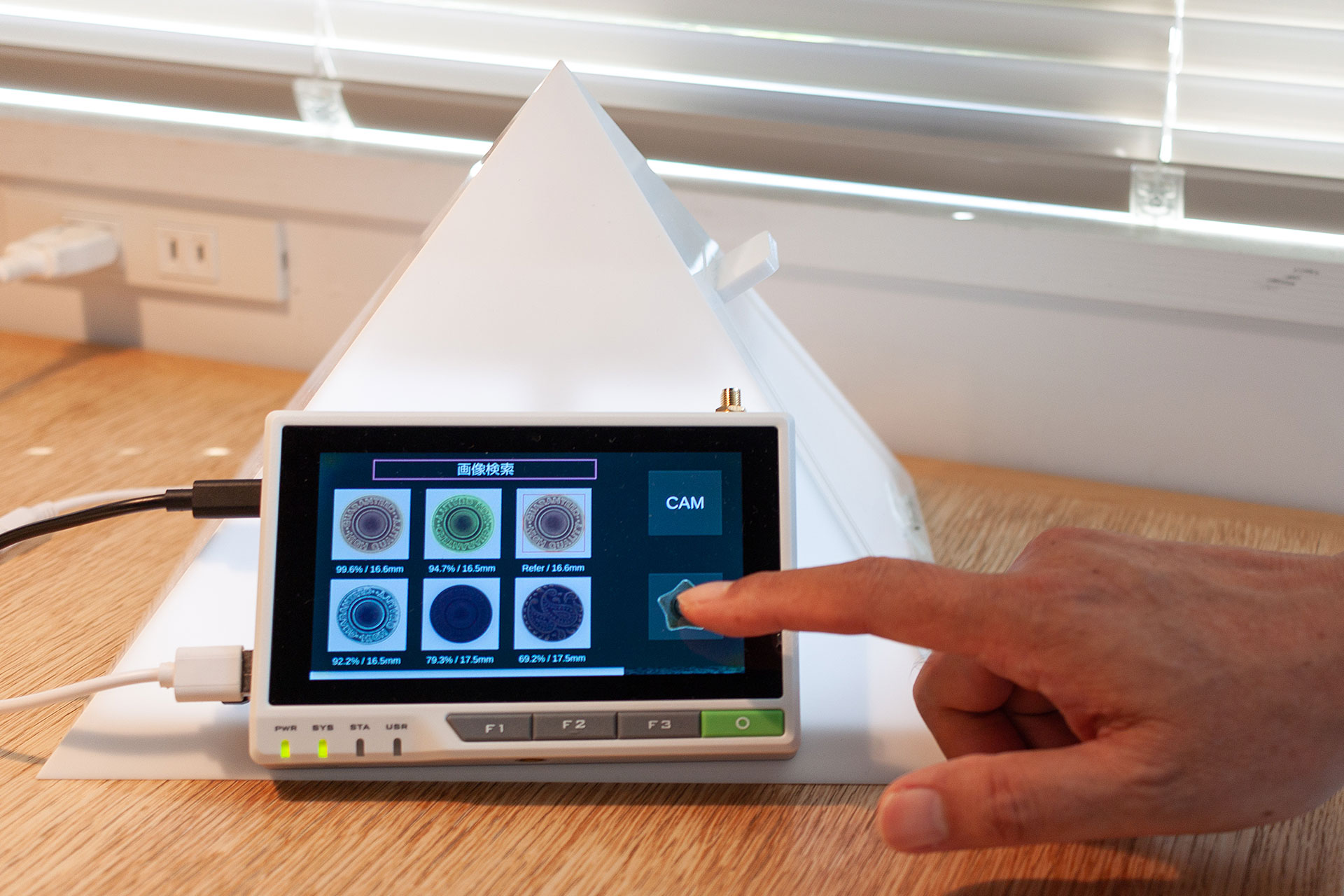
色を定量的に判断する。デザインを判別できる。尚且つ、流れる業務の中で使いやすいシステムであることが望ましい。こういった観点で、eftax小林さんにご相談させてもらいました。
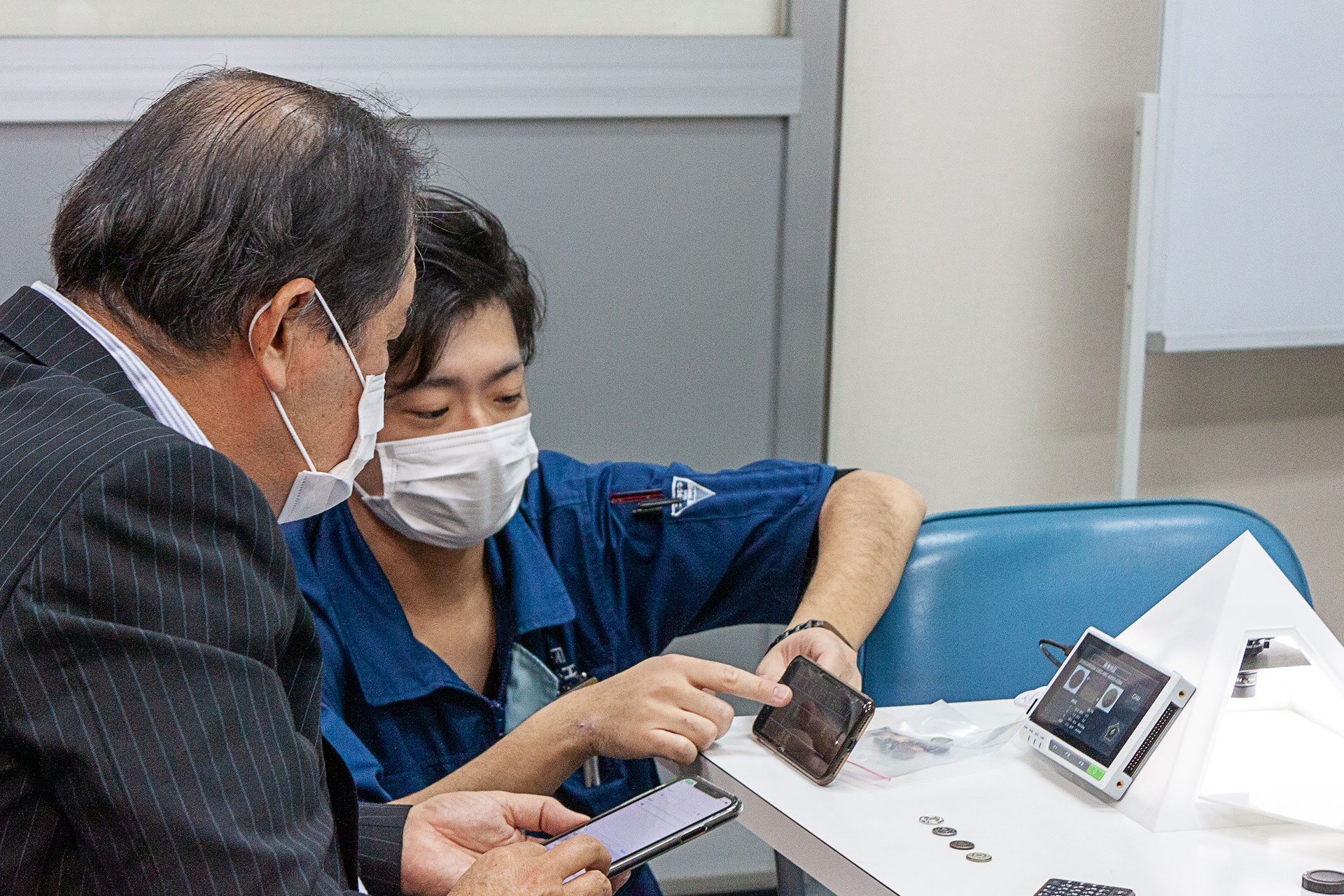
紛失がない、優れた検索性。DXは大きな資産に
IT系企業とは違って、うちみたいな製造業では「DX」とか「IT」とかってなかなか浸透しにくいところがあります。ただ、DXする最大のメリットと僕が思っているのが、紛失がない、検索性に優れている、この二つです。この尺度なら製造業の方でもイメージしやすく、効果も大きいのではないでしょうか。
紙で保管・蓄積してきたものがドーンとあるのも資産です。しかし、欲しいデータがすぐに出せる状態に有るというのは、紙以上の資産になるんじゃないかと思っています。
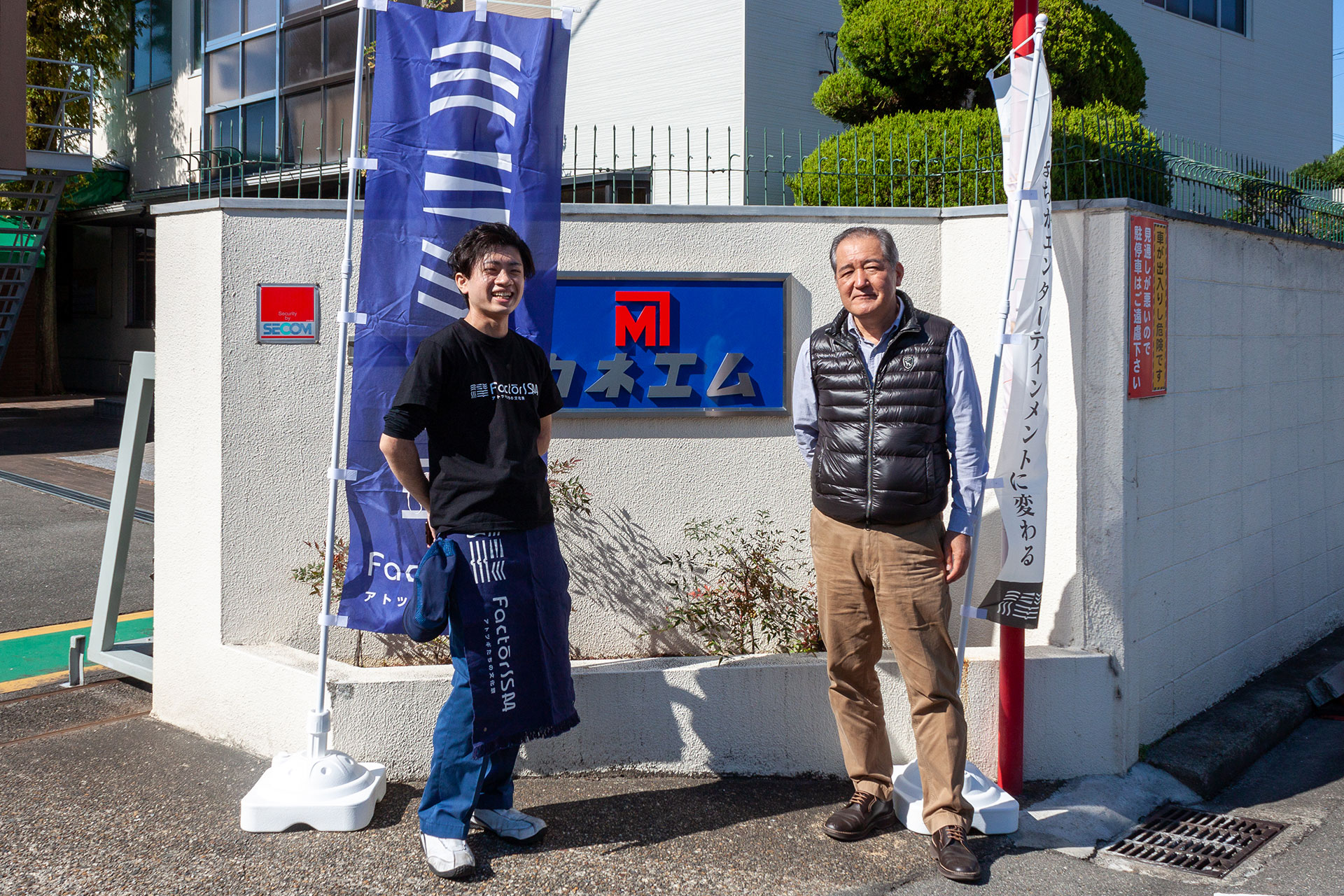
弊社担当者より
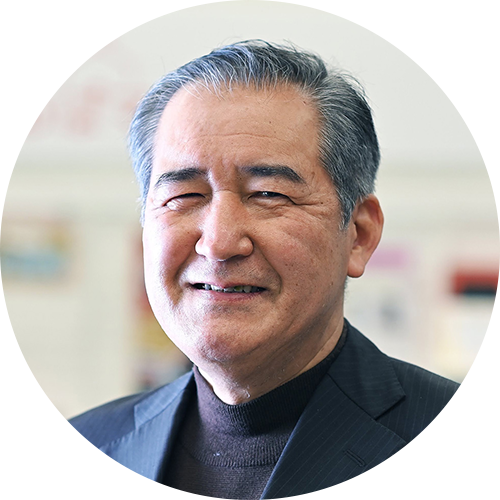
今回のプロジェクトは、紙や実物のデジタル化を確立したいというお話でした。
カネエム工業様のご提供される製品は、エンドユーザーまでの間に発注元企業のデザイナーさんがいるケースが多くあります。材質、デザイン、色など、様々な観点で追求するデザイナーさんにとって、多品種で組み合わせ多様なカネエム工業様の製品は大変魅力的であり、事実多くの企業様に優れた製品を提供しておられます。
そこでポイントになるのが、デザイナーさんの色感覚に合ったものを提供することです。発注時のイメージと納品物に差異のない、工業生産品として安定した物にするためにデジタル定量化が求められていました。
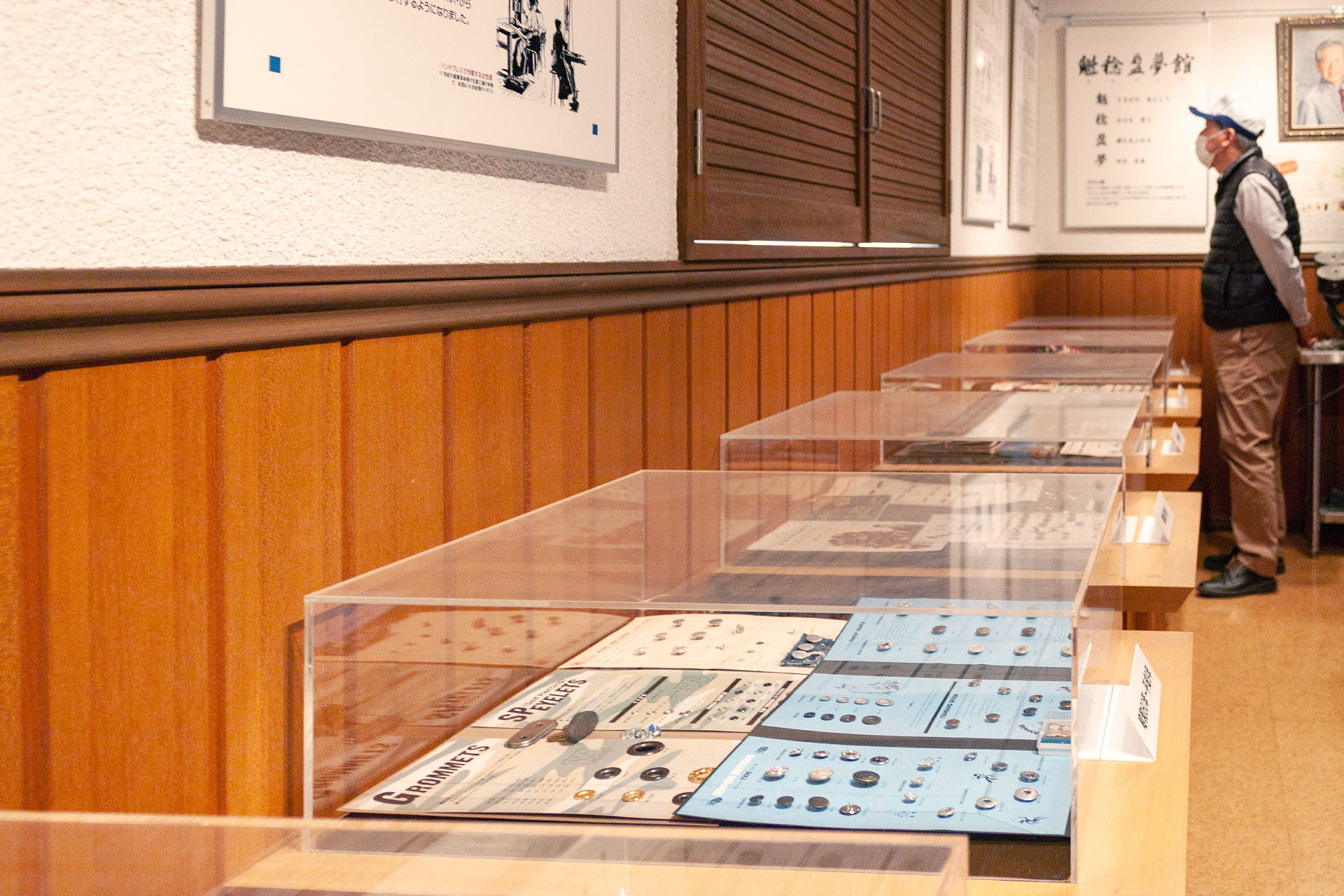
装置としては、今回ポイントになったのは照明です。一定条件で撮影できる機能から、自ずとピラミッドの形に行き着きました。

画像認識の技術を用いて検索ができるため、ベテランでなくともすぐに型番を知ることが可能です。連携アプリケーションでスマートフォンやタブレットからも閲覧できるので、営業の商談の際に活用してもいいかもしれません。
使用する部材や技術の選定、無料で使えるアプリケーションとの連携などは、小回りのきく弊社ならではのご提案ができたかと思っています。
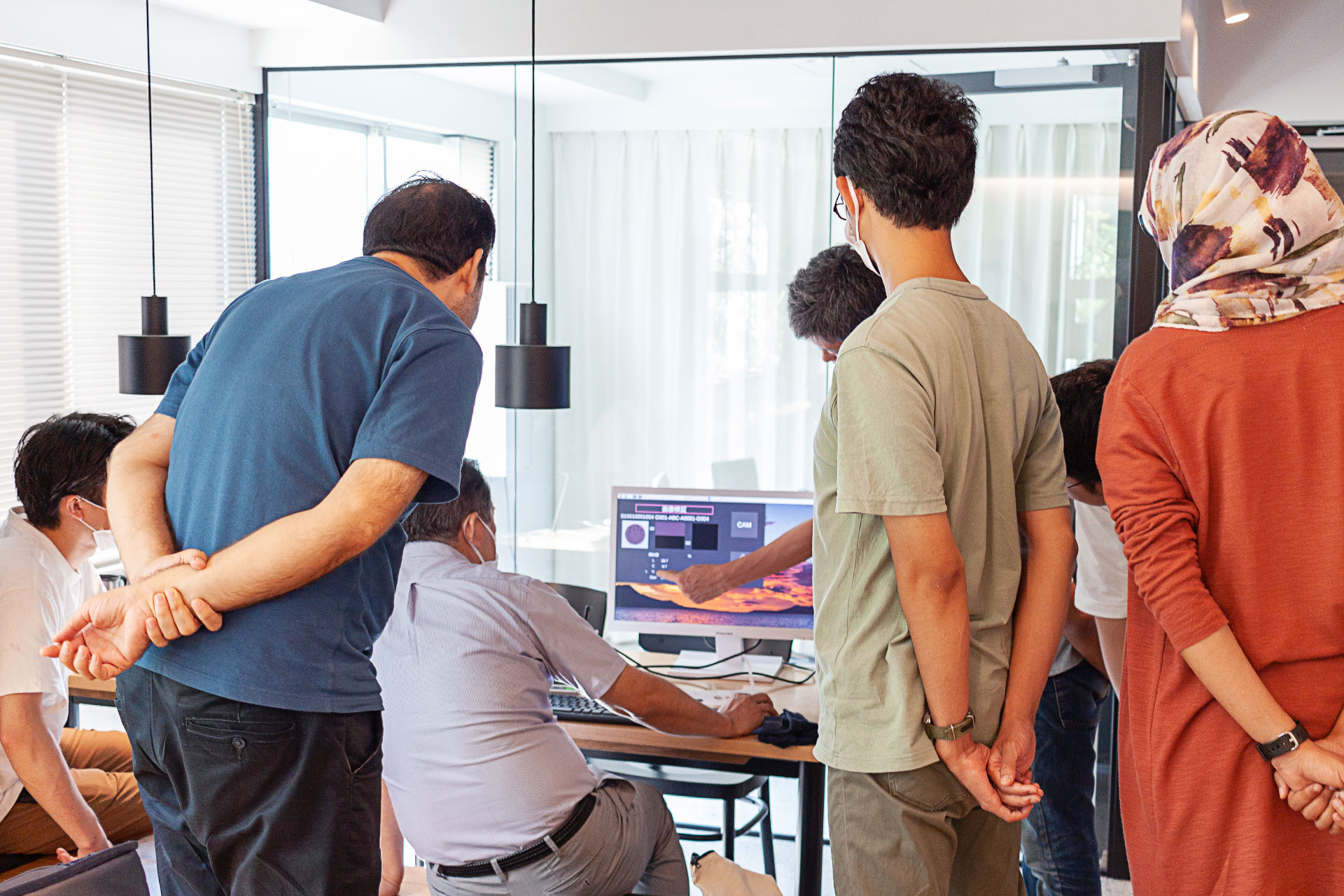
昨今、リスキリングの必要性が世で叫ばれていますが、デジタルスキルにおいては顕著です。テクノロジーによる業務の効率化・イノベーションの創出が期待でき、業界を問わず需要が高まっています。私自身破壊的イノベーションは中小企業こそ享受すべきと考えていますが、時間や手間、コストがかかり、志のある方が組織にいらっしゃっても壁が多いのが現状です。そうした現実を踏まえた時に、私の行っている伴走型のご支援はリスキリングに近いと感じました。
当システムはまだ納品したばかりで、本番はこれからです。今後とも伴走者として、カネエム工業様のイノベーション創出の一助となっていければと思っています
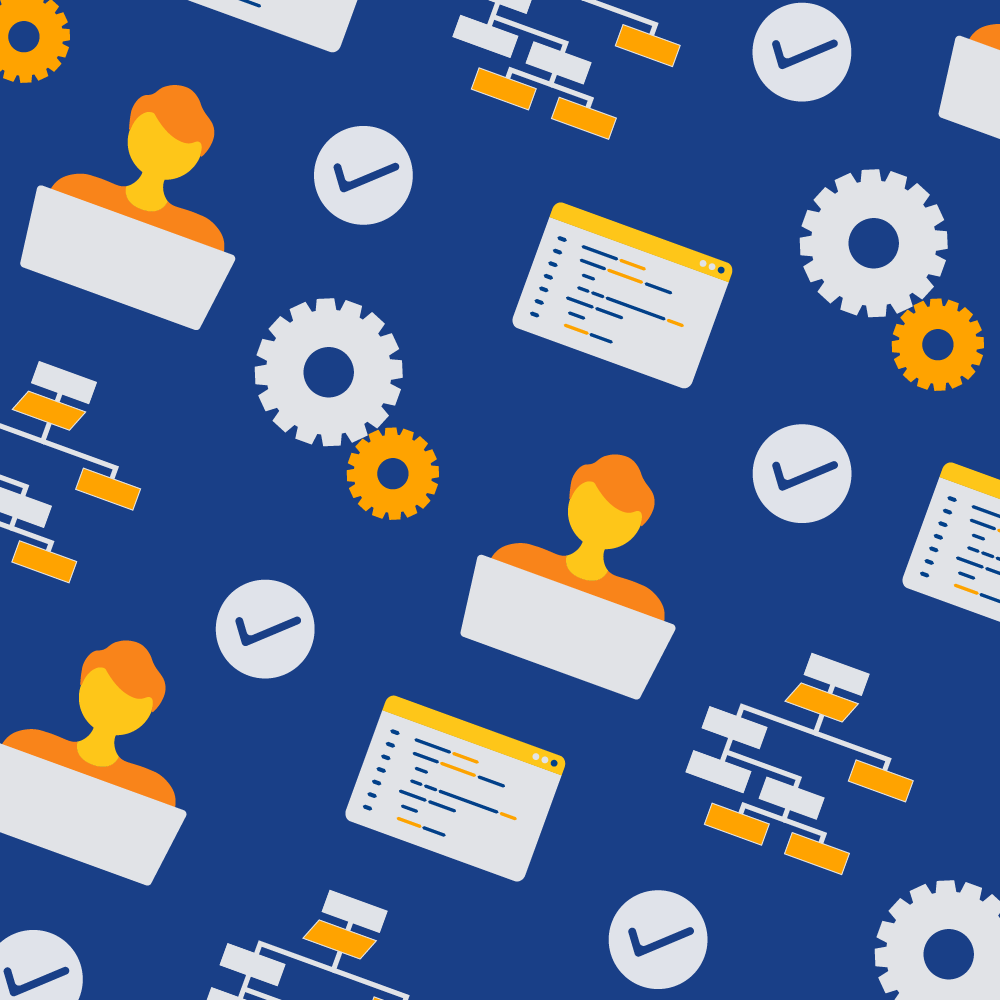
神戸大学様におけるLMS(学習管理システム)の構築・運用
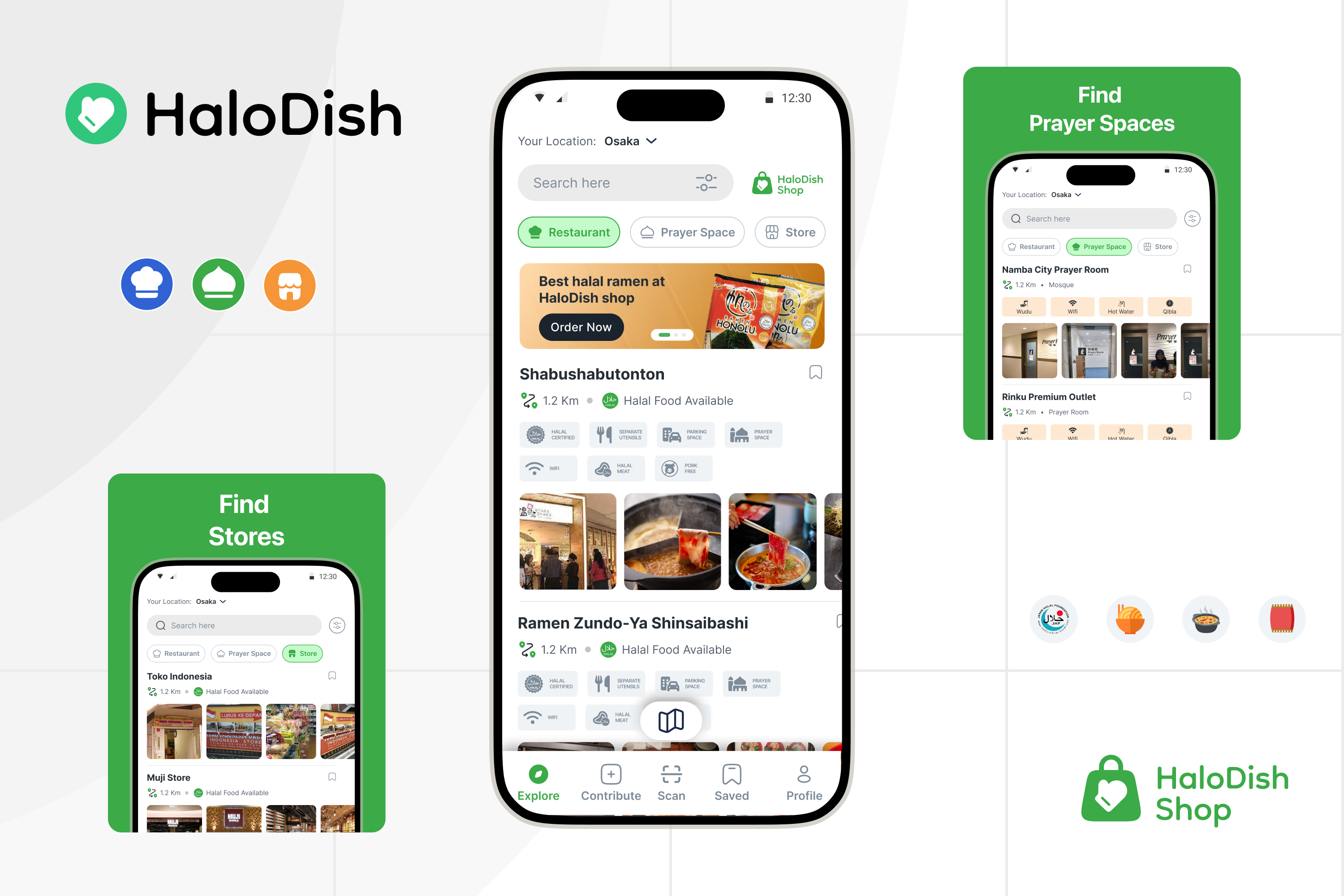